By Jason Richards, Hajoca Corp. I’ve seen a lot of creative ways to provide emergency heat to buildings during no-heat situations, but maybe none as original as a project we became involved with early this year at an upscale rural property near Reading, Pa. The 12,500-square-foot building, one of many on the 100-acre property, houses Read more
U.S. Boiler Company
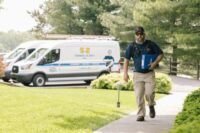
By Jason Richards, Hajoca Corp.
I’ve seen a lot of creative ways to provide emergency heat to buildings during no-heat situations, but maybe none as original as a project we became involved with early this year at an upscale rural property near Reading, Pa.
The 12,500-square-foot building, one of many on the 100-acre property, houses a heated pool, spa, full size tennis court, kitchen and locker rooms. When the old sectional boiler used to heat the facility failed mid-winter, maintenance staff turned the pool water temperature way up. This not only held the natatorium at a safe temperature, but waste heat from the pool heating equipment kept the adjacent tennis court from freezing.
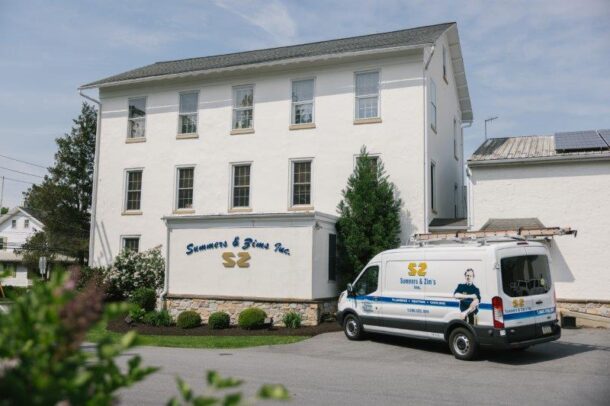
With 37 employees, Summers & Zims serves southeastern Pennsylvania from their headquarters in Atglen, Pa.
Mechanical contractor Summers & Zims, Atglen, Pa, was called in January to handle the no-heat call. The 37-person company had served the property owner in 2013 when they installed an extensive snowmelt system.
Joe Henderson, plumbing project manager, responded to the call and found that the large boiler was beyond repair; a replacement was needed immediately.
“Jason Richards, at Hajoca, and I began designing a replacement,” said Henderson. “There was a 500-gallon fuel oil tank on the property for the hydronic system and backup generator, and there was also an LP tank for the pool heater. The problem with replacing the original oil boiler with a propane unit was that the existing LP tank wasn’t large enough to handle the additional load. Plus, a second LP tank wasn’t immediately available.”
We didn’t know it then, but that was the first instance we experienced where major product availability issues would impact our decisions during the design process. Luckily, the supply chain challenges ultimately resulted in an even better system than we planned for initially.
Collaborative design
We continued the design with a multi-boiler approach. The original plan was to install a single large sectional boiler, but supply chain issues caused some trouble. I consulted with Dave Raabe, at ROI Marketing, and we learned that the boiler we wanted wouldn’t be available for a few weeks.
“This project took place at the height of the product availability challenge,” said Raabe. “The larger boilers weren’t available, so we looked at using three smaller MPO-IQ boilers, made by U.S. Boiler Company. These were immediately available. Ultimately, installing three boilers provides three stages of heat input for higher efficiency, and it also provides a level of redundancy. The smaller boilers also meant that the units could be wheeled into the mechanical on hand carts, instead of being field-assembled.
As a result, the design team selected three, 189 MBH boilers.
“We’ve come to love the MPO-IQ,” said Henderson. “We’ve installed tons of them. At 87 percent, they’re the most efficient, dependable oil boiler we’ve ever used.”
This design yielded a three-stage oil-fired system, which is uncommon in a residential/light commercial application. It provides some redundancy and, more importantly, allows the system to fire at lower input based on outdoor reset.
Controlling the boilers became the next question. Summers & Zims’ HVAC trainer and in-house tech support, Kenny Walker, has a great deal of experience with tekmar controls and had used the tekmar Boiler Control 274 for staging multiple boilers on numerous occasions. The property owner also wanted to remotely monitor the system through WiFi, so the new tekmar Smart Boiler Control 294 was selected.
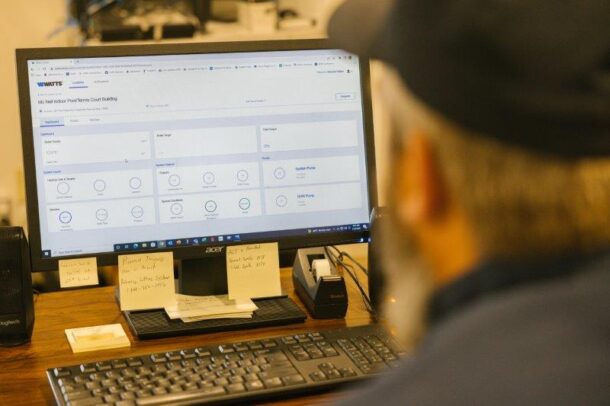
Using the Watts OnSite web or mobile applications associated with the tekmar Smart Boiler Control 294, Kenny Walker can monitor the boiler system from his desktop or mobile device.
Rapid installation
Summers & Zims, originally Summers Brothers Plumbing & Heating, has been in the business since 1930. They merged with Zim’s Sales & Service in the 70s, forming the company it is today.
I’ve known a lot of their people for a long time, and can speak to their professionalism. They’re what I’d call “do the right thing” kind of people. Joe Henderson and I go back 25 years, even before I joined Hajoca. He’s a very sharp hydronics guy. When it came time to install the system in a hurry, I knew they could handle it.
For the install, Walker was joined by Todd Lease, head plumbing technician, Andrew DiEugenio, journeyman plumber, and Austin McGhee, apprentice.
The boilers were rolled into the mechanical room and a primary-secondary piping configuration was used to connect them to the system loop. The fuel supply line to each boiler features a Tigerloop fuel oil deaerator.
“We install a Tigerloop on every oil-fired system we install,” said Walker. “They cut down on nonsense service and emergency calls by cleaning up ignition and burn, which creates less soot in the heat exchanger. We also like that they allow us to use spin-on oil filters, which catch small dirt particles and reduce nozzle failures.
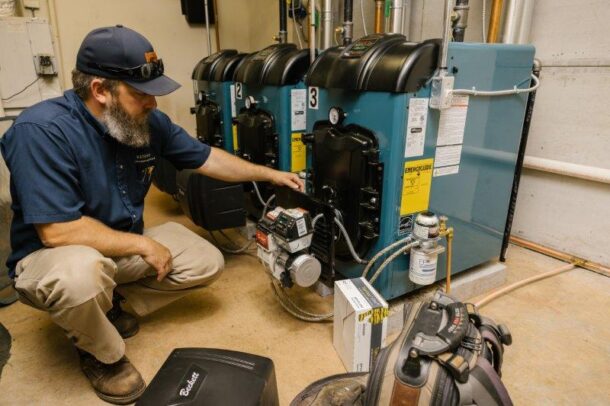
Kenny Walker, Summers & Zims HVAC trainer and in-house tech support, installs a Tigerloop Ultra oil line de-aerator.
“If the homeowner isn’t attentive to the amount of fuel they have left in the tank, running empty isn’t such a big deal,” he added. “The Tigerloop provides a two-pipe system from the oil pump to the unit. This way, the oil pump will self-prime, meaning the owner or the fuel delivery tech can simply hit the reset button on the primary control once oil has been delivered.”
Flexible fuel lines were used from the Tigerloop to the boiler’s Beckett burner. To provide easy access to the three-pass heat exchanger, the MPO-IQ features a hinged front door, where the burner is located. By using flexible lines instead of hard pipe, service techs can open the boiler without removing the fuel fitting at the burner.
“Providing deaeration is even more critical on a multi-boiler installation like this because the more times you Tee off of the fuel line, the more opportunity there is for air to enter the fuel supply,” continued Walker.
Venting the boilers was done as deliberately as supplying the fuel. The existing chimney was large enough, but common venting the three units had to be done carefully.
“We couldn’t just run three, six-inch vents into a common stack, because the distance between the boilers and the main stack were slightly different,” explained Henderson. “The first two boilers join into an eight-inch vent, which increases to 10 inches as it picks up the third boiler and exits to the chimney.”
Control
When the original boiler failed, the homeowner decided that he wanted to monitor the heating system regardless of where he was, and he also made the decision to sign a service agreement with Summers & Zims. For both of those reasons, Henderson wanted to find a control solution to stage the boilers and provide web-based monitoring. That said, they also wanted to avoid the use of a complex, costly building automation system.
“Jason had recently told us about the new tekmar 294,” said Walker. “So when we bought the boilers from Hajoca, we also bought the control. The 294 is similar to the 274, but with more features, a touch screen, and most importantly, remote monitoring capability. It can also send me texts, emails and push notifications for a wide variety of alerts.”
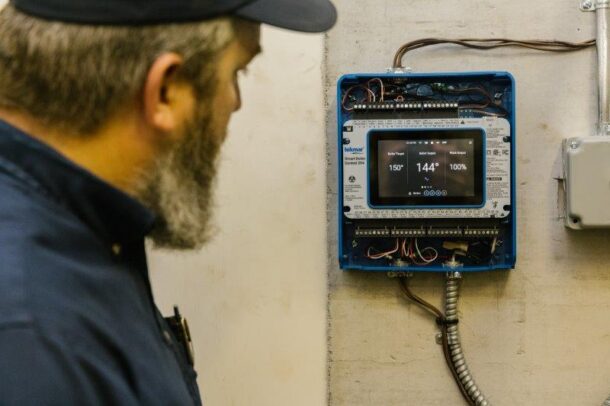
Kenny Walker installs the tekmar Smart Boiler Control 294.
The control stages and rotates the boilers, as well as handling outdoor reset, DHW priority, warm weather shutdown, etc.
In a typical MPO-IQ boiler installation, the onboard boiler control features optional plug-and-play cards to provide outdoor reset, low-water cutoff and aquastat. In this system, the tekmar 294 replaces all but the low-water cutoff card.
“The 294 was easy to install, and I can pull up and make setpoint changes to the customer’s system at my office or on my phone,” said Walker. “Right off the top of my head, we have half a dozen other systems in the field that would benefit from the use of this control. Each one can control four appliances, and they’re expandable to 16.”
Within a week of the old boiler failing, the new hydronic system was heating the building, and the pool heater was turned back down to its normal operating temperature.
I think this job—and the speed at which it came together despite supply chain issues—is a testament to Summers & Zims. The whole company shows up and honestly tries to do the very best they can.
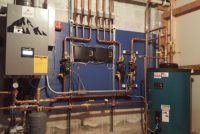
Quarryville, PA, is home to a true hydronic savant. Tom Soukup, owner of Patriot Water Heater, Co., used to do general plumbing and a variety of HVAC work. However, over the past few years, he has transitioned to a sole focus on hydronic work. “Hydronic heating—and cooling for that matter—is a truly universal form of Read more
Quarryville, PA, is home to a true hydronic savant. Tom Soukup, owner of Patriot Water Heater, Co., used to do general plumbing and a variety of HVAC work. However, over the past few years, he has transitioned to a sole focus on hydronic work.
“Hydronic heating—and cooling for that matter—is a truly universal form of space conditioning,” exclaimed Soukup. “What other medium has as much ability, and flexibility? I can heat your building, your spa, your DHW, melt snow, create process water, and just about anything else. And I can do it with nearly any fuel source you can think of.”
Soukup has done hydronic work since he got his start in the trades 25 years ago. Still, his recent move to all hydronic has been so deliberate that he even created a new brand, EcoDronics.
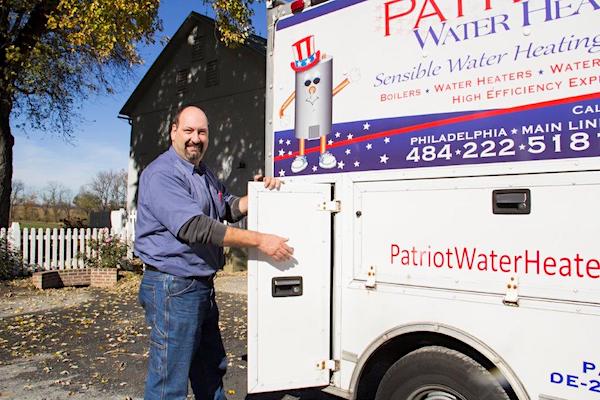
Tom Soukup, president of Patriot Water Heater, arrives to a jobsite.
“EcoDronics is our ‘unconventional’ hydronic brand,” he explained. “Think greenhouses, swimming pools, and snowmelt. It’s different than general home comfort, so the new brand reflects that.”
The move into unique water-based heating applications doesn’t mean that the company turns down typical boiler projects. Last month, a nearby homeowner asked Soukup to give a second opinion on a dying mechanical system.
Patriot Water Heater’s answer was the same as the first company that visited the home: a complete system replacement of the LP-fired boiler system was needed. The difference is how Soukup came to the conclusion, and the results he could deliver throughout the home, not just the boiler room.
“I make a point to spend a good deal of time asking what the customer wants in regard to the system as whole,” he said. “Noise, comfort, control… and whether or not there areas of the house that go unused? I need to know what the homeowner really wants so my team can deliver it.”
Murphy’s Law
This customer’s system was 25 years old, and it’s a wonder it lasted that long. Anything that could have been installed wrong, had been.
“There was no primary/secondary piping, no air elimination, no feed valve and the pump was on the return side of the boiler,” said Soukup. “The water returning to the cast iron boiler was too cool and the heat exchanger was condensing. The combustion chamber had collapsed, sections were leaking, the flue pipe was rotten, oil use cost over $3,000 per year, and the home was horribly uncomfortable. Long piping runs and high head pressures created by strange piping were causing both condensation and comfort issues.”
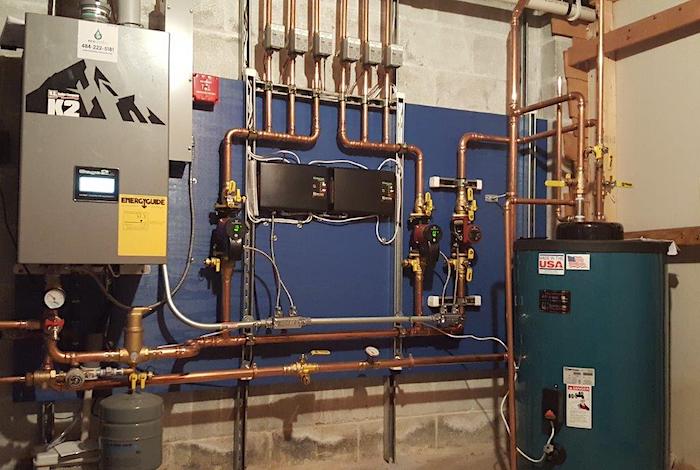
Soukup appreciates that U.S. Boiler Company provides a full hydronic solution: K2 boiler, Sage Zone Controls and the Alliance sidearm tank. A boiler with a 10-1 turndown ratio is complemented nicely by variable-speed pumps, making the system very responsive to the needs of the home.
The house was zoned horizontally, right down the center, instead of being zoned upstairs and downstairs. The upstairs was sweltering hot while downstairs occupants froze. The parents ran an electric space heater in their downstairs bedroom so that the kids, upstairs, wouldn’t sweat all night.
When the first contractor visited the home, they condemned the boiler but had no interest in addressing the comfort issues, or how the fin-tube radiation had been piped.
“My apprentice and I spent 16 hours analyzing and diagnosing issues before we gave a bid,” said Soukup. “First we performed a Manual J and an EDR. It became apparent that scrapping the boiler and rebuilding the mechanical room was the easy part. Rezoning the house was another story.”
Rubber meets road
Over the course of four days, Patriot Water Heater completely revolutionized the heating system. Aside from the baseboard and some copper pipe, everything was replaced.
“As is usually the case when you think things through before grabbing a pipe cutter, the install was relatively straightforward,” said Soukup
He and his apprentice, Ben Dyson, installed a K2 condensing boiler made by U.S. Boiler Company. The unit features a 10-1 turndown and provides 95% AFUE. They also used two U.S. Boiler Sage Zone Controls, which are expandable to 16 zones.
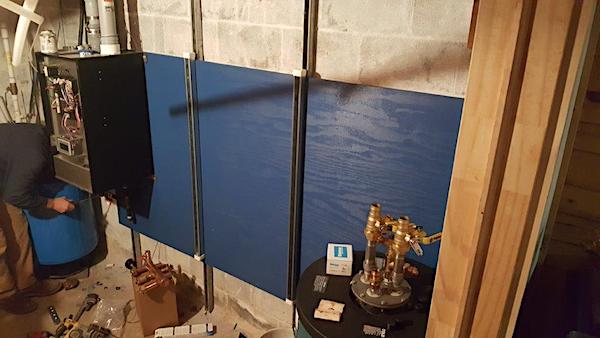
Patriot sets the big items first: K2 boiler and Alliance SL indirect tank.
“U.S. Boiler hit a home run with the K2 boiler,” said Soukup. “It’s a ton of functionality in a small box, and the controls are lightyears ahead of the competition. For example, the Sage Zone Control communicates directly with the boiler. I think being able to provide an integrated solution is important.”
Soukup and Dyson, who is a Marine reservist, broke the existing supply and return piping into six zones. A seventh was added for domestic hot water. A 35-gallon U.S. Boiler Alliance SL tank was used for nearly limitless hot water, long service, and the fact that the tank features top connections. The existing electric water heater was removed.
Fine-tuned success
“I visited the home on the morning after I fired the boiler, and the customer mentioned how nice it was to have even heat throughout the house,” said Soukup. “At the time, the outdoor temperature was 31°F and the boiler was running at 20% input. Nonetheless, there was still a little room for improvement.”
Through the K2 boiler’s touchscreen display, Soukup accessed the zone-by-zone runtime data and noticed that the living room was calling for heat too often. So, he lowered the anticipated BTUs slightly on the Sage Zone Control, and set the programmable thermostat’s temperature differential from one to two degrees. That solved the issue, and comfort levels haven’t changed.
“That’s what I love about the Sage Controls,” said Soukup. “Once I program the control, I can get really granular by looking at individual parts of the system. It allows me to fine-tune the system. Plus, if you’re going to install a modulating boiler, isn’t that the ultimate goal?”
On commercial projects specifically, Soukup has begun installing a meter on the gas valves of the systems we will be retrofitting, sometimes a year in advance. It’s a fantastic way to compare the energy use before and after a retrofit, and he can use those concrete numbers to sell the next project.
“For residential jobs like this—which don’t typically provide us with enough data collection time on the front end—we use the owner’s records,” explained Soukup.
On this job, the owners knew they’d used 2,200 gallons of fuel oil (308,000 MBH) the previous year. The year following the retrofit required 800 gallons of LP gas (73,600 MBH). Those number don’t include DHW production, either, as DHW had previously been supplied by electric, and are now provided by the boiler via the sidearm tank. And an electric space heater is no longer used in the master bedroom.
That’s a staggering improvement, but at the end of a cold winter day, it is pretty hard to quantify comfort.
Lancaster, Pa.-based U.S. Boiler Company recently launched its new online training program, called U.S.B-U (U.S. Boiler University). U.S.B-U was developed to provide an archive of readily accessible information to help heating professionals perform service and installations quickly, and with a high degree of confidence. This new training platform delivers educational content in video and blog Read more
Lancaster, Pa.-based U.S. Boiler Company recently launched its new online training program, called U.S.B-U (U.S. Boiler University).
U.S.B-U was developed to provide an archive of readily accessible information to help heating professionals perform service and installations quickly, and with a high degree of confidence. This new training platform delivers educational content in video and blog format. Live online training seminars are also offered.
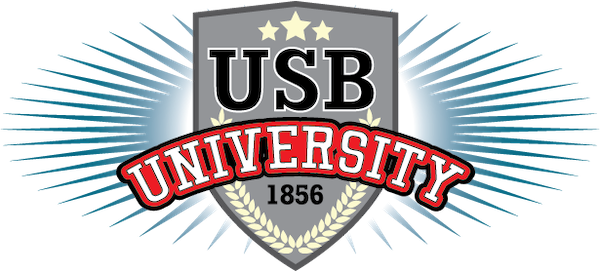
The training material is developed U.S. Boiler Company’s technical sales and support staff. The first course, Installing High Efficiency Boilers, was released April 6, 2020, followed by sessions for venting high efficiency boilers and primary/secondary piping.
By breaking the training material into 10 to 15-minute online modules, U.S.B-U provides the content in a digestible, convenient format. Anyone who installs and services boilers will find the information highly informative, regardless of the boiler brand they install.
U.S.B-U was created to provide more training opportunities to professionals in a rapidly changing industry, and as a valuable resource for the coming heating season, when HVAC professionals may be in higher demand than ever before. U.S. Boiler Company feels that the relatively mild 2019-2020 winter, coupled with the current global pandemic, will create a “perfect storm” of installations and service calls in 2020-2021. Contractors who are able to quickly and efficiently perform these services will be well positioned to meet the need.
To learn more or receive updates on U.S. Boiler Company’s training offerings, visit https://www.usboiler.net/u-s-boiler-university.html