Another product innovation on display at this year’s AHR Expo in Las Vegas was Uponor’s Ecoflex pre-insulated PEX piping system. Here is a closer look at this insulated piping solution. https://www.youtube.com/watch?v=JEB-J1Kg3Es Read more
Radiant
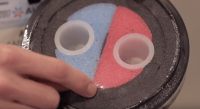
Another product innovation on display at this year’s AHR Expo in Las Vegas was Uponor’s Ecoflex pre-insulated PEX piping system. Here is a closer look at this insulated piping solution.
https://www.youtube.com/watch?v=JEB-J1Kg3Es
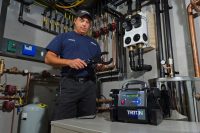
Recently, Toronto has had more high-rise construction projects underway than any other North American city. Last year alone, according to Canadian media, there were 130 high-rise buildings in progress. In the first quarter of 2015, the trend seems to continue. So it’s no surprise that Toronto’s suburbs are alive with the sounds of saws and Read more
Recently, Toronto has had more high-rise construction projects underway than any other North American city. Last year alone, according to Canadian media, there were 130 high-rise buildings in progress. In the first quarter of 2015, the trend seems to continue.
So it’s no surprise that Toronto’s suburbs are alive with the sounds of saws and pounding hammers. Within a half-hour drive from the heart of Toronto, custom home construction remains high.

Tim Rickards (l) and Fernando Valadai, of The Hydronics Group, deliver HDPE pipe and a Triton pipe fusion system.
As residential construction expenditure in Ontario and Quebec have pulled back only slightly since the record high in 2012, the custom home market retains its momentum. Enough so that some companies have made it their focus.
“We started to concentrate on the custom home market about a year ago,” said Bob Williams, VP of Tropical Heating and Air Conditioning. The 14-person firm used to serve a wide range of residential customers in the greater Toronto area — and still does when it comes to service work — but new installations are almost entirely in the half-million plus home market.

Bob Williams, owner and manager of Tropical Heating and Air Conditioning, gets ready to fuse an HDPE join as part of the home’s multi-unit geothermal system.
“Our staff has a wide knowledge base, especially in regard to hydronic applications,” continued Williams. “That specialty allows us to offer a great deal to clients seeking a more complex system, or systems, as is often the case.”
Concrete and complex
Custom work goes hand-in-hand with longer timelines. A project doesn’t need to be in the “starter castle” range to progress gradually, as the professionals at Tropical have learned. This is evident through ongoing work at a 5,000-square-foot modern residence between Toronto and Mississauga. Tropical started the job in 2012.
“This has been an on and off project,” said Williams. “But it includes some elements that stretch out the timeline, from concrete construction to geothermal.”

Adrian Navarette, senior installer for Tropical, uses The Triton pipe fusion system to join HDPE pipe and fittings after they’ve been dry-fitted.
Four ground-source heat pumps draw from 10 vertical bore holes to supply both hydronic and forced air systems. Polished concrete floors throughout the home include 8,600 lineal feet of half-inch Watts Radiant oxygen barrier RadiantPERT tubing. A 175 MBH NTI condensing boiler provides backup heat, DHW and heat for a snowmelt system. In all, 22 zones of radiant heat and three zones of air conditioning come out of two mechanical rooms; the main room downstairs and a smaller room on the second level.
“Space for components is the biggest challenge here,” said Williams. “And running all that pipe and ductwork through a solid concrete structure takes a lot of foresight. You need to use the available space as efficiently as possible.”
Close quarter connections
Geothermal Solutions, the drilling subcontractor, ran all the HDPE tubing from the exchange field to the mechanical room, where Tropical took over. The main flowcenter circulates the water/alcohol solution through the field and into a 26-gallon hydro separator. From here, flowcenters on each of the four heat pumps draw fluid as needed to condition the home. As a result, the room has one-and-a-quarter-inch HDPE pipe running in all directions.

Bob Williams, owner and manager of Tropical Heating and Air Conditioning, dry-fits an HDPE joint before fusing.
“To us, professional appearance is second only to functionality, and that’s hard to maintain with HDPE pipe,” said Williams. “A socket iron fusion system limits you to measuring, cutting and fusing pipe one piece at a time. We really wanted a system that allowed us to dry-fit an entire loop to make sure it’s all square, plumb and level, before fusing any fittings.”
While looking for a solution, Williams spoke with Tim Rickards, at The Hydronics Group, a Toronto-based wholesaler. In addition to supplying most of the equipment on the job, Rickards suggested that Tropical look at the Triton pipe fusion system, which uses radio frequency (RF) electromagnetic technology to fuse pipe instead of a hot iron.
The system is the HVAC industry’s first application of RF technology; a method of welding plastic pipe that’s been trusted in medical and industrial applications for decades. Radio frequency energy is emitted from the system’s portable control unit, and literally “excites” a thin strip of reactive metal that’s molded into each Triton fitting. The material heats up to the point of fusing the pipe and fitting together to form a joint that’s stronger than either the pipe or fitting alone.
With standard socket iron-fusing, two pieces of pipe are individually melted, then pressed together and allowed to cure. The Triton system allows the user to dry fit the pipe and fitting together, position them as desired, then simply clamp the tool around the fitting to complete the weld — with no risk of burns.
“The system really allowed us to tidy up the geothermal piping,” said Williams. “But it also cut our labor hours down. For example, while a technician is fusing one line, he can be simultaneously dry fitting the next one.”
Overload
According to Williams, Toronto’s geothermal installations are few and far between, as a result of small lot sizes. “Most of the geothermal work in Ontario is in more rural areas, where bigger yards are conducive to drilling or trenching exchange fields.”
At the concrete home, there was room enough in the yard to drill 10 bore holes, for a total 10-tons of geothermal exchange. But, the heat pumps in the home total 16 tons. As a result, BK Consulting Engineers — with input from Rickards and others at The Hydronics Group — designed a flexible system that overcomes the challenge.
The home’s main mechanical room includes three geothermal heat pumps; water-to-air units of two and four tons, and a six-ton water-to-water unit for the home’s extensive radiant floor system. An additional, four-ton water-to-air unit is on the home’s second story.

(L-R) Bob Williams of Tropical Heating and Air Conditioning, Tim Rickards of the Hydronics Group, and Mike Breault, Watts product manager HVAC Canada, look at building blueprints.
“We’re able to accommodate more installed capacity than the exchange field can supply based on two factors,” said Rickards. “First, the home is rarely, if ever, going to call for maximum input from all four units at once. Also, the condensing boiler is backup for the radiant system, which handles the brunt of the heating demand.”
To avoid getting what geothermal specialists call a “cold field” — where the exchange field becomes depleted of energy to the point that it can’t produce enough heat for the structure – the incoming water temperature is monitored. An aquistat on the main line into the mechanical room is programmed to shut off the water-to-water unit if dips below 32°F. At this point, the natural gas boiler supplies heat to the radiant system as well as an 80-gallon DHW tank and 1,200 square feet of driveway snowmelt.
In the summer, with the smaller cooling load and the water-to-water unit out of service, there’s no concern of overtaxing the exchange field’s ability to reject heat into the ground. While the home’s design heat load is 150,000 BTU, the cooling load is only 75,000.
“What this design does,” explained Rickards, “is cut down on exchange field expense, while using it to its full capacity without ever having to worry about overdrawing it.”
Double duty radiant
Each room in the home is an independent heating zone. Radiant tubing was installed on nine-inch centers, except where exterior walls consist of large expanses of glass. Here, six-inch centers were used on the perimeter.
“Right now, the system is supplying 100°F water to the radiant loops,” said Williams. “Once the home is occupied, that’ll fluctuate depending on the desired indoor temperature and outdoor ambient temperature.”
The owner also wanted the option to use the radiant system for cooling. The way the air conditioning system is designed, the water temperature in the slab can be dropped to 70°F without risking condensation on the floors.
“We’re able to focus on the custom home market because we can offer unique solutions,” said Williams. “And that’s a result of experience, relationships with other professionals, and a willingness to adapt to emerging technologies and practices.”
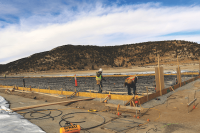
When most people think of radiant heat or hydronic snow melt, the usual applications come to mind: warm floors, heated sidewalks and snow-free driveways. The Big Bear Area Regional Wastewater Agency (BBARWA) in Big Bear, Calif., contacted Viega Radiant Design Services with a project that needed an innovative solution. A byproduct of the water treatment Read more
When most people think of radiant heat or hydronic snow melt, the usual applications come to mind: warm floors, heated sidewalks and snow-free driveways. The Big Bear Area Regional Wastewater Agency (BBARWA) in Big Bear, Calif., contacted Viega Radiant Design Services with a project that needed an innovative solution. A byproduct of the water treatment process is sludge which must be hauled by a truck to an off-site disposal area. BBARWA needed to reduce the water content and weight of the sludge, making it less expensive to haul. BBARWA tried several different methods to dry the sludge with only marginal success, so they decided to devise a new system that would be more effective, more efficient and would reduce the odor complaints.
Viega Radiant Design Services worked on the specifics of the slab-heating system design, focusing on what would be required to generate enough heat from the slab to meet the sludge-drying objectives. Viega design engineers used finite element analysis (FEA) to determine the optimum tubing size, spacing and install-depth in the slab based on the water temperature supplied from the diesel generator’s exhaust. Due to the shape and size of the 315- by 60-foot heated slab, it was clear that this project was an excellent application for Viega’s revolutionary Viega Climate Mat® system.

Within the first year alone, the new system saved approximately $200,000 in transportation and fuel costs. Additionally, the project received the California Water Association Desert Mountain Award for Innovation.

For more information on Viega system solutions, visit Viega.us.
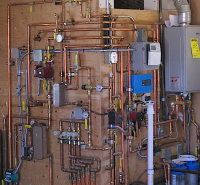
A leading solar integrator in the San Luis Valley of southern Colorado, Solar Gain Services has been offering solar thermal and photovoltaics to commercial and residential clients since 2007. When co-owner Luke Christy—NABCEP certified as both a solar heating installer and as a PV installation professional—received a call from a homeowner in Sagauche, Colo., to Read more
A leading solar integrator in the San Luis Valley of southern Colorado, Solar Gain Services has been offering solar thermal and photovoltaics to commercial and residential clients since 2007.
When co-owner Luke Christy—NABCEP certified as both a solar heating installer and as a PV installation professional—received a call from a homeowner in Sagauche, Colo., to reduce the overall energy usage footprint as low as reasonably possible, he had the tools and pedigree to meet the energy challenge. The 2,000-sq.-ft. home was built to LEED Gold standards, is heavily insulated, incorporates passive solar features, and has a grid-tied solar electric system to help offset the electrical energy consumption.

The solution, after taking into account available budgets and the highly efficient home, was to install a hybrid combi-system—for domestic hot water (DHW) and radiant floor heat—with a large amount of thermal storage. A copper single pass tube coiled within the tank serves as the primary means of heating DHW. Since the tank is purposely stratified, with the top of the tank always being charged first. “This technique works very well,” says Christy. A setpoint control activates a Caleffi 3-way valve to divert water from the single-pass through the tankless heater when the tank temperature is low.
Eight installed Viessmann Vitosol 100 solar collectors heat a 700-gallon custom stainless steel tank through a brazed plate heat exchanger, and Christy opted to go without a mod-con boiler for back-up heat to reduce costs. Instead, a gas-fired tankless water heater paired with a plate heat exchanger and some control logic serves as a back-up heat source.
A Caleffi iSolar BX solar controller charges the storage tank in two vertical stages to ensure that the top of the tank is always as hot as possible, even in winter. This helps preheat DHW through a single-pass copper coil heat exchanger, and in practice the thermal system is able to supply solar heated DHW for most of the year without any assistance from the gas water heater. “A Caleffi BX differential controller was selected because of its ability to charge the tank in upper and lower stages. This is accomplished via a Caleffi 3-way valve that diverts the flow to the tank from the water side of the heat exchanger. This helps the upper stage stay hotter at times of low solar harvest,” says Christy.
The radiant floor distribution system extracts heat from the storage tank until a low temperature setpoint is reached, at which point the gas-fired backup is enabled. “We have used Caleffi products since 2007, when they were introduced to us by Low Energy Systems in Denver. As a system designer I appreciate the extremely high level of quality of the products, as well as the comprehensive range of products available,” says Christy.
In addition to the solar controller, Christy relied on Caleffi components throughout the install, including four Caleffi thermostatic operator zone valves, an air separator, a backflow preventer and pressure reducing valve, a balancing valve, two thermostatic mixing valves, two 3-way zone valves, flowmeter, eight sweat union connectors—used for making plate heat exchanger connections—and a small automatic air vent. In fact, the radiant loop extracts heat from the storage through a second plate heat exchanger, and delivers it to the radiant slab through an assortment of Caleffi products — a thermostatic mixing valve, a balancing valve, a bypass valve and zone valves.
Challenges Met
One challenge in particular was the lack of a proper mechanical space for the system piping and components. Once the solar storage tank was in place, Christy realized that the space could be sheathed in plywood and used as a substrate for mounting components. However, we ended up needing all the available area of the tank exterior, which resulted in the system completely covering and wrapping around the tank.
Another challenge was the homeowners desire for solar collectors in a specific place, which was about 150’ away from the mechanical area. This resulted in a very long pipeline to and from the collectors, with potential flow and heat loss issues. These issues were resolved by using oversized and heavily insulated underground piping, as well as a larger collector loop pump.
Customer ‘Pipes’ In
This system has just gone through its third winter of operation and has been an outstanding success, with a glowing report from the homeowners and zero service calls. The homeowners report that they are comfortable all year round and only refill their 250-gallon propane tank once a year. The single tank supplies all the fuel for the heating and DHW backup, as well as a gas range and a gas fired clothes dryer, so the savings would seem to be significant. On future installations of this kind we will be installing a web-connected energy meter, which will enable us to collect enough system data to translate the daily energy harvest into the corresponding economic benefits.
“The homeowners have had nothing but good things to say about the system. We did not have a single callback on the system until a severe windstorm damaged some collector mounting hardware three years after the system was commissioned. When we checked system operation at that point, everything was still performing properly, with no leaks or control glitches,” says Christy.
Caleffi Excellence
According to Christy, Callefi’s commitment to innovation and constant improvement is extremely important, as is their commitment to education and training. The Coffee with Caleffi webinar series and their Idronics publications are a really valuable resource for the hydronics professional constantly looking to hone his/her skills.
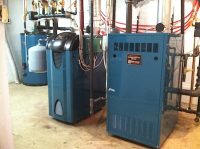
Long Island’s rich hydronic heritage can be seen in the houses that cover the island, as well as the plumbing and heating shops that serve them. Common is the moderately sized, turn-of-the-century house that’s seen addition after addition, with as many changes to the heating system. The family-owned hydronic shops run by passionate “wet-heads” continue Read more
Long Island’s rich hydronic heritage can be seen in the houses that cover the island, as well as the plumbing and heating shops that serve them. Common is the moderately sized, turn-of-the-century house that’s seen addition after addition, with as many changes to the heating system. The family-owned hydronic shops run by passionate “wet-heads” continue to leave their mark on the heating landscape.
Hunter Botto will be the first to attest to this. He and his brother, Roger, are third generation owners of Botto Bros. P&H, in Hicksville, NY. Their grandfather started the company in 1937, and they purchased ownership in the ’80s. Today, it’s a 10-person, multi-faceted firm that’s commercially and residentially focused. Plumbing and heating is their bread and butter, but kitchen and bath remodels and generator installations keep them busy year-round.
“One thing we’ve found is that diversifying helps build a bigger network of clients,” said Hunter. “We’ll land a remodeling job, and later in the year they’ll call us back to service a boiler or install a generator.”
In early February, Botto technicians were completing a generator installation when the owner asked them to check their radiant heating, and if a gas $1,400 gas bill was normal for a 3,500-square-foot home in January. When they stepped into the home’s mechanical room, what they found was so bizarre that they texted Hunter a bunch of photos.
Steam to radiant disaster
The circa-1910 house had been expanded and remodeled a number of times, with the heating system constantly gaining complexity. The original cast-iron steam radiation was accompanied by a jumble of air handlers and two different in-floor systems, none of which operated properly. The floor didn’t heat well, and the two-pipe steam system was banging. Oddly enough, the entire system was served by one oversized steam boiler.

A Burnham Independence supplies steam to cast-iron radiators, while an ES2 heats in-floor zones and DHW via a Burnham Alliance sidearm tank.
“I had to check it out myself,” said Hunter. “The boiler – which was 20 years old – was twice the size it needed to be. There was no proper equalizer; the four-inch header went right into the boiler, and three, two-inch supplies Teed off the big main. But it gets better.”
“Instead supplying DHW, the steam boiler’s internal coil was piped out to a 30-gallon buffer tank – which was just an old indirect-fired water heater. A circulator moved water from the tank to two radiant supply manifolds; one which supplied PEX under the marble kitchen floor, another for a staple-up zone in the dining room. The PEX didn’t receive the flow or temperature it needed. DHW was supplied by an old gas-fired water heater, and an upstairs den was heated by a single gas-fired air handler.”

Because the home uses both water and steam heating elements, Botto Brothers used two boiler to share the load.
During Hunter’s visit, the homeowner decided she wanted to lower her fuel bills and restore heating function by replacing the system. To hold her over for a few weeks until they could design and install a new system, Hunter de-rated the existing boiler to 50 percent of its 300,000 BTUH capacity. He then completed a heat load calculation in the rooms with radiant heat, and measured the radiators.
Share the load
“Instead of converting the radiators to water, we decided to divide the load between a new steam boiler and a new water boiler,” said Hunter. “We started on February 17th and finished five days later. The homeowner headed to Costa Rica during the process, which made life easier for us.”
Once the old boiler was removed, Botto Bros technicians Mike Depaulis, Bryan Scheafer and Brian Single installed a 105 MBH, natural gas-fired Burnham ES2 water boiler. The unit now supplies DHW via a 50-gallon, Burnham Alliance indirect-fired water heater, and working heat for the in-floor system.
“The ES2 is a real workhorse,” said Hunter. “Efficient, easy to install, and ridiculously dependable. What else do you want from a boiler?” Updating the radiant system included the addition of a pump; one for each manifold. Mixing valves are now used to temper down the 180°F supply temperature. The kitchen supply temperature averages 115°F, while the dining room – with wood floors – requires 140°F.
After the water side was squared away, they turned their attention to the radiators. Any air vents were removed, and supply valves were replaced. Next to the ES2, a 140 MBH Burnham Independence was installed for the 310 square feet of connected radiation.
“We couldn’t promise the owner of this job tropical weather upon her return, but a comfortable house and a lower heating bill were a given. The project even qualified for a 900.00 dollar rebate from National Grid, the local utility,” said Hunter. “
Worthwhile affiliations
Hunter is a 15-year PHCC member who has served as local and state president, and has been on the National PHCC Board of Directors. Currently, he serves as the local Zone Director.
“PHCC has allowed me to have open communications with contractors from all around the country,” said Hunter. “Over the years, their guidance and recommendations have proven an invaluable asset to have.”