… what is the level of scale in your water? Hard to say, I’d imagine. But, over time, believe me, you’ll know. Scale, also known as limescale, refers to mineral buildup—primarily magnesium and calcium—that creates a white, chalky-like substance that can accumulate on the plumbing system’s internal components, including water heaters, pipes, and fixtures, says Read more
Featured Articles
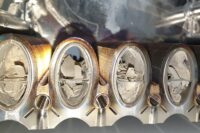
… what is the level of scale in your water? Hard to say, I’d imagine. But, over time, believe me, you’ll know. Scale, also known as limescale, refers to mineral buildup—primarily magnesium and calcium—that creates a white, chalky-like substance that can accumulate on the plumbing system’s internal components, including water heaters, pipes, and fixtures, says Randall Oshiro, Lead Engineer, Noritz America.
In other words, “Common in household water, especially in areas with hard water, scale is essentially the crusty stuff you sometimes see on old pipes or the heating element of an old kettle,” says Ben Tate, National Sales Manager—Water Treatment, Navien, Inc. “When water is heated, these minerals crystallize and stick to surfaces such as the interiors of pipes, boilers, and heaters, forming a hard, insulating layer. It’s a natural process, but not exactly a welcome one, as it hampers the efficiency of any appliance it settles in.”
Scale’s Geography
Scale’s prevalence comes down to the geological makeup of the land through which your water travels. Water is a universal solvent, and as it moves through soil and rock, it picks up minerals like calcium and magnesium. In areas rich in limestone and other calcareous rocks, which are composed mainly of calcium carbonate, water tends to carry a higher load of these minerals. Consequently, regions with such geological features—think of areas like Texas and Florida—often struggle more with hard water and, by extension, scale.
Calcium and magnesium are naturally occurring minerals, says Oshiro. Depending on where the water is drawn from, water flowing through ground sources that contain high concentrations of these minerals will absorb some of the minerals. For example, water drawn from an aquifer with a high concentration of limestone will inevitably have a high concentration of lime (calcium). Like the previous example, areas where water is drawn from underground are often where the highest concentration of hard water exists.
A Water Heater’s Nemesis
Yet the “damage” scale can bring can’t be overstated, says Dan Giosia, Assistant Product Manager, Bradford White Corporation, “The accumulation of scale in a water heating system diminishes the overall performance, efficiency, and lifespan of the water heater unless preventative maintenance measures are implemented.”
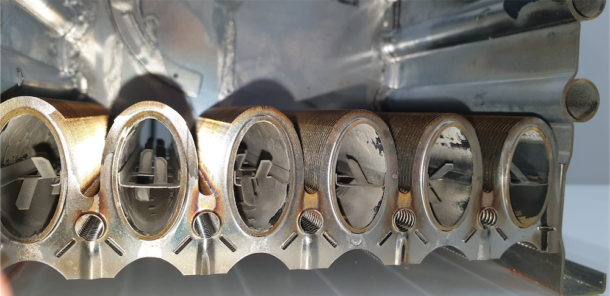
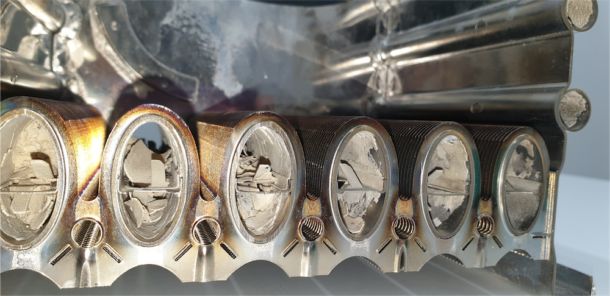
Scale poses a triple threat to water heating systems, says Tate. First, it’s an insulator. In a domain where efficient heat transfer is key, scale is a formidable barrier that keeps heat from doing its job effectively, which can drive up energy costs as your system struggles to keep up. Second, scale buildup increases the pressure in water lines and heating chambers, which can lead to leaks or mechanical failures. Lastly, the more energy and repairs a system requires, the more its lifespan diminishes. That’s why preventing scale isn’t just about maintaining water flow; it’s about saving money and extending the life of your equipment.
According to Oshiro, the primary danger of this scale formation is that it can accumulate inside the water heater (on the heat exchanger of tankless water heaters, along electrical heating elements, or along the internal flue of gas storage water heaters). This scale formation acts as an insulator in large amounts, preventing the proper heat exchange between the water and the heating source. “When this happens, the temperature will increase—as heat is not being drawn away at the designed rate—leading to increased thermal stress and decreased longevity of the internal components. Additionally, this buildup can reduce the surface area of piping, which can reduce the flow performance of the fixtures as well,” says Oshiro.
Tankless Magnified
Scale impacts both tank-type and tankless water heaters, though it manifests differently in each system, says Tate. In tank-type heaters, scale settles at the bottom of the tank, reducing heat transfer efficiency and leading to increased energy consumption and potential corrosion. Over time, this can significantly shorten the lifespan of the heater. Conversely, tankless models, which heat water directly, experience scale buildup directly on their heat exchangers. This can decrease heating efficiency and disrupt water flow, though it does not necessarily indicate a greater susceptibility to scale than tank-type heaters.
Regardless of the system type, the key to mitigating scale effects lies in regular maintenance. Both tank-type and tankless water heaters benefit from routine descaling and the proactive use of water treatment solutions like water softeners or scale inhibitors. Properly maintained, both systems can handle scale effectively, ensuring efficient operation and extending the lifespan of the heater. Thus, neither system is disadvantaged by scale when properly cared for, allowing users to choose based on their specific needs and preferences.
The reality is the mechanism/issue is about the same for both types of technology. “However, it will present itself much sooner/more apparently with a tankless type water heater than a tank-type water heater. The reason for this is basically that the pipes are smaller. Imagine a ¾” pipe and 24” round storage vessel. The smaller pipe, with a ¼” of scale buildup, loses significantly more of its surface area in comparison. This means that issues like reduced flow will become more apparent sooner,” says Oshiro.
However, it should be noted, continues Oshiro, that this same amount of scale will have the same actual effect on the systems (reduced efficiency, higher thermal stress). As a result, a tankless water heater may show signs of decreased performance sooner; however, this also allows the customer to preemptively conduct maintenance to ensure that the product will last many times longer than a storage tank-type water heater.
The storage tank-type water heater often continues to build up this scale over time, resulting in lower efficiencies (meaning higher operating costs) and eventual failure sooner. This scale formation is one of the primary mechanisms by which water heaters will fail. 1
According to Bradford White’s Giosia, scale does pose a greater issue for tankless water heaters compared to tank-type water heaters due to their compact heat exchanger design. With a limited surface area and brief heating period, tankless heaters must rapidly elevate water temperatures, requiring high temperatures within the heat exchanger. As a result, scale tends to accumulate on this surface. If scale buildup becomes excessive, it can restrict water flow through the heat exchanger to the point of causing component or unit failure so it’s important for homeowners to contact their plumbing professional for regular maintenance.
In comparison to gas tank-type water heaters, electric tank-type heaters are generally more susceptible to scale buildup. This is primarily due to the very hot surfaces of electric heating elements, which have a small area and are prone to accumulating limescale within the tank. However, the impact of scale buildup is limited by the fact that electric heating elements are relatively inexpensive to replace, especially when compared to the cost of replacing a tankless gas heat exchanger or complete unit.
Gas tank-type water heaters may vary in susceptibility to scale buildup depending on their design. Units with a burner located outside the tank are typically less affected by scale compared to those with an internal heat exchanger where scale can accumulate.
Action Plan
What can contractors/homeowners do to “combat” scale? “The first step is to know your water supply,” says Oshiro. “Almost every municipal water supply company will annually publish a water quality report that will include data about the hardness of your water supply. This rating will often be rated on a scale of grains per gallon (gpg), parts per million (ppm), or milligrams per liter (mg/L). These ratings tell the density of mineral hardness (calcium) present in the water supply. The USGS[1] has a relative hardness indicator, where 61-120 mg/L (3.6-6 gpg) would be considered somewhat hard water.”
The best way to reduce scale is to treat the cause. This means using water treatment devices to prevent the calcium from building up in your water heater and piping. However, this isn’t always possible, so maintenance can be conducted by a descale flush: running a deliming agent (ex., vinegar or a specialized deliming agent) solution through piping the water heater to neutralize the calcium. As calcium is a basic material (pH >7), the acidic deliming agent will neutralize the calcium and remove buildup.
It’s also essential to adhere to the manufacturer’s recommendations for preventative maintenance, including specific procedures and frequency, for their product, advises Giosia.
Regular descaling of the water heater is often recommended to minimize scale buildup on the heat exchanger of a tankless water heater. The frequency of preventative maintenance typically depends on the characteristics of the water supply in your area, such as whether it is heating hard or soft water.
Installing a water softener can help reduce the hardness of the incoming water into both tankless and tank-type water heaters. However, it’s important to consult with a plumbing professional to ensure compatibility and to follow their recommendations.
Navien’s Tate says contractors and homeowners in these regions should adopt a proactive approach to water treatment. Installing a water softener is one effective strategy; it replaces hardness ions like calcium and magnesium with sodium or potassium, preventing them from forming scale. Additionally, I’d recommend considering scale prevention systems, which are designed to transform hardness minerals into harmless crystals that won’t stick to surfaces. Regular maintenance checks are also vital—they help ensure that any potential scale buildup is managed before it becomes a serious issue.
If you know that your water source is hard water, Oshiro suggests that you can take action to alleviate the risks.
- Develop a routine maintenance plan: This can be done by “descaling,” or flushing, your water heater regularly, depending on usage and quality. Asking your water heater manufacturer or installer for recommendations on frequency is a great first step.
- Treat the water: There are ways to eliminate (sequester or remove) hard-water minerals from the water source. These include items like water softeners, which use an ion-exchange process to physically remove free calcium from the water, or products that use a polyphosphate media to sequester the calcium to prevent it from coming out of the solution when heated.
Technology Tips
Is there newer technology that could make the equipment more scale-resistant? “Indeed,” says Tate. “One of the latest advancements in this area is Template Assisted Crystallization (TAC), which is a highly effective technology for preventing scale without the use of chemicals or salt. TAC systems work by transforming the calcium and magnesium minerals in hard water into stable, harmless crystal particles. These particles then flow through the system without sticking to surfaces, effectively preventing scale buildup. This technology is particularly useful for protecting high-efficiency tankless water heaters from scale, ensuring they operate at optimal efficiency while extending their lifespan.”
To some degree, says Oshiro, the selection of materials, design of the heat transfer surface, and the temperature in which the system operates, all have roles to play in controlling the amount of scale formation.
- Materials with less surface roughness provide less chance for scale particles to attach.
- Systems with lower temperature rises can also slightly reduce the formation rate of scale.
There is constant research into reducing the harmful effects of scale formation in water heating products, but at its core, it is a challenging situation to avoid entirely.
According to Giosia, some tankless water heater models incorporate technology aimed at enhancing scale resistance, such as scale reduction technology and replacement filtration cartridges. Moreover, water softeners can serve a similar purpose in mitigating scale buildup.
However, despite these advancements, maintenance remains essential for all tankless water heaters to prevent excessive scale accumulation. Regular upkeep is necessary to ensure optimal performance and longevity of the unit.
In conclusion, the timeline for significant damage can vary widely depending on the water’s hardness and the frequency of system maintenance. In regions with very hard water and minimal preventive measures, says Tate, significant scale buildup can occur within just a few months, leading to efficiency losses and potential system failures. Conversely, with proper management and regular maintenance, scale-related damage can often be staved off for years, preserving the efficiency and extending the life of the system.
1
https://www.usgs.gov/special-topics/water-science-school/science/hardness-water#:~:text=Measures%20of%20water%20hardness&text=General%20guidelines%20for%20classification%20of,mg%2FL%20as%20very%20hard
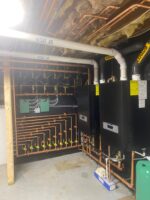
By Thomas Renner Any couple will tell you an enduring relationship depends on effective communication. So, too, do some home heating systems. Jeff Potvin came across this scenario in a project at a six-bedroom, 6-bath house in Andover, Mass. Potvin, the owner of Jeff Potvin Plumbing & Heating in Methuen, replaced two 150k BTU boilers Read more
By Thomas Renner
Any couple will tell you an enduring relationship depends on effective communication. So, too, do some home heating systems.
Jeff Potvin came across this scenario in a project at a six-bedroom, 6-bath house in Andover, Mass. Potvin, the owner of Jeff Potvin Plumbing & Heating in Methuen, replaced two 150k BTU boilers and a 75-gallon natural gas water heater. He chose two HTP Elite Ultra high efficiency condensing boilers as the alternative.
“The two new boilers will communicate with each other and increase efficiency, which will save the homeowner on his heating bill,’’ Potvin said.
No Ordinary Home
The residence where Potvin installed the boilers is no ordinary home. Built in 1954, the home is located in one of the state’s most historic towns just 20 miles north of Boston. The structure sits on 1.4 acres and extends across more than 7,800 square feet, including a sunroom, multiple fireplaces and is a mile away from Phillips Academy, a prestigious private high school. The school’s graduates include 2 former Presidents, George H.W. Bush and George W. Bush, Humphrey Bogart, Jack Lemmon and Bill Belichick, among others.
The challenge Potvin faced in the project was establishing communication between an outdoor sensor and the aquastat that were on air handlers to help reach the correct temperature. Aquastats are used in hydronic systems and adjust the temperature of the water in the boiler based on the outdoor temperature.
“We needed to move a few dip switches on the board to get it to work properly,’’ Potvin said.

The setup will increase efficiency and save the homeowner money on monthly heating bills. It will also heat domestic hot water and keep the home at a better temperature.
Project scope
The units provide hot water and heat for the home. Potvin said it is unusual, however, to replace three heating elements and get the same firepower with just two.
“It is unusual to change a water heater to a storage tank,’’ he said. “We completed the job during the summer, so no heat was needed.”
But the homeowner should realize some important benefits, according to Potvin.
“The two new boilers communicate with each other and increase efficiency,’’ Potvin said. “That will save the homeowner with the heating bill. The boilers have a larger BTU and will heat up faster and more efficiently. It will heat domestic hot water and keep the home at a better temperature.”
An Elite Solution
Potvin chose the HTP Elite Ultra boilers for other projects and knew it would be a good fit for this application.
The calling card for the Elite Ultra is a proprietary heat exchanger. The XtraTech Durable Stainless Steel Heating Technology exchanger ensures maximum quality at the heart of the boiler and resists corrosion to guarantee reliability for years.
The design provides increase in water flow, which creates more internal turbulence, scrubs the internal walls and reduces heat exchanger deposits to ensure a longer life span for the boiler.
Deposit buildup is a major problem in boiler operation. Scale and sludge deposits in boilers impede heat transfer, which leads to higher energy costs and can cause a loss of equipment operation and premature failure.
Boiler deposits can include calcium, magnesium, iron, copper, aluminum and others. Water treatment options can help reduce scale buildup, but those annual expenses can reach between $1,000-$2,000. Annual maintenance on the boiler will also help, but service calls can also reach more than $600.
The pipe surface on the Elite Ultra is up to 150 percent larger than conventional designs and ensures extremely low pressure water pressure drop. “The heat exchanger guards against corrosion and guarantees a long lifetime for the boiler with less maintenance,’’ Potvin said.
The boiler has a 10:1 turndown ratio that limits short cycling and provides more efficient energy consumption. The boilers rated thermal efficiency is among the highest in the industry at 96%. Adding the outdoor sensor provides the opportunity to increase that efficiency by reducing the delivered water temperatures to match the load based on outdoor temperature. This feature allows homeowners to save even more money on their monthly energy bills.

Two HTP Elite Ultra high efficiency boilers were installed in a Massachusetts home by Jeff Potvin Plumbing & Heating. The boilers replaced two 150K BTU boilers and a 75-gallon natural gas water heater.
Additional Advantages
The boiler also offers whisper-quite operation and an HTP Link that lets the homeowner control boiler operation from anywhere. With the link, homeowners can view boiler parameters and status, receive boiler text and e-mail updates, and access the unit and troubleshoot issues without having to be onsite, as long as the unit is connected to Wi-Fi and registered.
“We have used these HTP products in the past found it to be a great product,’’ Potvin said. “We also found tech support to be very good.”
Home and hot water heating can be especially challenging in Massachusetts, where temperatures fluctuate wildly from season to season, and sometimes daily during transitional periods. Having an efficient system on a large residence will generate considerable savings for the homeowner.
“Projects such as this can be challenging to find the proper solution,’’ Potvin said. “We think the homeowner will be quite satisfied with this product for years to come.”
Thomas Renner writes on building, construction, engineering and other trade industry topics for publications throughout the United States and Canada.
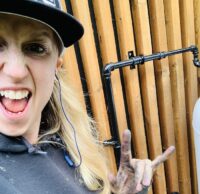
Located in rural British Columbia, Lesley McGlenen has a much greater impact on the skilled trades than her small company would lead you to believe. Online, McGlenen goes by @ThePipeWench. She’s a plumber, gasfitter and hydronic professional. Most of her work is residential, but she dabbles in commercial work from time to time. From her Read more
Located in rural British Columbia, Lesley McGlenen has a much greater impact on the skilled trades than her small company would lead you to believe.
Online, McGlenen goes by @ThePipeWench. She’s a plumber, gasfitter and hydronic professional. Most of her work is residential, but she dabbles in commercial work from time to time. From her shop in Scotch Creek, she travels to jobsites around Shuswap Lake, typically venturing up to two hours from home.
McGlenen’s father was a general contractor when she was young. She’d lend a hand where she could, cleaning up and helping on jobsites. Eventually, a plumbing contractor noticed her work ethic and offered her a job. She enjoyed the job for a while before trying her hand at cabinet making, all the while picking up skills that would aid her journey in the trades.
Eventually, plumbing called her back and she endeavored to finish her plumbing apprenticeship. Today, 17 years later, she’s sole proprietress of Pipe Wench Plumbing, Ltd.
“I love this trade, and the variety it provides,” said McGlenen. “I’d get bored if I did the same thing day in and day out. The diversity of work creates a few challenges, but they’re not overwhelming. Different people, places and the occasional challenge keep me on my toes.”
She loves the job so much that she felt a calling to help other women become part of the skilled trade workforce.
A heart for women in the trade
“I want to impact and empower women to see the trades as a viable career,” said McGlenen. “There’s no proper direction in school. School systems aren’t asking young women what they really want to do. Even if they did, few would say they want to be plumbers, pipefitters or HVAC techs because the awareness isn’t there.”
McGlenen’s father didn’t push his own kids—two daughters and a son—toward the skilled trades because from personal experience how it can be hard on the body.
“Because the school system doesn’t present the trades as a high value career path, young men and women alike are left to find their own way. The big difference is that the skilled trades are more intimidating for potential female apprentices.”
“I hear comments from time to time that young women are afraid of sexual harassment on a jobsite full of men,” said McGlenen. “I’ll admit, I’ve encountered some of that, but it’s always been a ‘bad apple’ scenario. The vast majority of men I encounter at work are very respectful. The ones I worked with early in my career were great guys.”
“There’s one other thing to consider,” she continued. “As sad as it is, women will face harassment in any job. Harassment isn’t exclusive to the skilled trades and it shouldn’t hang over the trades like a dark cloud. And it goes both ways. Men face harassment in the workplace from women, too. Harassment should not be a deterrent from this industry, and the fact that it’s still perceived this way shows a lack of knowledge and poor communication on our part.”
There’s a trade shortage in general, and women represent only two percent of the field—that alone represents a huge opportunity and room for improvement.
Because women in the trades are still such a rarity, McGlenen believes it’s important for women who’ve found their path as trade pros to speak openly about the broad range of possibilities.
“Women represent half the global population, yet we’re a tiny fraction of the skilled trade industry,” she said. “Why aren’t women jumping into the industry? Why do we feel our only path to success lies in a college education? It’s lack of representation, and that’s what I want to change.”
Taking it to the turf
After moving to Scotch Creek in 2020, McGlenen, an avid golfer, planned to host 30 of her friends at her local golf course. Then an idea struck her.
“I had this big group of women coming to golf, so why not make it a benefit tournament?” she said. “So, I made it official.”
In 2023, the first annual Babes GDGT (Goddamn Golf Tournament) was held at the Talking Rock Golf in Chase, BC, which benefitted the Women in Trades program at Okanagan College. “Funds raised at the golf event helped provide what women in the program need, including making the transition from the program to employment.”
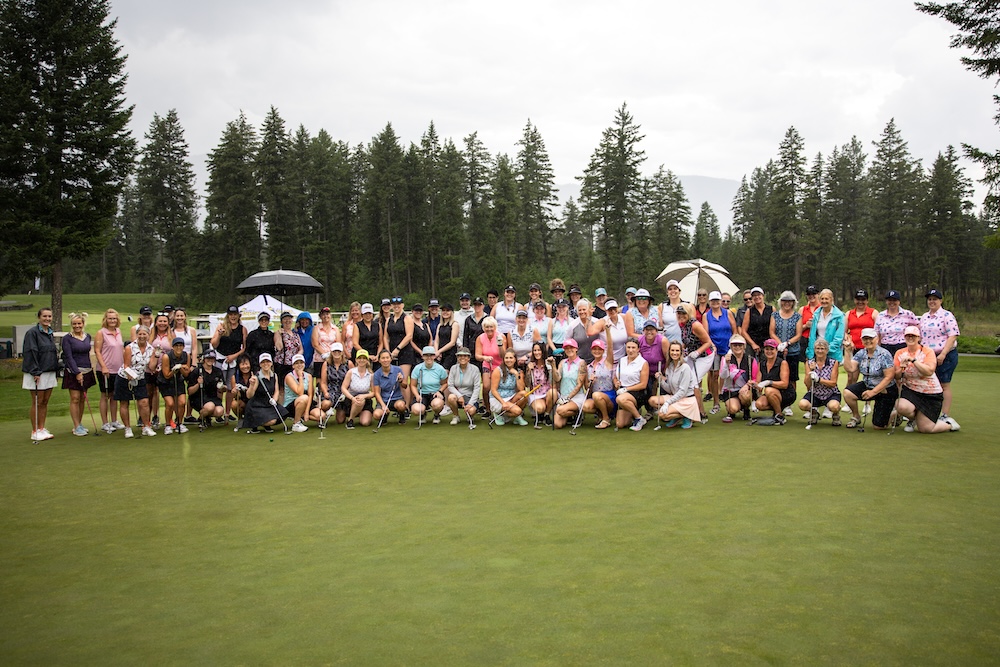
“The goal of the event is to help women achieve the highest level of success possible in their selected skilled trade field,” said McGlenen. “We had 78 women at the golf tournament last year. That was a perfect number. Any more would have been too much for the first year, since I organized that event myself.”
McGlenen draws similarity between the trades and the game of golf. Both are arenas in which women often feel intimidated.
“I think it’s important for women to find excitement and challenge in golf – just as it is in the skilled trades,” she explained. “They need to make an initial push to overcome any hesitation they feel. I use golf as a business tool. Men do it, but women less so. The game can offer great networking opportunities. It’s just a matter of stepping out of your comfort zone.”
Intersecting interests
In 2022, McGlenen was signed into one of Taco Comfort Solutions’ Monday Night Live training sessions when Mike Miller, with Taco Canada, brought up the AHR Expo, suggesting that those in attendance meet up for a round of golf in Las Vegas.
So began the Taco Ryder Cup, in which a US team and a Canadian team go head-to-head on the golf course.
“It was great to meet Lesley in person and play golf with her, especially after seeing her on so many of our online training sessions,” said John Barba, Director of Training at Taco and an accomplished golfer. “She plays very well. For the record, Canada has beaten us both times, but neither of those losses were my fault! Lesley won both her matches and I won both of mine!”
“Meeting the Taco trainers and so many of the people I’d seen on social media was so much fun,” said McGlenen. “I became a part of their learning community during COVID and it’s been invaluable since.”
The COVID lockdowns increased the need for online training for tradespeople across North America, but for McGlenen, the remoteness of her shop means that she needs to look online for training opportunities anyway.
“It’s nearly a three-hour drive for me to get to a training session hosted by a rep or wholesaler, and if I want factory training, it requires airfare. Instead, I just sign in to the “Taco After Dark” or “Taco Tuesday” training sessions. I can learn a lot from Dave Holdorf, John Barba and Rick Mayo without leaving my office. The availability of Taco’s tech support crew and the training I’ve received online gives me the confidence to tackle things I may not otherwise undertake.”
Taco appreciates what McGlenen is doing for the trade, so they’ve stepped up as a key sponsor for the 2024 Babes GDGT event. Mechanical Hub has also stepped up to help support GDGT this year with sponsorships.
Babes GDGT moving forward
The next Babes GDGT (@BabesGDGT) golf event will be held at Talking Rock Golf on June 8, 2024, and it’s already sold out with 128 golfers, and more than a few on the waiting list.
Unfortunately, Okanagan College’s Women in Trades Program was recently cut due to lack of provincial funding. But there are other schools in BC with similar programs.
“The fact that the program was cut illustrates how important it is for the trades to present a compelling and attractive pitch to women,” said McGlenen. “We hope to raise twice as much money this year, and we’re taking a close look at how best to support women in the trades with the funds we raise in June.”
In McGlenen’s battle to increase the skilled trade workforce, she’s quick to remind all tradespeople, not just women, that there’s more than enough work to go around. “Me against you” is the wrong mindset.”
“I hope that offering a new perspective, and enthusiastic advocacy for the trades will help to shift the demographic of tradespeople in Canada,” she continued. “There’s so much opportunity!
“With broader awareness of the trades, especially among women, it could lead to a win-win for all—from home and business owners to everyone in the trades,” she said. “We need to collaborate and develop better processes. It’s realistic and achievable, and I’ll do everything I can to help.”
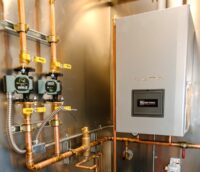
Like most add-ons and accessories, the boiler fuel conversion kit is another easy to forget item that stretches out the installation. In the third and final installment on Alta gas-adaptive technology, we’ll cover why fuel conversion is necessary, what was required to accomplish this in the past, and how simple it is to set the Read more
Like most add-ons and accessories, the boiler fuel conversion kit is another easy to forget item that stretches out the installation. In the third and final installment on Alta gas-adaptive technology, we’ll cover why fuel conversion is necessary, what was required to accomplish this in the past, and how simple it is to set the Alta up for either natural or LP gas.
As with most things in life, it’s best to start with the basics. Propane has roughly twice the BTU/ft3 when compared to natural gas. As such, the technician was historically required to replace or adjust certain gas train components to configure the boiler to operate safely, reliably, and efficiently with the selected fuel. Take cast iron boilers for example. The main orifices, pilot, and sometimes even the gas valve were replaced when transitioning from NG to LP, or vice-versa.
On 5:1 turndown condensing boilers such as the U.S. Boiler Alpine, technicians are required to adjust the throttle screw, and then set up combustion appropriately by tuning the boiler with an analyzer, and on occasion adjust the offset screw as well. On other 10:1 high efficiency, condensing products, a venturi replacement was required to switch from NG to LP, or vice versa. After the venturi replacement, combustion tuning is still required to verify optimal combustion settings.
With the Alta boiler, this conversion process is dramatically reduced to two easy steps, with no component replacement or kits required.
When purchasing a boiler, fuel selection is certainly a primary consideration, and there are a few options when ordering a boiler. Some models are available from the factory set up either for natural gas or propane, while others are shipped set for natural gas and must be converted to operate with propane in the field. The latter is true of all Alta boilers, but lucky for you, fuel conversion on the Alta is super simple!
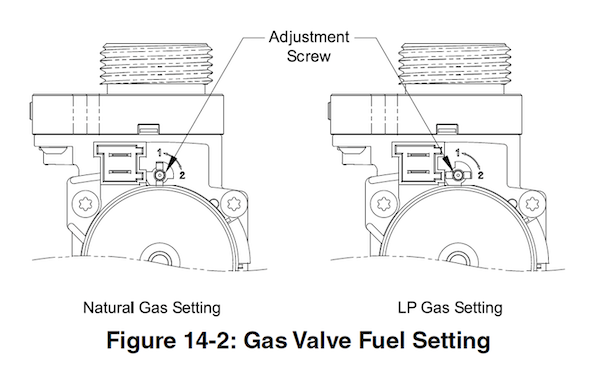
To convert an Alta from natural gas to LP, the technician must turn the fuel screw on the gas valve 1/4 turn to the LP position. Note that on the fuel screw position one is for natural gas, position two is for LP.
Next, simply follow the process listed in the manual to make adjustments on the control.
At this point you may begin looking around for your fuel conversion kit, but as the Alta boiler begins tuning itself for optimal combustion you can simply sit back and relax. The Alta’s gas adaptive system will ensure that your boiler is set for the highest efficiency operation, and all you need to do is press a button.
Is this the end of the gas analyzer?! Don’t put yours up for sale on eBay quite yet. Once your Alta boiler has completed the tuning sequence, we recommend a combustion check just to be sure there is nothing wrong with the venting, combustion air intake, or any other field variables.
So as you prepare for this week there will be hundreds of things to worry about. Are the boiler installs natural gas or LP? Who cares? Skip the conversion kits. Just put in an Alta by U.S. Boiler Company and it will take care of itself.
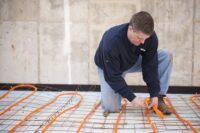
By Kolyn “Coach” Marshall No matter where we go these days it seems as if there’s always someone trying to upsell us on something. Truth is, the art of upsell is nothing new. Walk into a fast food restaurant and you’re asked if you want to super-size it. Go to the theater and you’re asked Read more
By Kolyn “Coach” Marshall
No matter where we go these days it seems as if there’s always someone trying to upsell us on something.
Truth is, the art of upsell is nothing new. Walk into a fast food restaurant and you’re asked if you want to super-size it. Go to the theater and you’re asked if you want to make your popcorn a combo deal. Heck, even Amazon’s in on the program.
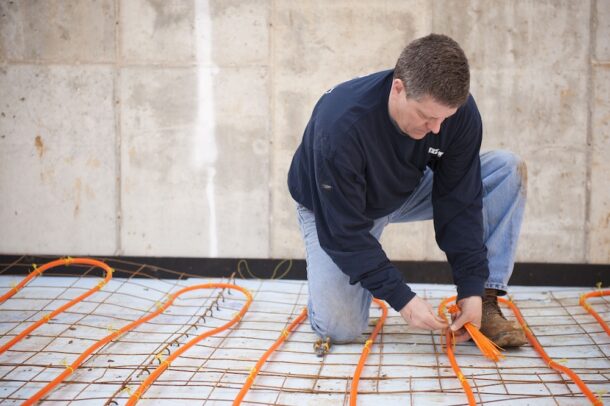
Ubiquitous upsells can be awfully annoying, especially when it’s something you know a lot about. But, what if it’s something you know nothing about? Or, better yet, didn’t know to even ask?
This last question is where I find a lot of potential radiant buyers. They simply don’t know enough about what’s out there to ask.
This is where you—Neighborhood Radiant Installer—come into play.
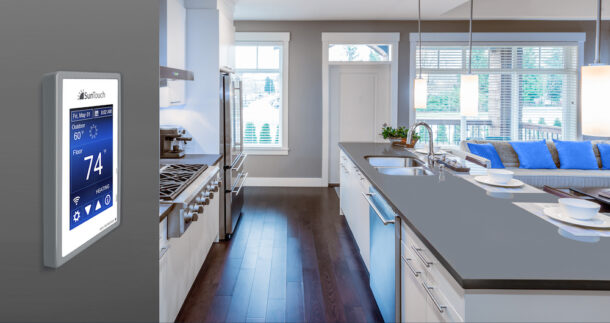
It’s your opportunity to throw out the option of radiant floor heating or snowmelting. Sounds easy, right? Well . . . sort of. In order for you to be able to effectively talk about radiant, it can be helpful to know what there is to talk about.
Understanding the want
Depending on the audience, say, home or a business owner, the want or need may vary. For homeowners, they may want to be more comfortable. There’s a factor of efficiency or cost savings, but those are typically secondary to comfort. People really don’t like being cold.
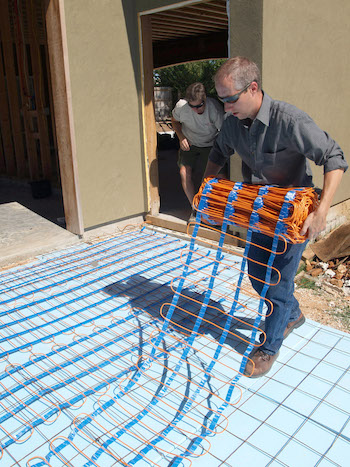
Comfort, however, takes on many forms. But, as the Neighborhood Radiant Installer, it’s important to know what comfort means. One aspect is keeping the room temperature between 68 and 70 degrees. The other facet is knowing how occupants interact with the interior space. The key driver for comfort is floor temperature.
Ever step out of the shower onto a cold tile floor? In that instant it’s pretty easy to connect to what cold is. Oddly enough, our feet dictate our comfort more than air temperature. It’s the main reason why we have slippers and wool socks. If our feet are warm we feel warmer.
So the easiest way to feeling comfortable is to keep the floors from being cold. Radiant heat does that with most radiant systems maintaining a floor temperature between 75 and 85 degrees.
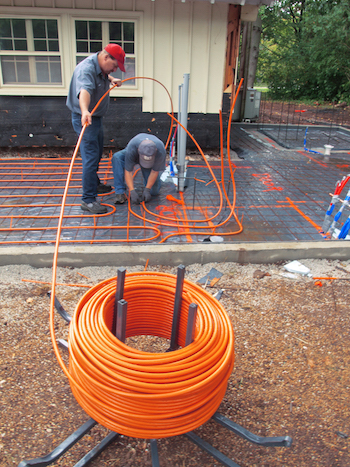
Business owners tend to have a slightly different goal in mind. Their focus is more on customer safety, especially when the weather turns cold and the freezing rain and snow start to fall. Or: employee satisfaction, a great incentive in retaining, and attracting, employees.
As for safety, injuries due to slips and falls plague business owners constantly. It’s a seasonal risk, and source of concern.
Radiant snowmelting systems help keep walkways, parking lots, and access ramps ice and snow free all winter long. This means no more early morning labor; shoveling snow is a thing of the past. No more chemical ice melt. This alone eliminates another key concern: icemelt tends to get picked up by customer’s shoes and tracked inside, eventually taking its toll on the floor.
The upgrade package
So a spark is struck. Warm floors are something that wasn’t expected but is now very much wanted.
How are these once cold floors now warmed? There are two main ways to provide radiant floor heat: hydronically with water, or through electric resistance.
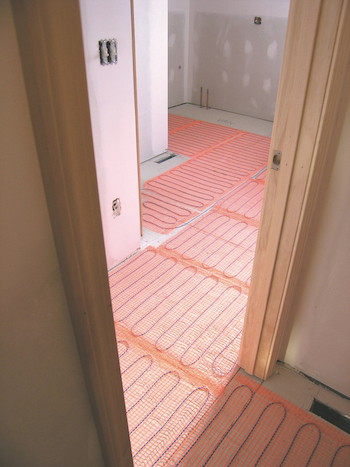
Hydronic systems rely on tubing being installed in the floor and connected to a heat source. Tubing options range from PEX, to PE-RT, to EPDM rubber. Tubing is connected to a series of manifolds, then those manifolds connect to a boiler, or other equivalent heat source.
If the area to be heated is small, say only a kitchen or bathroom, then an electric product may be best; these use electrical resistant wire or cable to generate heat. Wire is embedded in a lightweight concrete or thinset generally under tile or other masonry material. One of the advantages of electric is there is no need for a mechanical room and no need to physically run piping back through a home or facility. Electrical installations tend to be less invasive but also tend to be reserved for smaller areas.
With both electric and hydronic systems there are options for controls and thermostats. Most of today’s systems incorporate some form of connectivity feature, giving remote access to users.
Delivering the Goods
Congratulations Neighborhood Radiant Installer! The Enlightened Customer has decided to go with the radiant upgrade. Now what?
Now it’s time to figure out how to get all those tubes and wires where they’re supposed to go.
Hydronic tubing is generally installed in one of two ways, either in a concrete slab or under a frame floor. In a concrete slab, tubing is typically 6, 9, or 12 inches on center with the tubing approximately 2 inches down from the top. In a frame floor, the tubing is secured to the subfloor, often with heat transfer plates. These plates secure the tubing (usually PEX or PE-RT) to the subfloor while providing good conductive heat transfer to the floor.
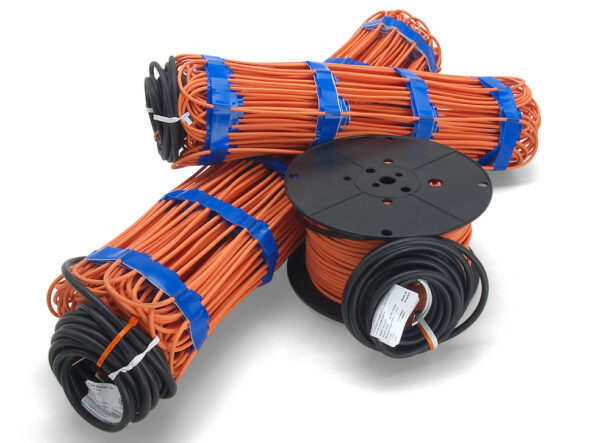
Electric systems are installed in a similar fashion to hydronic slabs with the difference being the wire is generally installed on top of the floor in ½ inch thinset with tile or other stone material as the finished floor covering. An electric system is then connected a controller or thermostat.
Both hydronic and electric systems then operate in the same way any forced air system does. The controller or thermostat is set to the desired temperature and the system operates automatically.
Satisfied Customers
So how does our Neighborhood Radiant Installer know the system is working as expected and the customer is happy? It’s simple: our Honorable Customer won’t be able to stop talking about the most comfortable heat they’ve ever experienced.
Becoming the go-to radiant expert is the best way to keep the future looking warm and bright.
Kolyn “Coach” Marshall, based in Springfield, Mo., is Systems Engineering Manager at Watts Radiant.