Bradford White Corporation subsidiary recognizes the experienced executive’s contributions to the company and industry with promotion to senior VP and general manager post Bradford White Corporation, an industry-leading manufacturer of commercial, residential and industrial water heating and storage applications, has named Rich Simons senior vice president and general manager of Laars® Heating Systems Company. “I’ve Read more
water heating
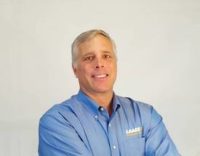
Bradford White Corporation subsidiary recognizes the experienced executive’s contributions to the company and industry with promotion to senior VP and general manager post
Bradford White Corporation, an industry-leading manufacturer of commercial, residential and industrial water heating and storage applications, has named Rich Simons senior vice president and general manager of Laars® Heating Systems Company.
“I’ve often said that Rich is the epitome of a general manager, because he can bring insight and ideas to every facet of the Laars Heating System’s business,” said Bruce Carnevale, president and CEO of Bradford White Corporation. “His broad knowledge base, tireless work ethic and industry experience have made him an invaluable part of our corporate leadership team.”
Simons, a graduate of Case Western Reserve University and the University of Minnesota Carlson School of Business, joined Laars in 2016 as vice president and general manager. His responsibilities encompass the overall operation of the business as well as its strategic direction and financial results. Simons has more than 30 years of experience in the boiler industry.
“The opportunities that we are taking to deliver innovative customer solutions have never been better and we are excited about our future,” Simons said. “It’s about our customers and our people, and as a member of the Bradford White family, I am very proud of what we have accomplished. I believe we embody a customer commitment that is second to none as one of the industry’s premier boiler manufacturers.”
In January, Simons was appointed to the board of directors of the American Boiler Manufacturers Association.
“When Rich arrived at Laars, his priority was to spend time with our customers and manufacturers’ representatives so he could truly understand their needs and learn about any challenges they were experiencing,” Carnevale said. “Under his leadership, the Laars team has brought new products to market in record time and implemented improvements across the major functional areas of the company.”

Navien, Inc. announced three new innovations during their boiler virtual launch event on February 16. The three new products include the NCB-H condensing combi-boiler, NFC-H condensing fire tube combi-boiler and NFB-H condensing fire tube boiler. Navien’s new NCB-H condensing combi-boiler series includes 5 models ranging from 160,000 BTU/H for DHW and 60,000 BTU/H for heating Read more
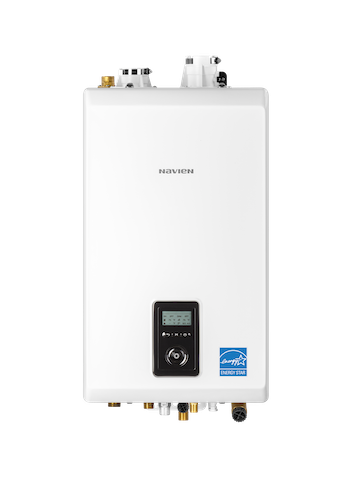
NCB-H Condensing Combi Boiler
Navien, Inc. announced three new innovations during their boiler virtual launch event on February 16. The three new products include the NCB-H condensing combi-boiler, NFC-H condensing fire tube combi-boiler and NFB-H condensing fire tube boiler.
Navien’s new NCB-H condensing combi-boiler series includes 5 models ranging from 160,000 BTU/H for DHW and 60,000 BTU/H for heating, to an industry first 210,000 BTU/H DHW and 150,000 BTU/H heating. The NCB-H uses durable dual stainless steel heat exchangers for heating and a separate flat plate stainless steel heat exchanger for DHW.
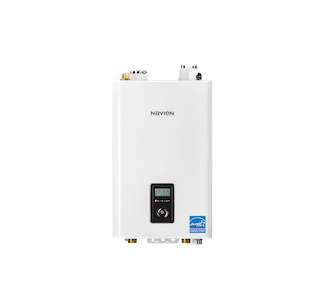
NFB-H Fire Tube Condensing Boiler
Advanced features on the NCB-H include 15:1 TDR for DHW and up to 11:1 TDR for heating, advanced controls with intuitive display, built-in advanced DHW recirculation controls, 2” venting up to 65’ and 3” venting up to 150’, common venting capability with up to 7 NPE tankless water heaters, cascade capability with up to 15 NPE tankless water heaters, field gas convertibility to NG high altitude (5,400 ft. to 10,100 ft.) or LP (up to 10,000 ft.) and a new DHW module with mixing valve and flow adjustment valve.
NCB-H is available to ship from Navien immediately.
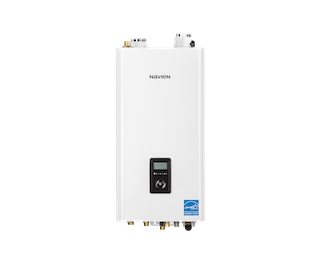
NFC-H Fire Tube Condensing Boiler
Navien also revealed updates to their fire tube lines with the NFC-H fire tube combi-boilers and NFB-H fire tube boilers. Both the NFC-H and NFB-H now offer turndown ratios up to 15:1, powered connections for 3 zone pumps or 3 zone valves, easy to use Setup Wizard for improved installation, 2” venting up to 65’ and 3” venting up to 150’. The NFC-H also includes increased DHW performance with up to 210,000 BTU/H for DHW, offering up to 5.4 GPM at a 70-degree temperature rise. Both the NFC-H and NFB-H will begin shipping from Navien in April 2021.
Navien will host another virtual launch event focused on water heaters on March 16, 2021. Registration is still open for the event at navieninc.com/live. For more information on all products shown during Navien’s boiler virtual launch event, visit navieninc.com.
Irvine, CA – Navien has added to their website, NavienInc.com, the ability to view the website in Spanish. In an effort to make more information available to Spanish speaking visitors, Navien has gone through a grand project of translating the entire NavienInc.com website along with brochures, manuals, guides and more. Visitors can now search for installers in Read more
Irvine, CA – Navien has added to their website, NavienInc.com, the ability to view the website in Spanish. In an effort to make more information available to Spanish speaking visitors, Navien has gone through a grand project of translating the entire NavienInc.com website along with brochures, manuals, guides and more. Visitors can now search for installers in their area, register a Navien product, learn about Navien tankless water heaters, combi-boilers or boilers and much more on the website in either English or Spanish. To access the Navien website in Spanish, click on language within the main navigation at the top of the website and select, or directly visit the website in Spanish by going to NavienInc.com/es.
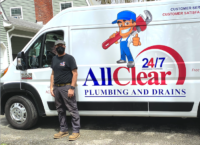
Turning wrenches since he was 17 years old, George DeJesus (@georgetheplumber) considers himself relatively lucky during these crazy times were going through, as the service calls are still trickling in, with some days bit slower than usual. During the current state of the trades during the pandemic, DeJesus says it’s hard going into customer’s homes Read more
Turning wrenches since he was 17 years old, George DeJesus (@georgetheplumber) considers himself relatively lucky during these crazy times were going through, as the service calls are still trickling in, with some days bit slower than usual. During the current state of the trades during the pandemic, DeJesus says it’s hard going into customer’s homes right now, but he is taking the necessary precautions to take to keep himself as safe as he can. Pandemic or not, “I’ve learned to never get too comfortable that the jobs are going to come in,” says DeJesus. “You have to give great customer service so you get called the next time.”
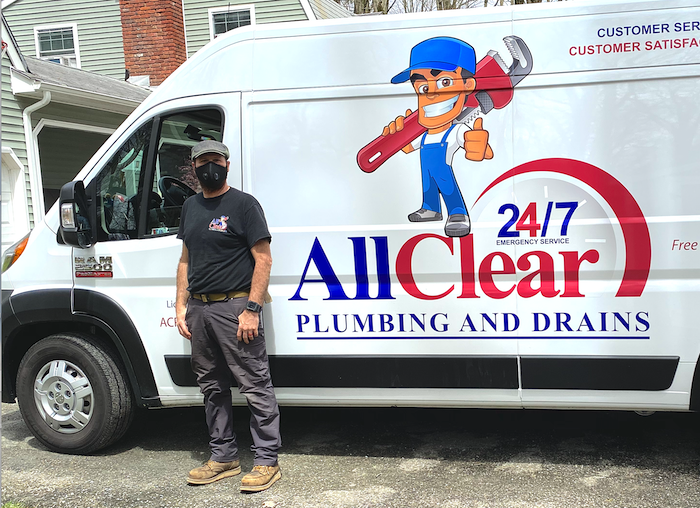
DeJesus transferred to a trade school during his junior year of high school and got his first plumbing job at 17, and he hasn’t looked back. “High school just wasn’t for me. Finding this trade was my savior; I could have gone down a very bad road but I got a job, learned this trade and found I could be good at something. From there, it was easy to apply myself. I continue to learn every day, and teach when I can,” says DeJesus.
Having worked with various companies throughout the years has helped DeJesus become very well-rounded, learning more skills with each experience. For the past two years, DeJesus has worked for All Clear Plumbing and Drains, Succasunna, N.J., where he specializes in boiler and drain cleaning residential work, finding gratification in troubleshooting the most difficult service work jobs. “I love being a plumber. It’s hard work but when you have a difficult job and figure it out, it leaves you with great satisfaction,” says DeJesus.
DeJesus considers himself very fortunate to have had many mentors over the years, but perhaps none more influential than his father, a very hard working and dedicated general contractor. “There are new skills to be learned and I try to learn as much as I can about each position I take. The friends that I have met through the years are great guys and I love learning and sharing skills I know with them.”
What advice would DeJesus give to someone thinking about entering the trades? “It’s hard work but a good living. Don’t be lazy. If I’m showing you how to do something, pay attention and get involved. Keep your phone in your pocket. Measure twice and cut once,” says DeJesus.
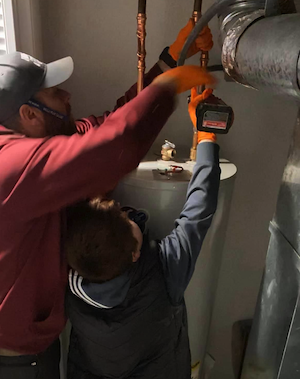
One outlet DeJesus has found most satisfying and beneficial is social media. “I have definitely found social media to increase my friendships and knowledge,” says DeJesus. “It’s amazing that no matter how much you think you know, you can still learn more. I talk to most of my Instagram friends more than the friends I have locally. They can relate to what struggles come with the job and can celebrate the triumphs. I’m so thankful to have been able to make friends with so many great people.”
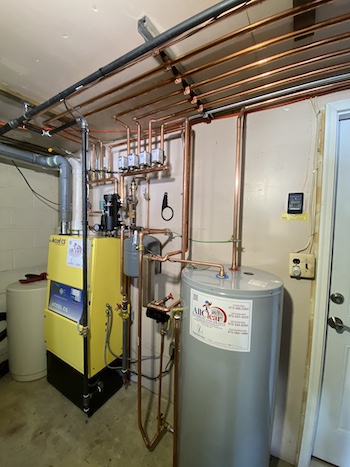
A proud install: oil-to-gas conversion; boiler was moved from one side of the house to the other to gain space. Added a zone of heat in the addition with a stat.
Yet one of DeJesus’ biggest struggles is balancing work and family time. In his “spare time,” DeJesus likes going to the movies with his wife and family, and he enjoys taking day trips and weekend trips. “I tend to put too much into my work. Even on my days off or when I get home, I tend to be catching up with IG and social media,” says DeJesus. “Lately, I’ve been trying to teach my kids some of the trade, and I do listen to my wife when she tries to focus me back to family time. Well, most of the time.”
In the end, DeJesus is a craftsman and he is proud of the work he does, and it shows. In fact, when asked when the last time he said, “Man, today is a great day!” he responded that it happened last week with his last boiler install. “I stepped back and felt that it was probably one of my best and favorite installs.”
With hard work and his willingness to get better, the trades have been good to DeJesus. You get what you put into it. “Not many people can say they make six figures and don’t even have a high school degree … well, at least working legally!” says DeJesus.
Lancaster, Pa.-based U.S. Boiler Company recently launched its new online training program, called U.S.B-U (U.S. Boiler University). U.S.B-U was developed to provide an archive of readily accessible information to help heating professionals perform service and installations quickly, and with a high degree of confidence. This new training platform delivers educational content in video and blog Read more
Lancaster, Pa.-based U.S. Boiler Company recently launched its new online training program, called U.S.B-U (U.S. Boiler University).
U.S.B-U was developed to provide an archive of readily accessible information to help heating professionals perform service and installations quickly, and with a high degree of confidence. This new training platform delivers educational content in video and blog format. Live online training seminars are also offered.
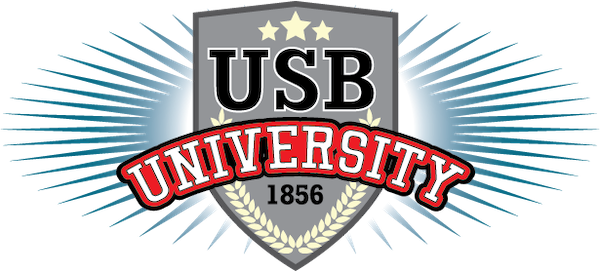
The training material is developed U.S. Boiler Company’s technical sales and support staff. The first course, Installing High Efficiency Boilers, was released April 6, 2020, followed by sessions for venting high efficiency boilers and primary/secondary piping.
By breaking the training material into 10 to 15-minute online modules, U.S.B-U provides the content in a digestible, convenient format. Anyone who installs and services boilers will find the information highly informative, regardless of the boiler brand they install.
U.S.B-U was created to provide more training opportunities to professionals in a rapidly changing industry, and as a valuable resource for the coming heating season, when HVAC professionals may be in higher demand than ever before. U.S. Boiler Company feels that the relatively mild 2019-2020 winter, coupled with the current global pandemic, will create a “perfect storm” of installations and service calls in 2020-2021. Contractors who are able to quickly and efficiently perform these services will be well positioned to meet the need.
To learn more or receive updates on U.S. Boiler Company’s training offerings, visit https://www.usboiler.net/u-s-boiler-university.html