By Norman Hall A competitor recently asked how we can afford to spend so much time and money training our employees and our customers. My response is, “How can you afford not to train your people?” I would argue that education should be a prominent expense item for all contractors, wholesalers, and representatives in the Read more
training
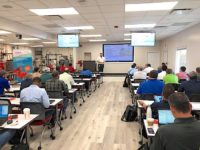
By Norman Hall
A competitor recently asked how we can afford to spend so much time and money training our employees and our customers. My response is, “How can you afford not to train your people?” I would argue that education should be a prominent expense item for all contractors, wholesalers, and representatives in the HVAC and plumbing world. In this industry, where product and technical information can feel like a tsunami, customers rely on us to act as trusted advisors guiding them to the best solution. Our staff cannot simply exist as a walking, talking brochure. Arming our people with the knowledge and empowerment to think critically and to act with integrity has resulted in a thriving business and a dedicated customer base here at R.L. Deppmann.
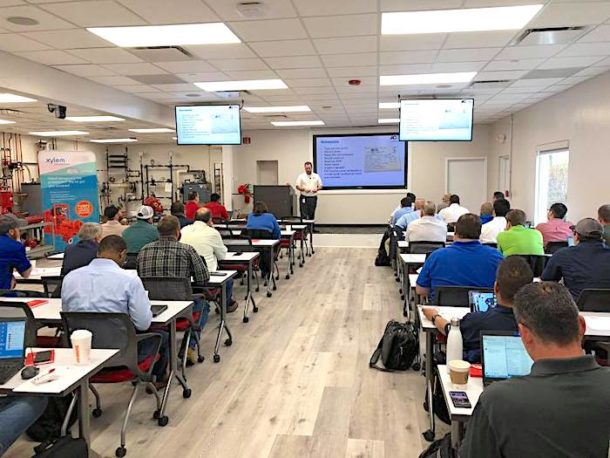
“OK, Show Me the Boiler and I’ll Help you out.”
A few months ago, I was at lunch with a commercial mechanical contractor. By the way, it was a real lunch, not a Zoom meeting. The contractor started asking about the importance of the R. L. Deppmann seminar series for the winter season. He told me the story. Last fall he purchased some equipment for a project from a competitor. The equipment was installed and ran fine for a short time. In the spring he received a call from the owner. There were complaints of sporadic shutdowns of the boiler. The younger salesperson who took the original order was called out to the jobsite to assist in troubleshooting.
The rep stood in the mechanical room and asked the contractor to take him to the equipment with the trouble. The response was, “it’s right behind you.” Imagine the look on the contractor’s face. The young salesperson was embarrassed and the customer lost confidence. No one wants this to be a story in their company.
Starting in the Industry
Employees are valuable assets of any successful company. Today, it appears there are more positions available than people to fill them. The result is a younger work force that is changing jobs and careers. The person you are hiring may have little knowledge of the industry and certainly little knowledge of your company.
Exposing this new employee to knowledge about the company, the job, and the growth opportunities is paramount. The new employee will leave you or you may leave them if they are not successful in a short time. There is a roadmap to training if you are willing to invest in it.
The New Employee Education Road Map
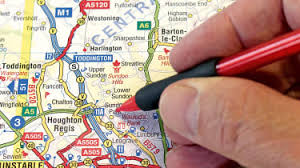
Image Credit: Carbuyer
Our company, R. L. Deppmann, is a successful manufacturer’s representative of hydronic, steam, and plumbing products in Michigan and Ohio. Our customers call us to help them solve problems because we have, and teach, the knowledge they need. How does this happen? Our hiring pool on the sales and engineering end is no different than other companies, but the training program is.
- Start with core values and what the company is all about. Our new employees are purposely exposed to the company business and culture three times in the first few weeks of their career. The HR department presents, the managing supervisor presents, and a senior manager describes the business and culture.
- Know the team that supports you. Our customers are contractors, wholesalers, and owners. It is important for the new inside or outside salesperson to understand the various departments of support.
- The new sales rep spends a short time in the warehouse, learning, seeing, and touching the products. They also begin to learn the ERP and CRM systems.
- Next, they move into the startup and warranty (service) department. Here they begin to see installed products and how they are commissioned. With the Service Tech as their mentor, the employee will gather knowledge of the terms used in the industry, proper installation, and troubleshooting. There is also a chance to interface with customers.
- Customer service/inside sales is the next stop. Here they begin the process of satisfying customer requests. They learn product, parts, and our business systems. They work in a team with open conversation about the hundreds of different product types and customer issues. The employee learns to help the customer make a better decision about what they are asking for.
- We have a strong new construction business. The salesperson will learn the plans, specifications, proper selection and sizing, proper detailing to avoid issues, and pricing. Here there is the baseline process of speaking with contractors, wholesalers, engineers, and coordinating with other employees.
- By this time, the employee is well into their training period. They now go out on calls with a senior sales rep. They are prepared with some understanding of product, installation, troubleshooting, selection, and quoting. Daily discussions with the senior rep will fill in the features, benefit, and competitive landscape for company and individual success.
- Now the employee is prepared to be a resource for their customer. They understand who knows what and the resources available to satisfy the customer’s needs. The new employee feels like they are part of a team. They may have developed a friendship with other employees. They feel like they belong.
Getting Started: How to Create a Training Program
This program may seem difficult to start. We developed this over many years. The departments a new employee is exposed to changes with their job. An accounting employee will go through the core ideology training. They may not experience the customer service department but warehouse experience in return goods or the purchasing process knowledge may help them do their job better.
Start with that core ideology process. Make sure the employee understands who you are, where you fit in the industry, and what to think about when making decisions. Next, just pick one support department for the job and list what they need to know about it. Communicate with all the department employees what the goal is and just try it out for a couple weeks. You will develop your own program.
Next quarter I’ll share the continuing training program we use once the employee is in the job full time.
Norman Hall is an engineer and leader at the R. L. Deppmann Company, a manufacturer’s representative, in Michigan and Ohio. Norm has assisted in the design and troubleshooting of hydronic and steam systems for 45 years.
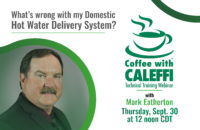
Brought to you by the Coffee with Caleffi™ Webinar Series Many multi-family buildings with medium to large domestic hot water (DHW) systems can suffer from numerous problems. Is your commercial DHW system giving you trouble? Then it’s time to receive the benefit of Mark Eatherton’s 49 years of hot water heating and troubleshooting experience at Read more
Brought to you by the Coffee with Caleffi™ Webinar Series
Many multi-family buildings with medium to large domestic hot water (DHW) systems can suffer from numerous problems. Is your commercial DHW system giving you trouble? Then it’s time to receive the benefit of Mark Eatherton’s 49 years of hot water heating and troubleshooting experience at the next Coffee with Caleffi™ webinar on Thursday, Sept. 30 from 12 noon – 1:00 p.m. CDT.
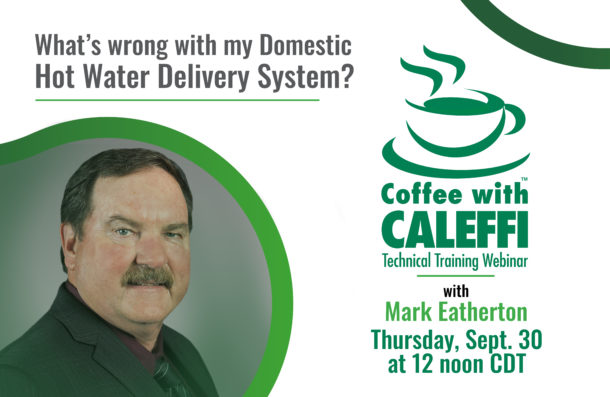
There aren’t many situations that Eatherton hasn’t encountered and resolved in his nearly 50 year career in the industry. He loves to teach, write and educate and has been doing so for over 25 years. Eatherton is responsible for designing, managing and troubleshooting tough plumbing and hydronic related problems for Advanced Hydronics, Inc. (Denver, Colo.).
The monthly educational webinars are free and are intended for engineers, contractors, designers and wholesalers. A Certificate of Attendance is emailed to attendees following the event for continuing education audits.
Please visit our website at www.caleffi.us for schedule details and registration.
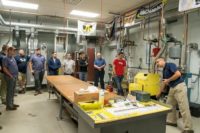
The Northeast U.S. has been the hydronics stronghold in America since boilers were first put to use as a source of heat. To serve the interests of trade professionals, especially those just entering the field (though by no means limited to introductory training), the Pennsylvania Petroleum Association (PPA) technical education center (PPATEC) has substantially expanded Read more
The Northeast U.S. has been the hydronics stronghold in America since boilers were first put to use as a source of heat. To serve the interests of trade professionals, especially those just entering the field (though by no means limited to introductory training), the Pennsylvania Petroleum Association (PPA) technical education center (PPATEC) has substantially expanded its facility in the Harrisburg, Pa. area.
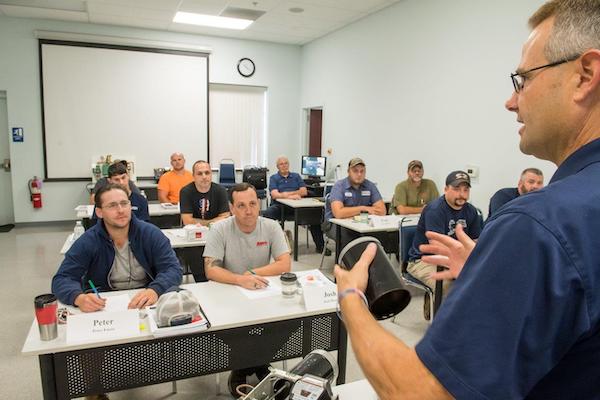
For over 35 years, PPA has offered oil-fired hydronics and forced-air equipment training at the facility, serving thousands of trade professionals who came to hone their skills while under the skilled guidance of expert instructors. The equipment in PPATEC’s oil-fired training room is connected to a large, primary hydronics loop, enabling all of the heating systems to operate under real-world conditions. PPA won accolades as having one of the best facilities of its kind, and with quality of training second to none. Currently, classes range from one-half day to two weeks in length.
Though PPA is recognized for excellence in oil-fired training, association managers recognized the need to evolve their programs to train for all types of energy sources. This included a greater focus on gas-fired equipment, air conditioning, and electrical components, and to accommodate larger classes. By late 2019, preparations for the new facility had begun.
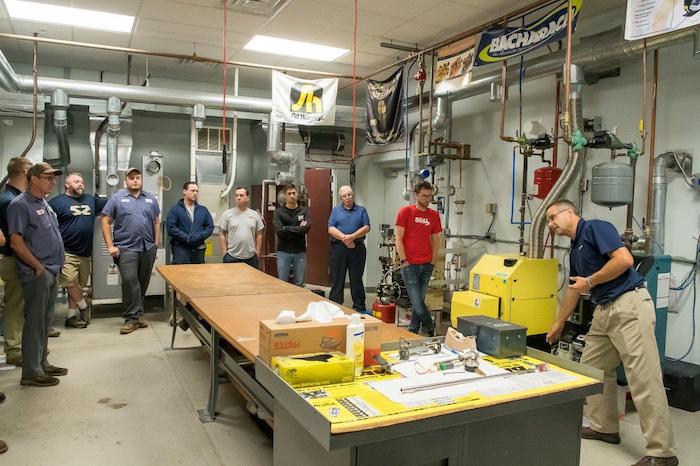
Though, soon after the association initiated an expansion to accommodate the need for gas-fired training, COVID-19 swept in with hard repercussions worldwide. “Among the many concerns we had, we had to consider the negative impact on the new facility’s mission, and had we chosen exactly the wrong time to expand?” asked PPA’s Executive Vice President Ted Harris. He and Trainer Alan Mercurio certainly had their hands full since the expansion project began in early 2020.
As it turned out, the forced pause in association activity allowed its managers to turn their full attention to making sure the new facility, including a modern classroom and a working lab, would exceed the needs of trade professionals “when they returned; not if,” insisted Mercurio.
Through last year, as the economy’s pace slowed to a crawl—sure enough, and just as predicted—a silver lining emerged. Addition of the association’s new gas-fired hydronic facility was not only completed, but attracted the attention of manufacturers, reps, wholesalers and installers who wanted to help. And now the expanded facility is teeming with students.
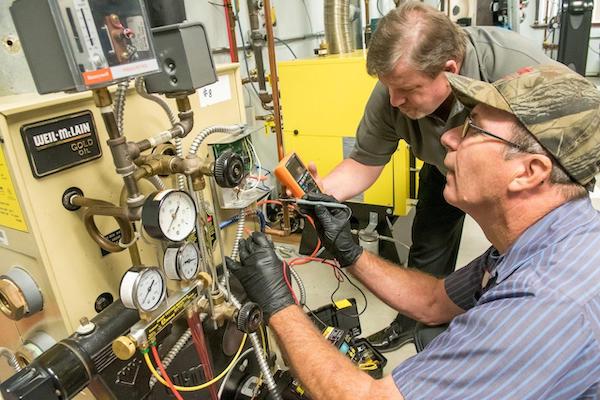
The new facility – with Ed Howell as the key “gas-side/HVAC” instructor – offers plenty of room for students and additional instructors and serves as the ideal training venue for a wide range of classes. Students receive training on all facets of gas-fired equipment and mini-split system operation, service work and troubleshooting.
As many veterans to the mechanical trades will affirm: it’s easy to install new equipment; it’s another thing entirely to know how to diagnose and treat ailing systems. Students who attend classes at PPATEC’s now-enhanced training facility get the best equipment service training available anywhere.
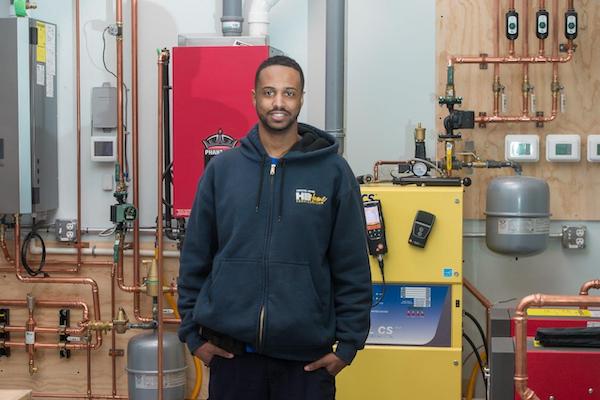
Classes resumed early this year, with lots of interest in troubleshooting and service work, allowing “students” to hone skills in a lab setting that allows instructors to replicate a wide variety of especially challenging conditions. “The repeatability of any technical challenge is one of the greatest assets of our facility,” said Mercurio. Not only do students get to work through a problem until it’s fully solved, giving them the best hands-on experience with it, but instructors can also add new challenges to reproduce a real-world encounter.
Trade Pros Give PPATEC Two Thumbs-Up
One trade professional who recently completed training at PPATEC’s workshop—on the “oil side”—is Damon Allen, an 18-year air-side veteran of the HVAC trades based in Randallstown, MD. Allen, an HVAC service technician with H. B. McClure Company said, “I was glad that H. B. McClure saw the advantage of sending me to PPATEC training because it allowed me to expand confidently into hydronics work. The three-day service course, focusing mainly on service and maintenance of oil-fired equipment, was extremely valuable.”
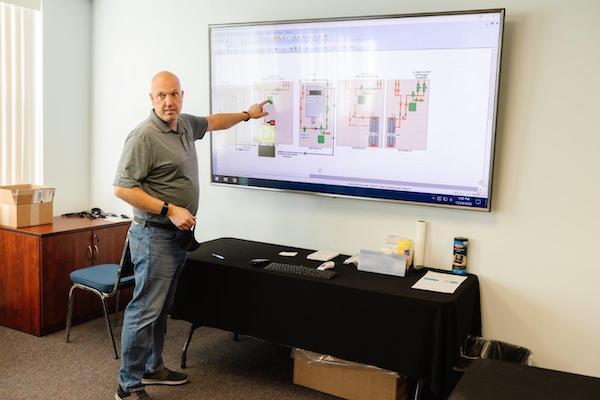
Another veteran of the trades—and also a military vet who served four years in the U. S. Marines—is Shane Lang, a service technician with Philipsburg, PA-based J J Powell Inc. Last fall, Lang attended PPATEC’s two-week training, affectionately referred to by attendees as “burner school.” Lang said that, “A number of trainers, each coming from different manufacturers, provided detailed instruction in trouble-shooting, maintaining and servicing equipment—from boilers and furnaces, to burners. The course taught me a lot about burner technology, and how to keep the systems running at their best.
“The quality of training [at PPATEC] was excellent,” added Lang. “I’d recommend it to anyone ion the HVAC trades. I’ll hope to return for more instruction there.”
Yet another military vet, and rather new to the HVAC trade, is Jeremy Perez, an ex-Marine and NATE-certified HVAC tech with Towanda, PA-based Energy Distribution Partners. “The training at PPATEC goes deeper than NATE schooling, so I appreciate that. The hands-on experience is valuable, and the simulator training—which allows us to run through various conditions with live voltage—is very helpful.”
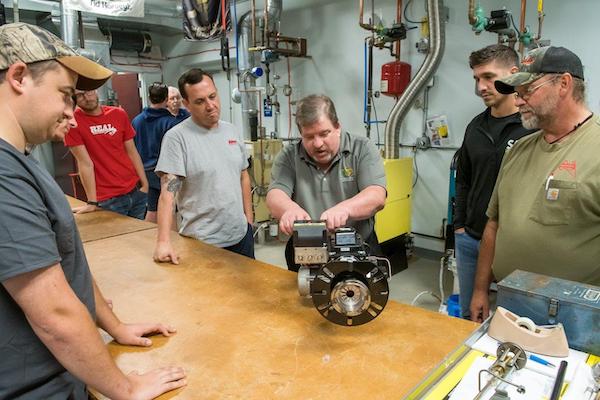
Cody Watts, also an HVAC technician with Energy Distribution Partners, was attending a two-week PPA course with Perez. After serving for a decade on shale gas drilling rigs where he worked routinely with industrial pumps and three-phase equipment, Watts chose to enter the HVAC trade and quickly found that PPATEC’s training played a valuable role in helping him make the transition. “Most beneficial for me has been the hands-on experience I got at PPATEC, the simulators for real-world troubleshooting, and the binder that’s full of material—tied to each aspect of the training.”
“Throughout the training – whether it’s a few days or a few weeks in length – we provide all students with plenty of review and instructional material,” assured Mercurio. “It’s one of our hallmarks. We hear routinely [from students] that it’s greatly beneficial.”
Veteran benefits/”Gateway” program
Mercurio says that they’ve trained a substantial number of military veterans at the PPA facility. “Aware of that, one of Ted Harris’ visions for training here is to develop a 10-week workforce development program specifically for vets. The plan [now underway] is to meet conditions for GI Bill veterans benefits so that ex-military students can use funds available to them for extensive training, even to include travel and hotel expenses.”
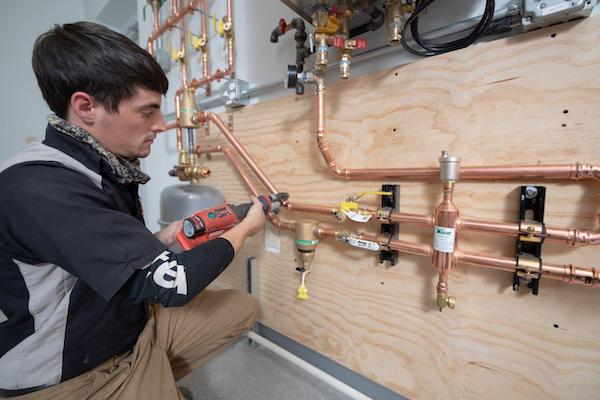
PPATEC received approval and recognition from the PA Dept of Education in February 2021 as a private licensed school. This allows PPA to admit students to a 10-week, entry-level trade course, one not paid by a current employer. PPA is set to introduce the course in 2022. “This segment of the market [individuals not currently employed in the HVAC industry] is one we very much want to cover, ideally allowing graduates to be hired by one of our members,” added Harris.
Industry support is crucial
Harris explained that industry support from manufacturers, wholesalers and contracting firms plays an important role in making PPA’s mission viable. “Our purpose here is to offer valuable, maybe even life-changing instruction, but without the help of our industry partners, we simply couldn’t do it.”
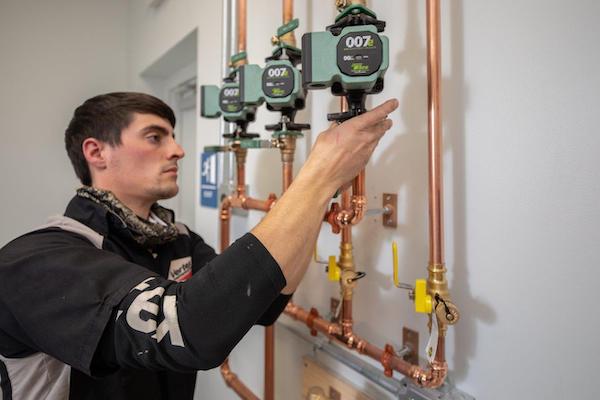
Key supporters of the association include Taco Comfort Solutions, NTI, APR Supply, Fujitsu, Sid Harvey, Rheem, Crown, Rhoads Energy, Tevis Energy, Ferguson, Navien, Friedrich, Burnham, Honeywell, Energy Kinetics, Ray Murray Inc., R. W. Beckett, Field Controls, Mitsubishi Electric, and F.W. Webb Company.
“Overall, the support we receive from manufacturers and other industry stakeholders is terrific,” added Harris.
Taco Gear + Dave Holdorf Expertise
Shortly after learning of PPA’s desire to install a new hydronic training lab with gas-fired (and ductless HVAC) technology, Johnny White, Jr., CEO of Taco Comfort Solutions, asked for a list of needed components.
Taco residential systems trainer Dave Holdorf also got wind of the project. He and White soon offered not only to provide many of the essential hydronic system components—including many of their newest, most advances ECM circulators—but that Holdorf would also make trips from Long Island to deliver the materials and to serve as a consultant to the installation firm (Stevens, PA-based Vertex Mechanical) chosen to assemble all of the new, hydronic lab equipment. “Johnny’s words to me were, ‘Give them anything they need, and all the support they can use,’ said Holdorf.
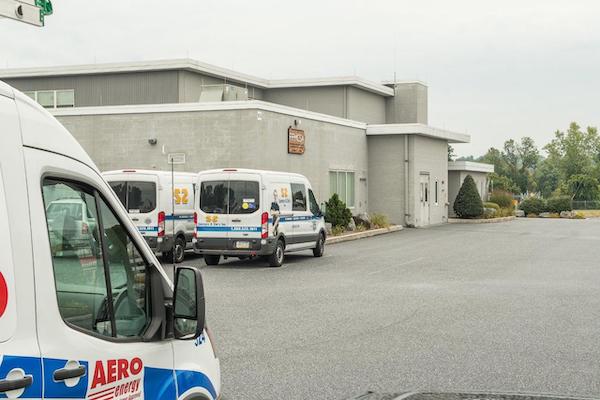
“I designed the facility to represent realistic conditions as closely as possible, with an emphasis on real-world variations and practicality,” said Holdorf. “For instance, I designed-in system circulation with zone valves for one of the cast iron boilers, and zone valves for the other. And, for the NTI boiler, the addition of a hydroseparator—just because it’s a possibility that a service tech will encounter scenarios like these in the field.”
Vince Youndt, owner of Vertex, explained that they wanted to do the installation work; he chose HVAC/hydronic systems installer Jared Fox as the lead technician. Holdorf used Taco’s FloPro Design software to develop a spreadsheet with all of the needed components and to design the systems, with many integrated boilers, as well.
Steve Wieland, MidAtlantic sales manager for NTI Boilers, Inc. was also one of those who, after learning of the association’s needs, quickly expressed interest in providing support. Not long after that, the very first, newest FTVN-110 boilers were rolling off the line. He received two of them, and soon delivered one of the company’s newest, most advanced mod-con boilers—an up to 11:1 turndown system with sizes of 85-200 MBH (purely) for heat, and 110-200 MBH for combi (heat with domestic water). “We’re delighted to support them, and I must say that after seeing the installation work there, the new lab is extraordinary. It’ll serve them well,” said Wieland.
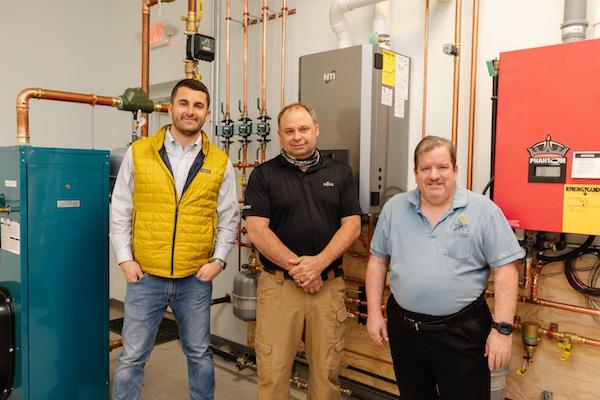
The new hydronics lab now includes a variety of mod-con gas boilers (including the latest from NTI) and two that are atmospheric. And, according to Mercurio, software in equipment sends diagnostic signals to the cloud for instant access to operational conditions, quickly availing information to any portable device.
Simulators, too
PPATEC has also added three HVAC simulator units from iConnect Training. According to Harris, the new simulators allow students to better understand the theory and operational techniques for electrical components, gas furnace systems and heat pumps. The simulator workstations feature a variety of live-fire conditions for heating and cooling systems:
- 9240 HVAC Electrical Control Trainer This simulator—with A/C, heat pump, basic electricity, commercial electricity and supermarket refrigeration modules, among many others—allows a trade pro to “build” a complete HVAC system by connecting the wires to the appropriate modules. Once complete, instructors can demonstrate how everything is working properly, or if there are failures, what can be done to solve the problem.
- 9250 Gas Furnace Controls Training Systems Specifically built to replicate a high efficiency gas furnace with air conditioning, this simulator allows an instructor to walk students through wiring from one module to the next until a system is fully operational. The sim has an actual gas burner to replicate close-to-real conditions. Students then learn about adjusting gas pressure and combustion air, and how to properly use a multi-meter to check flame rectification and a variety of faults, among other things.
- 701 Table Top Heat Pump Trainer Instructor use this simulator to demonstrate the proper way to use refrigeration gauges. Super-heat sub-cooling is also taught. Students can see refrigerant going through glass tubes to help them understand at which point the refrigerant flashes off from a liquid to a vapor and back to a liquid. A reversing valve gives an instructor the ability to explain its purpose, and troubleshooting techniques.
PPA and PPATEC members
Currently, PPA has about 400 members, most of which are fuel delivery firms who offer HVAC services. Though, there’s a wide range of wholesaler and manufacturer members. “Statewide, there are about 5,000 HVAC service and installation companies; we invite them all,” said Harris. Through membership, all member firms benefit through their alliance with PPA through the availability of training for techs, and through a greatly-improved, higher-skilled workforce.
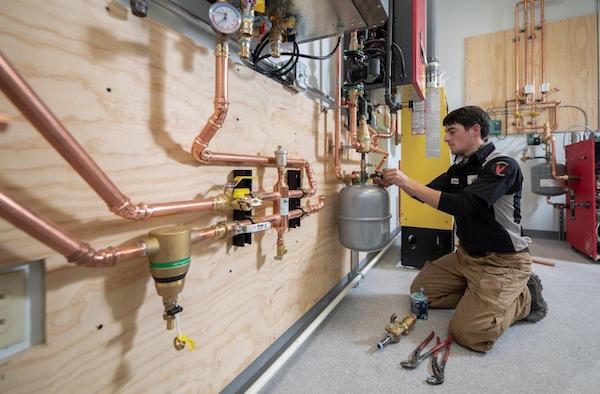
“Fortunately, we now have over 40 HVAC contractor firms that don’t offer fuel delivery who’ve joined the association as PPATEC members. This new membership category, introduced in 2019, now provides installing contractors the opportunity to receive various PPA benefits such as discounts for technical training,” added Harris. “We hope to continue to expand [membership] regionally—say, within a four-hour radius of Harrisburg.”
Equipment and components
Generous donations of HAVC and hydronic equipment, and components, came in from many manufacturers. “We were thrilled that, shortly after announcing our plan to expand the training facility, offers began to stream in,” said Harris.
Key contributors included Taco, which supplied a wide range of ECM circulators, zone valves, zone controls, hydraulic/dirt and air separators, boiler feed valves and other hydronic components. APR Supply chipped in with ductless mini split systems, one each from Fujitsu, and Friedrich. James Miracle and Mike Woods from Mitsubishi Electric contributed a two-head multi-zone system. John Monaghan, with Crown boilers, informed them that they had two atmospheric boilers and one condensing boiler to provide. Condensing boilers were also given by Energy Kinetics. Steve “Wheels” Wieland called from NTI to say that one of their newest boilers would soon be on its way (its only other twin, just off the line, would serve as a demo unit for Wieland’s own training efforts); he made the delivery personally.
Doug Oest called from Lancaster, PA-based Burnham Corporation to say that they would provide a very substantial nine-section, cast iron light commercial V9 gas boiler. Matthew Nowicki and Kurtis Mumma called from Ferguson HVAC to say that they would provide (in partnership with Navien) a tankless gas water heater. In partnership, Rheem and Sid Harvey supplied a tank-type gas water heater.
Residential and commercial gas burners were donated by R. W. Beckett. A power vent was donated by Field Controls; RegO and Fischer regulator products were donated by Ray Murray Inc. and F.W. Webb Company. A variety of Honeywell thermostats were given by Venco Sales Inc., and Viega ProPress fittings were discounted by RF Fager Company. A Monessen vent-free log set was donated by Ray Murray Inc. A Premier propane cooking range was donated by Martin Appliance.
John Vastyan owns Common Ground, a plumbing and mechanical, hydronic, HVAC and geothermal trade communications firm based in Manheim, Pa. He can be reached at JohnV@SeekCG.com.
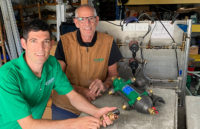
No doubt about it, COVID-19 quickly changed the way we work, and play. Travel and in person visits came to a screeching halt. Professional offices, suppliers, even many working shops closed their doors to visitors. Training in the not to distant past was done, for the most part, in person. Conveniently, most trainers adapted quickly Read more
No doubt about it, COVID-19 quickly changed the way we work, and play. Travel and in person visits came to a screeching halt. Professional offices, suppliers, even many working shops closed their doors to visitors. Training in the not to distant past was done, for the most part, in person. Conveniently, most trainers adapted quickly to offer online training options. Many of the companies in our industry were already familiar with platforms like Go To meeting. This made the switch to virtual training fairly easy for those trainers.
Some trainers I met through the ESCO group devised hybrid virtual training events. With a few cameras, one that would follow you around a room they kept the hands on training available also.
An instructor in front of a piece of equipment would be led through the troubleshooting in real time, clever and almost like being there.
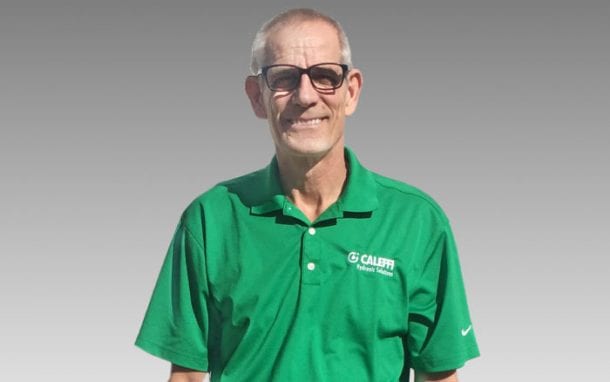
The question remains, what happens going forward in the training world. In some cases offices that made the change to virtual workspaces plan on staying that way. In some larger cities’ that has created office space vacancies and those building owners are scrambling to repurpose those spaces to get the rent rolling back in.
In cities like San Francisco it was a tough slog to see more than two engineering firms in a day due to traffic and parking logistics. With online, virtual sessions you can present to their entire staff as well as any locations they have scattered around the world.
I’ve started limited travel myself for training events. I doubt cramming 30 or more folks into a hotel meeting room will ever be attractive anymore. In some cases moving the training into the shop area, parking lot or a large cafeteria area is a good option to allow attendees to spread out more.
I doubt anyone knows for sure how this will shake out or what “bug” will hit us next that makes people want to avoid crowded rooms and spaces, but plan on having options. Come up with new ways to engage the attendees. Not being able to see faces, expressions and not getting that in person feedback changes the game for a trainer. Add polls to your training to get some interaction and a feel for the groups. Consider multiple speakers or trainers to get some back and forth conversation in your online trainings.
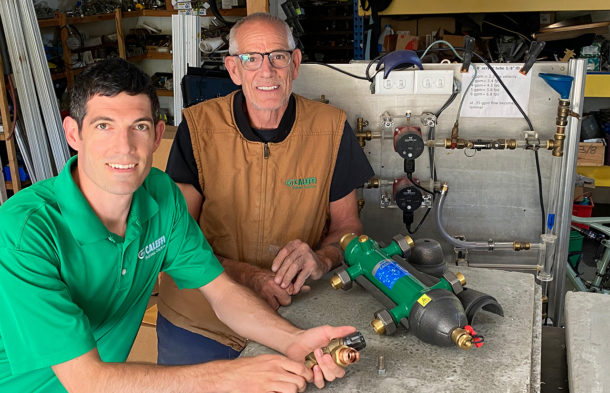
The need for having a trained workforce is critical. Equipment is becoming more sophisticated and specific, so factory training will march forward. We would love to hear from all the players in the industry, thoughts suggestions, what we can do to keep you’ all coming back.
Let’s rid the ‘VID and get back to the normal face to face that we all crave.
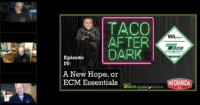
Taco’s Rick Mayo, Dave Holdorf and John Barba lead us through six weeks’ worth of hydronics essentials, capping off with a St. Patrick’s Day even blowout on Tips, Tricks and Other Essentials. This episode focuses on ECM Circulator Essentials. ECM stands for Electronically Commutated Motor. Those three little letters are transforming residential hydronics, but do Read more
Taco’s Rick Mayo, Dave Holdorf and John Barba lead us through six weeks’ worth of hydronics essentials, capping off with a St. Patrick’s Day even blowout on Tips, Tricks and Other Essentials. This episode focuses on ECM Circulator Essentials.
ECM stands for Electronically Commutated Motor. Those three little letters are transforming residential hydronics, but do we really know what we need to know about how these remarkable little devices work? Variable Speed Technology can do wonders for the modern residential hydronic system, but they’re not magic, and they don’t size themselves – no matter how many times you push that button. In this highly anticipated session, we’ll dispel the common falsehoods being fed to the industry about variable speed circulators and get right down to the truth of how they work, what they do and the value they bring to your systems.
You’ll learn the difference between Delta-T and Delta-P circulators, why each exists and what each can do for you. We’ll also show you the latest in ECM technology and the advantages of Bluetooth Connectivity.
For more information on this series visit: Taco After Dark