By Aaron Stotko When a century-old Dallas railroad company headquarters required major renovations to transform into a Homewood Suites by Hilton, initial cost estimates for the hydronic heating system came in too high. That’s when City Wide Mechanical of Dallas looked to alternative piping systems for a solution. They found PEX-a pipe with F1960 expansion Read more
Featured Articles
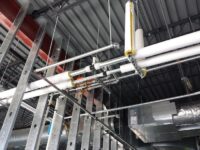
By Aaron Stotko
When a century-old Dallas railroad company headquarters required major renovations to transform into a Homewood Suites by Hilton, initial cost estimates for the hydronic heating system came in too high.
That’s when City Wide Mechanical of Dallas looked to alternative piping systems for a solution. They found PEX-a pipe with F1960 expansion connections to be the ideal system, due to its durability and ease of installation in addition to the job-site productivity, safety and, best of all, profitability potential it provided.
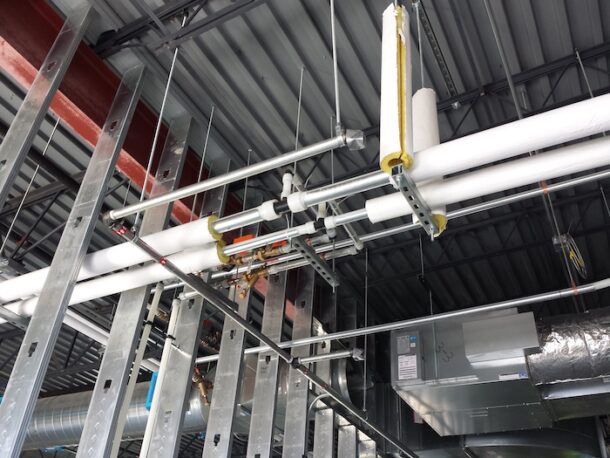
And City Wide Mechanical isn’t alone in their findings. Many mechanical contractors are discovering the benefits of PEX-a pipe and F1960 connections as the preferred alternative to copper, iron, and steel, which have dominated the mechanical piping industry for decades.
Benefits of PEX-a
PEX is an acronym for crosslinked polyethylene. It has been used in North America since the mid-1980s, starting with radiant floor heating systems, then moving into plumbing and, eventually, to hydronic hot-water heating and chilled-water applications.
PEX can be manufactured via three different processes, which create products with varying crosslinking percentages that allow for different characteristics. PEX-a is the most durable, flexible, and resilient with crosslinking around 85%. PEX-b is a stiffer piping product with crosslinking around 65% to 70%, and PEX-c features crosslinking around 70% to 75%.
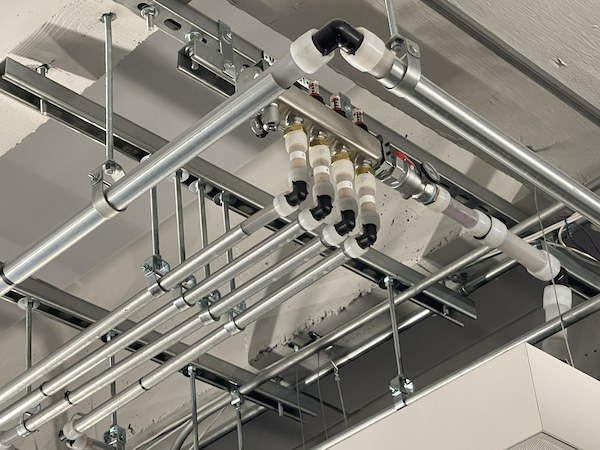
ASHRAE Headquarters Grand Opening Fall 2021, photos by Devin Abellon
One major benefit of the higher crosslinking in PEX-a is its extreme flexibility along with its thermal and shape memory. The flexibility of PEX-a eliminates most connections in smaller-diameter piping, saving time and money with up to half the connections required in rigid metal piping systems. To make a change in direction, the installer simply bends the pipe instead of having to stop and make a fitting. There are also bend supports available that help hold a bend securely in place.
The thermal memory of PEX-a provides kink repairability with a simple shot of heat from a heat gun. This eliminates the need to add in a coupling if a kink ever occurs in the pipe. (It is important to note that kink repairability is not possible with PEX-b or PEX-c pipe.)
The shape memory of PEX-a allows the pipe to expand and contract back down to its original shape. This makes it extremely resilient in freezing conditions and also provides for the fastest, easiest, most reliable PEX-a fitting system — F1960 expansions.
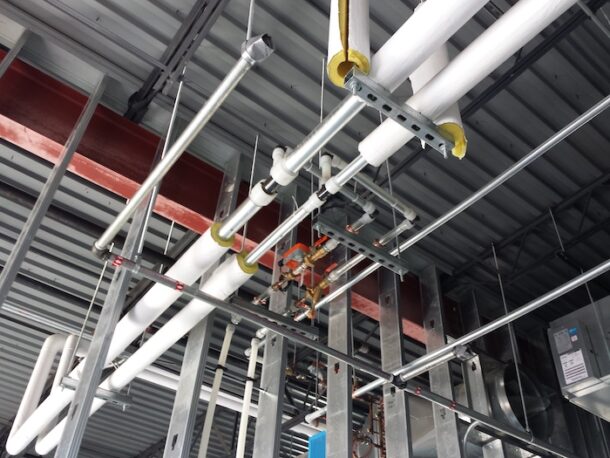
Expansion fittings require one simple tool to expand the pipe and an expansion ring before inserting a fitting. As the pipe and expansion ring naturally shrink back to their original shape, it creates a strong, durable connection that holds tight and can never be dry-fit. (Note: It is not recommended to expand PEX-b or PEX-c pipe due to microcracking that can occur.)
The innovative expansion fitting method eliminates torches, glues, and solder from a job site for greater worker safety. Plus, the system is extremely easy for installers to learn, helping get new crews up to speed quickly.
Speaking of job-site safety, PEX is also much lighter in weight compared with metal systems. For example, a 300-foot coil of 1/2-inch PEX weighs about 18 pounds, whereas the same amount of copper pipe weighs around 85 pounds. The lighter weight of PEX makes it safer and easier for installers to move around a job site and also eliminates the need for heavy-lifting equipment.
PEX-a also has a long-term advantage over copper when it comes to performance longevity. It is a static system, meaning its internal surfaces — which are three times smoother than copper — will not pit, scale, or corrode. That means its performance will remain the same from day one through decades of use.
Finally, because it is not a traded commodity, PEX-a holds a relatively stable material cost. This makes bidding a project much more consistent and reliable.
Application Details and Installation Tips
PEX-a is regulated by the ASTM F876 standard, which denotes temperature and pressure ratings of 200°F at 80 psi (pounds per square inch), 180°F at 100 psi, and 73.4°F at 160 psi. These values are well within the range of operation for most hydronic systems, including chilled beams, fan coil units, baseboards, radiators, hydronic VAV (variable-air volume) reheat coils, and radiant manifolds.
Because PEX is oxygen-permeable, it is important to use a pipe with an oxygen barrier that limits oxygen diffusion to levels below DIN 4726. This will protect the metallic components in the mechanical piping system, such as valves, strainers, and pump volutes, from corrosion.
The pipe is manufactured in sizes from 5/16 inch up to 4 inches and features a copper tube size (CTS) outside diameter. This means all the off-the-shelf components used in a copper hydronic piping system — hangers, supports, and insulation — can be the same.
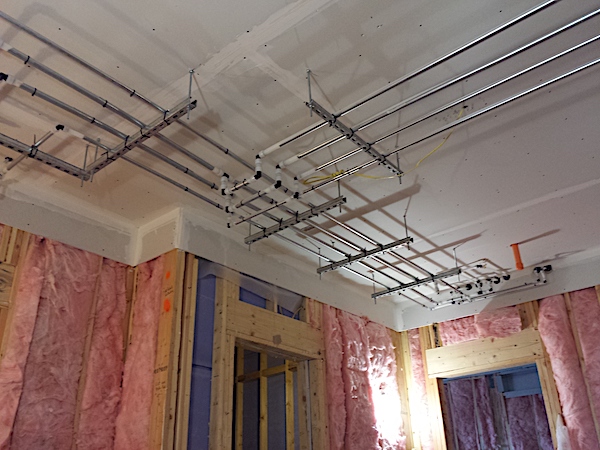
For horizontal piping, the industry offers PEX-a Pipe Support — a galvanized-steel channel that is 9 feet in length and available in PEX pipe sizes from ½ inch to 3½ inches. This solution enables hanger spacing similar to copper pipe and helps control the natural expansion and contraction of the pipe as it heats and cools.
Because PEX-a expands at 1.1 inches per 100 feet per 10°F Delta T (which is 10 times that of copper), installing anchors every 65 feet and using PEX-a Pipe Supports allows PEX-a to function much like a copper system. In fact, different installation methods have a different effect on the overall net expansion rate.
With a strut-and-clamp system, using PEX-a Pipe Supports and anchoring with fixed points reduces the expansion rate of PEX-a to 0.08 inches per 100 feet per 10°F Delta T (a rate less than copper). And a loop-and-clevis system can reduce the rate to 0.12 inches per 100 feet per 10°F Delta T.
If you’d like to learn more about PEX-a piping systems, visit the Plastics Pipe Institute at plasticpipe.org or the Plastic Pipe and Fittings Association at ppfahome.org.
Aaron Stotko is the director of Segment Marketing at Uponor. He can be reached at aaron.stotko@uponor.com.
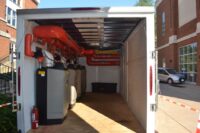
The University of Virginia sought a way to quickly provide temporary heat during construction projects while also reducing boiler rental expenses. The solution was the development of two innovative mobile boiler trailers that provide on demand heat where it’s needed. The University of Virginia is a public research university in Charlottesville, Va., founded in 1819 by Thomas Read more
The University of Virginia sought a way to quickly provide temporary heat during construction projects while also reducing boiler rental expenses. The solution was the development of two innovative mobile boiler trailers that provide on demand heat where it’s needed.
The University of Virginia is a public research university in Charlottesville, Va., founded in 1819 by Thomas Jefferson. It is the flagship university of Virginia and home to the Academical Village, a UNESCO World Heritage Site.
Like many large, historic universities across the country, especially in the Midwest and Northeast, the University of Virginia utilizes central steam heating plants that pipe steam and heating water to campus buildings.
The university is in the second year of a five-year project to convert its steam systems to low temperature hot water for more efficient heating across the grounds.
“During a pipe or heat exchanger replacement, we would typically rent boilers to heat the affected buildings,” said Cameron Ratliff, associate director of utilities distribution with the University of Virginia. “However, boiler rental costs were expensive, and so we were looking for a more cost-effective solution for temporary heat.”
The university team came up with an innovative idea: build its own custom mobile boiler trailer.
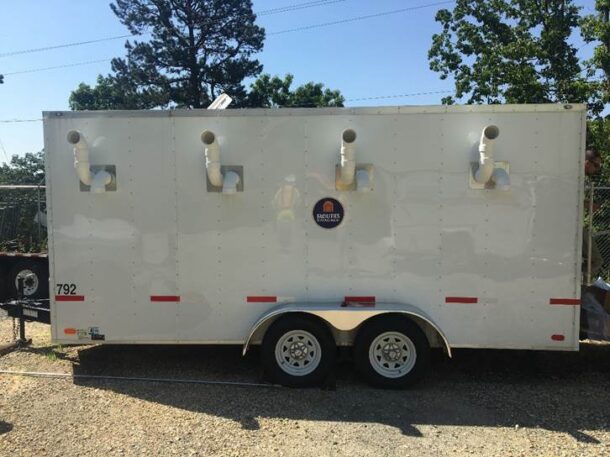
Building the Trailers
Collaborating with Ferguson Plumbing Supply, its main supplier for pipes and fittings, and SE Burks, an HVAC solutions and equipment company, the university facilities team came up with the idea to develop a mobile heating system using a 7½ x 20 ft. trailer and an 8½ x 24 ft. trailer as the housing. The team selected four Weil-McLain boilers to serve as the heart of each system.
“We developed our first mobile heating trailer with four Weil-McLain Ultra boilers for a total output of 1.2 million BTUs to provide temporary heat if a building’s heating went down,” said Ratliff.
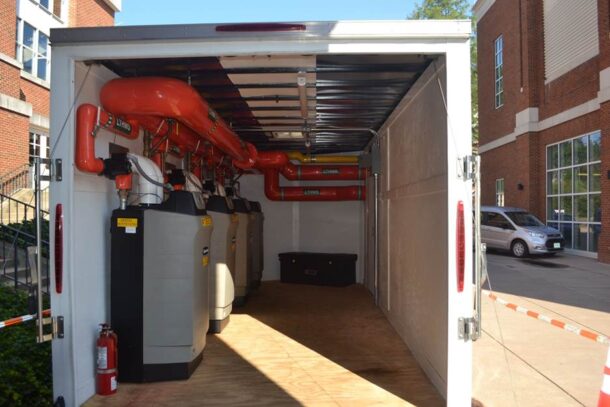
The Weil-McLain Ultra boiler is designed to operate in low temperature condensing applications and features a coated cast aluminum heat exchanger, up to 94% AFUE efficiency and high- grade stainless steel burner with quiet operation. In addition to the boilers, the trailer was outfitted with connections for fuel, water and electricity.
It didn’t take long for the University of Virginia to put the mobile boiler trailer into action.
“Carruthers Hall lost its boilers during the winter, and we had our 1.2 million BTU trailer connected in one day to provide temporary heat while we serviced the boilers,” said Ratliff.
With the success of the first trailer, the University was determined to build a second mobile heating trailer with even more heating capacity.
“The design for our second trailer required a powerful, efficient boiler that could meet our target BTUs while also fitting in an 8½ x 24 ft. trailer,” said Ratliff. “I researched the Weil-McLain SlimFit unit, and it seemed perfect for the application. We chose the 750K BTU SlimFit models as they were the largest units we could fit and because they operate on either propane or natural gas.”
Wes Collings from SE Burks offered guidance on selecting the boilers, and the facilities department teams installed the boilers.
“The SlimFit was an ideal choice for the small footprint of these trailers and because of the unit’s easy serviceability,” said Collings. “The university included extra pipe connections so two more units can be added to increase the capacity even more.”
The SlimFit boiler’s narrow housing enhances maneuverability for confined spaces and weight restricted areas. The design also increases usability and access for installing contractors, consulting engineers and facility managers for commercial retrofit projects.
With the four SlimFit units installed, the University now has a second boiler trailer with a total heating capacity of 3 million BTUs with the option to add two more boilers to increase it to 4.5 million BTUs if needed, for larger heating season applications.
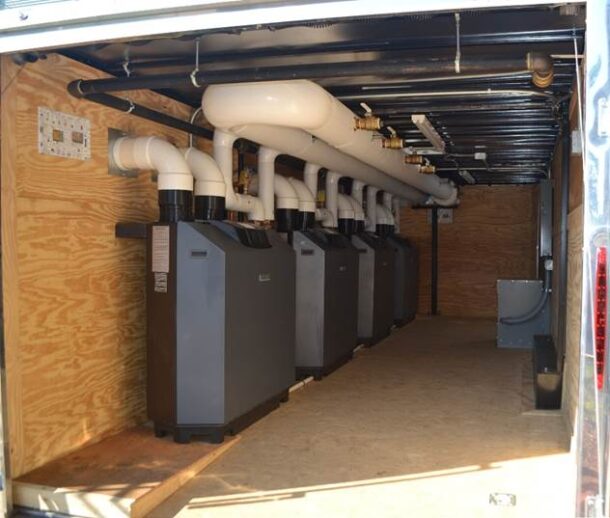
As the university transitions from steam heat, the facilities team also is creating temporary connections for easy connectivity to the trailers.
“We are removing heat exchangers and inserting blending loops with PICV valves and temperature regulators, so all of our buildings are directly connected to the plants,” said Ratliff. “Should we have an emergency breakdown, we can simply pull up the trailer and it’s plug and play.”
Temporary Heating on Demand
“We now can heat the majority of our facilities on grounds at any time with these trailers without having to rent boilers,” said Ratliff. “Waiting for a rental boiler is not an ideal option during the heating season when these systems are in peak demand.”
Ratfliff also notes that the small size of the trailers is advantageous, too.
“The trailers are easy to move around the grounds,” he said.
Besides having on-demand heat as needed, the university is experiencing significant expense savings from expensive boiler rentals.
“Our University CFO is not only intrigued by these trailers but also quite thrilled with the cost savings,” Ratilff added.
Ratliff noted it was a team effort to design the mobile heating systems.
“We really enjoyed putting out heads together to build these trailers,” he said. “It really is the perfect application for our university; the cost savings alone make it so worth it.”
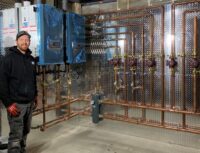
“Any day building custom mechanical rooms is a great day,” says Tyler Dynes (@dyneshvac), lead installer—with a specialty in hydronics—for Farr Mechanical Corp., greater Toronto area. You see, for Dynes, the most rewarding part of his work is seeing the finished install and hearing the customer say, “this is the nicest room in the house.” Read more
“Any day building custom mechanical rooms is a great day,” says Tyler Dynes (@dyneshvac), lead installer—with a specialty in hydronics—for Farr Mechanical Corp., greater Toronto area. You see, for Dynes, the most rewarding part of his work is seeing the finished install and hearing the customer say, “this is the nicest room in the house.”
In fact, Dynes loves what he does so much, one of his bucket list items is building his own home with a custom hydronic system.
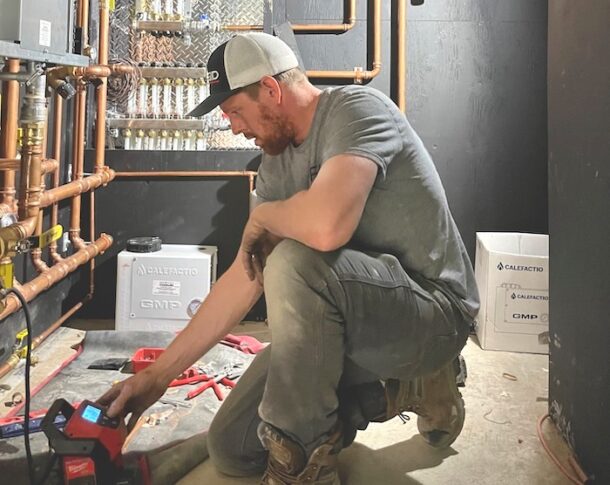
Dynes’ rise into the trades started right out of high school where he began a career in automotive mechanics. After a few years in the field, he soon realized it just wasn’t for him. After speaking to someone at a local fuel/HVAC company, Dynes decided to give working for them a try. Several of his friends were in the industry already and encouraged him to enter the trade. “I worked with that company for about 11 years, learning everything I could in the residential HVAC field. It was here I became a gas fitter, oil burner and started my AC apprenticeship,” says Dynes.
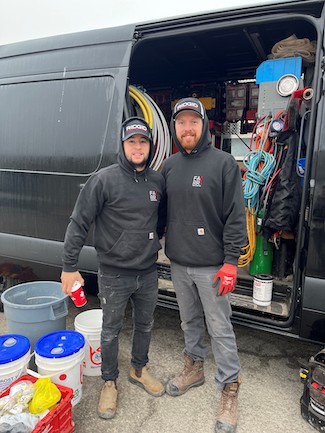
Tyler with Brandon Farr (l), owner of Farr Mechanical.
One of my Dynes’ first mentors was a seasoned tech named Chris who Dynes trained under for five years at that first HVAC company. I also follow the careers of Eric Aune (@mechanicalhub), Mike Flynn (@flynnstone1), Don Taylor (@dontaylor53) and Aaron Bond (@bond_aaron) closely on Instagram. “They inspire me to push myself and learn more about all the different aspects of the trade. I still look up to them and chat with them from time to time,” says Dynes.
Dynes hadn’t considered himself a role model, just someone who takes a lot of pride in what he does. “I hope that I can encourage people to join the trade, and for those already in it, to push themselves to learn new skills. I would love for people to look at my work and be able to ask questions to help them learn everything I have and beyond,” says Dynes.
And with that, social media has allowed Dynes to grow professionally and personally as he loves the relationships that he’s built through it. Dynes is amazed at the support and encouragement he’s received over the last few years through his Instagram posts and stories. “It has such a great community of people from all trades supporting each other,” says Dynes.
Yet social media can become addicting, says Dynes, and it can be hard to step away. “After I get home, there are usually questions or conversations that happen through Instagram about my posted installs or other people looking for advice. I try to help when I can, but I know it’s important to put my phone down and spend time with my family, which can be going to the cottage with his family and riding his dirt bike,” says Dynes.
Over the past decade, there is no debating social media has become a place where contractors can show off their work and wares, and connect. This should help enhance the trades. “We need to showcase the fun side of trades and that no day is ever the same. There are so many areas that you can excel or specialize in, and we need to make that more known to people. It’s a hard work, fast-paced environment, but it’s so rewarding when you get the freedom to be creative,” says Dynes.
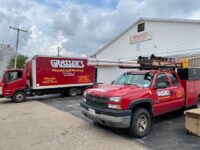
https://youtu.be/46yc2caCGzo A quick Hub on the Road takes us to Grasser’s Plumbing & Heating in McNabb, Ill., to visit with Tim Kuhlman to talk about the company, its new showroom, inventory and supply, and a plumbing truck tip Read more
A quick Hub on the Road takes us to Grasser’s Plumbing & Heating in McNabb, Ill., to visit with Tim Kuhlman to talk about the company, its new showroom, inventory and supply, and a plumbing truck tip.
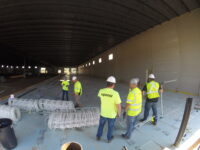
For the company’s 85th anniversary, Freeborn Mower Electric Cooperative in Albert Lea, Minn., decided to build a brand-new facility to house all their equipment, trucks, and employees in one location. The new 97,000-square-foot, $17 million structure featured several high-tech, sustainable building practices, including radiant floor heating throughout the entire building. Being an electric cooperative that Read more
For the company’s 85th anniversary, Freeborn Mower Electric Cooperative in Albert Lea, Minn., decided to build a brand-new facility to house all their equipment, trucks, and employees in one location. The new 97,000-square-foot, $17 million structure featured several high-tech, sustainable building practices, including radiant floor heating throughout the entire building.
Being an electric cooperative that serves 21,045 members in two counties with 2,950 miles of line, they wanted the most energy-efficient method for heating their structure, which meant a radiant floor heating system using Wirsbo hePEX™ pipe along with an underground distribution system using Ecoflex® pre-insulated piping.
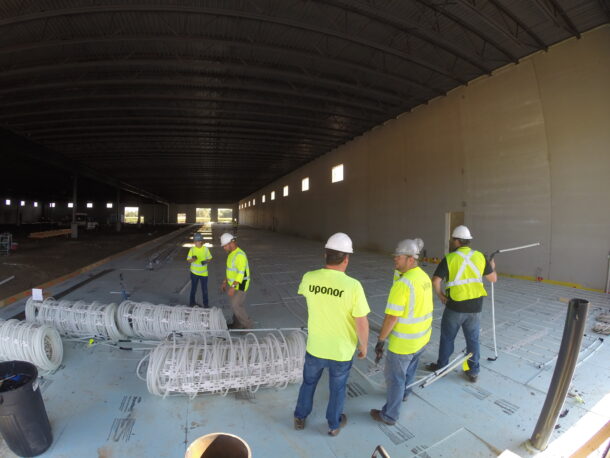
Despite construction being done during the height of the COVID-19 pandemic in 2021, all the construction partners came together to complete the project quickly and under budget. This was thanks, in part, to the efficiency of the Uponor Radiant Rollout™ Mats for the radiant heating system, which saved significant install time and labor costs.
Taylor Bestor of Valor Mechanical, the radiant contractor, had been installing commercial systems since 2007, but had always used traditional methods of wire ties or foamboard staples. When the engineer’s specification called for preassembled radiant mats, Taylor was curious about how the installation would go, knowing he needed to align with concrete-pour schedules to stay on the customer’s tight timeline.
To learn more about these preassembled radiant mats, Taylor met with Ryan Swanson of FourMation Sales, an Uponor manufacturer rep firm. Ryan told Taylor about the Uponor Radiant Rollout Mats and how they could “cut labor by one third.” Of course, after hearing about the incredible installation efficiencies, Taylor was interested in how this technology worked.
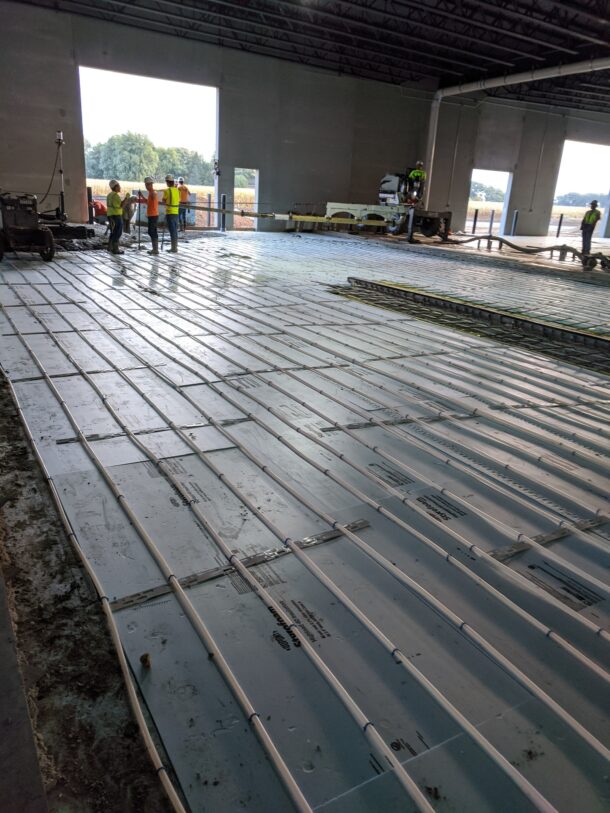
Once he learned that the mats are custom designed by Uponor Construction Services to fit the space and come to the job site preassembled and pre-pressurized, ready for installation, Taylor was on board with moving forward.
Paul McCulloch from Uponor, along with Ryan, were there for the first install to guide Taylor and his team with the mats. The crew made a plan to complete the radiant tubing install in thirds to work with the concrete pours.
“We started out by training about 10 guys to get an understanding of how the mats worked,” says Taylor. “By the last third of the project, we were able to do the entire install with three guys in one day. Using traditional wire ties or staples would have taken more than double the workers and triple the time.”
Because the project included complete layout designs from Uponor Construction Services, Taylor and his team were able to efficiently and effectively install the Radiant Rollout Mats as well as the radiant perimeter, which used a staple-down method. They also installed Ecoflex pre-insulated pipe for the underground piping to the Uponor TruFLOW™ manifolds, which, Taylor says, “worked out perfectly for the install”.
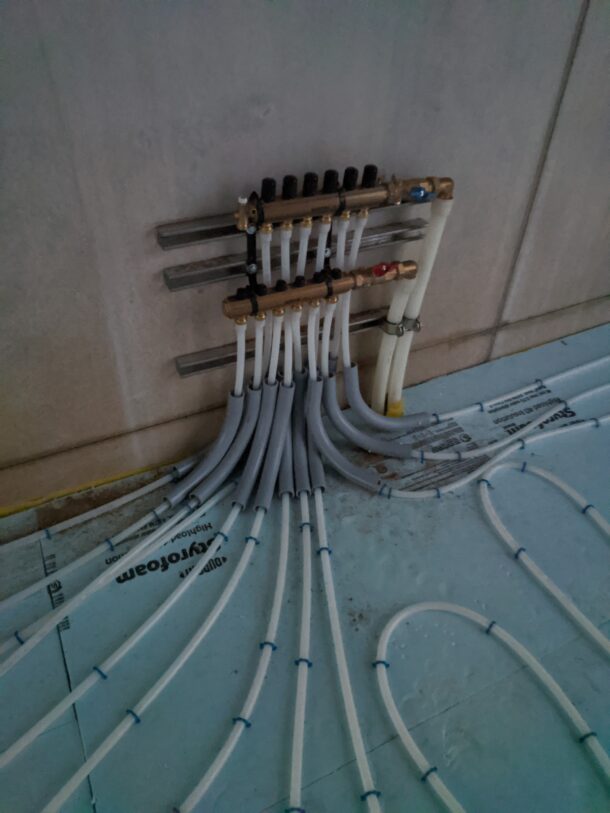
After his experience with the extreme efficiency of the Radiant Rollout Mats, along with the support from the Uponor sales team and Uponor Construction Services, Taylor is convinced of their effectiveness and is anxious to use them again in a future large commercial radiant project.
To learn more about Uponor Radiant Rollout Mats or other radiant installation methods, visit www.uponor.com.