Starting over 60 years ago in a small province in northern Italy, Caleffi has increased its footprint, expanded its international presence, survived the current pandemic, all the while manufacturing some of the most innovative PHVAC, heat metering and renewable products in the world. This past fall, Mechanical Hub was honored to tour the Caleffi S.p.A Read more
Featured
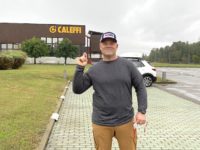
Starting over 60 years ago in a small province in northern Italy, Caleffi has increased its footprint, expanded its international presence, survived the current pandemic, all the while manufacturing some of the most innovative PHVAC, heat metering and renewable products in the world.
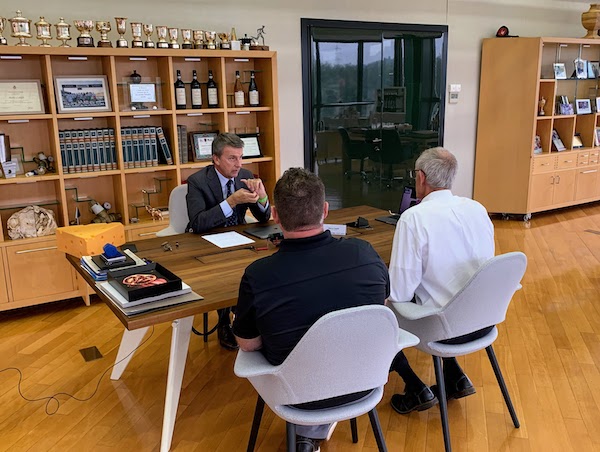
Chairman Marco Caleffi talking with Bob ‘Hot Rod’ Rohr and MH’s Eric Aune, while on an overseas video call with MH’s John Mesenbrink.
This past fall, Mechanical Hub was honored to tour the Caleffi S.p.A. global headquarters in Fontaneto d’Agogna, Italy. We were joined by Bob “Hot Rod” Rohr, Training and Education Manager, Caleffi North America. Afterward, we sat down to chat with Chairman Marco Caleffi. To break the ice, we asked Marco what type of sports he enjoys watching, whether it be American football or European soccer. Marco promptly reached to the shelf behind him and put a vibrant yellow cheese wedge on his head, signifying his admiration for the Green Bay Packers and solidarity with Caleffi’s North American headquarters, located in Milwaukee, Wisconsin. In disbelief and shock—as I am a Chicago Bears fan—I appreciated the gesture, but I needed to change the subject, and quickly!
A Taste of Caleffi
Upon arrival we were greeted with an impactful historical display of how Caleffi S.p.A.’s site was first constructed and the many expansions it has experienced in the decades since. During our walking tour, we were led through the entire manufacturing process—from the brass bar stock to final packaging of literally thousands of catalog offerings. “I’ve been on a fair number of factory tours, but I can say none showcase new technology and innovative manufacturing methods quite like Caleffi did,” said Eric Aune, co-owner, Mechanical Hub.
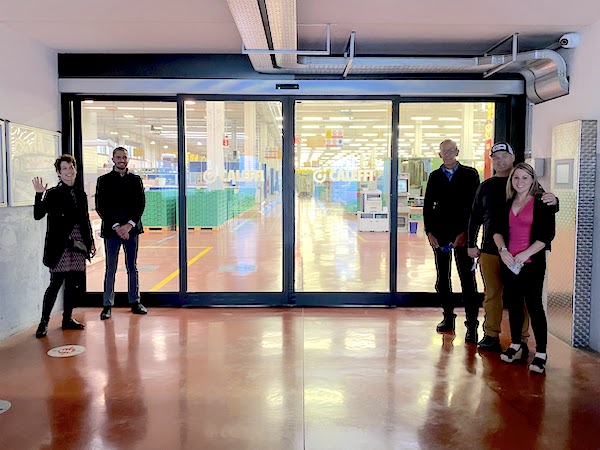
Standing at the entrance to the plastics manufacturing plant, from left: Ellen Rohr, Fabio Rossi, Hot Rod Rohr, Eric Aune & Heather Aune.
With all the technology, synchronization and automated machinery, there still exists a proud workforce that is instrumental in the final product sold to plumbers, HVAC techs and other contractors around the world. “It was so cool to meet the people responsible for the products we buy every day. Equally as impressive, we were able to watch the process as literally every product Caleffi manufactures is tested before final packaging ships. I was blown away—the tour and people are first class all the way,” said Aune.
60 Years of Leadership
In 1961, beginning with two small lathes in his basement used for parts he crafted for OEMs, Francesco Caleffi founded the company. Fast forward to today and the Caleffi Group has grown to employ 1,400 people worldwide with subsidiaries and commercial offices in 18 countries. It produces and moves products via four Italian manufacturing and logistics facilities. Unlike other companies that are in the third or fourth generation, Francesco started from the beginning. “My father was like a hurricane. To be honest, he was able to build Caleffi in only one generation,” said Marco Caleffi.
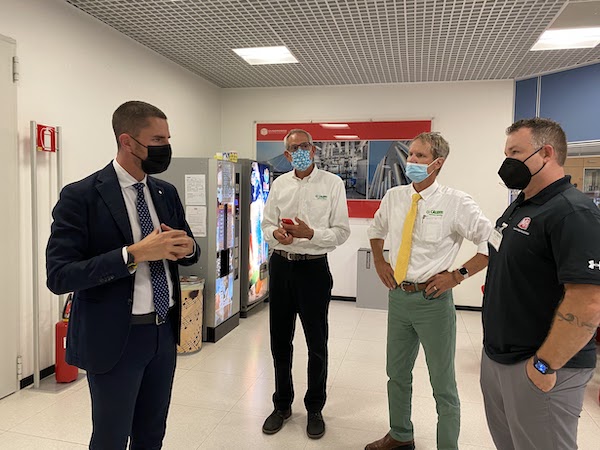
Fabio Rossi about to give the Caleffi tour with Hot Rod, Mark Olson and Eric Aune.
Marco boasts that his father was a good mechanic, personally machining items and producing spare parts for other companies. “After two years, my father decided to make new, finished products such as air vents and safety valves,” said Marco. As technology advanced, automation became a big factor in the company’s success, a key contribution Marco’s father pushed for. “With forward-thinking automation, we have far greater control over quality. The standard of consistency is much, much better than manned assembly.”
From the beginning, what set Caleffi apart from competitors was “while they were only making ball valves, fittings and manifolds we were much more focused on the needs of the systems while making valves, fittings and manifolds,” continued Marco.
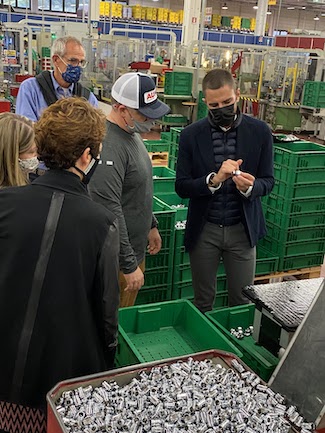
Fabio showing the details of how every catalog item is tested before leaving the plant
Early in Caleffi’s development, an instrumental partnership was formed. Marco’s uncle, Dante Bonini, joined Francesco Caleffi and was responsible for building a new commercial division. According to Marco, the two created a nice collaboration and they were a good balance for each other. “My father was difficult to manage because he wanted new buildings, new facilities and new investments before we needed them,” chuckled Marco.
Bonini offered a calming temperament that assisted Caleffi in making strategic moves when the time was right. “When we moved from the Gozzano regional plant in the Italian province of Novara, we bought this piece of land with room to grow in Fontaneto. It is still our headquarters today. Since the day we arrived, it has been our intention to expand,” said Marco.
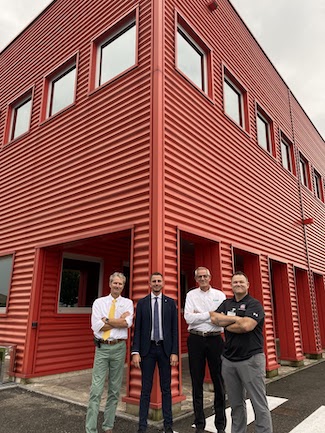
In front of the CUBOROSSO (from l to r): Mark Olson, Fabio Rossi, Hot Rod Rohr and Eric Aune.
In 2008, Caleffi opened its new research center, named CUBOROSSO, a bright red building where products are researched, developed and tested. It is a building that stands in stark contrast with the others on the Caleffi campus. “It represents the color of the Italian mechanical ‘soul,’” said Marco. “Like Ferrari, Ducati and Alessi, red represents the mechanical side of Italian innovation.
In 2009, Caleffi continued its investment in innovation with its completely unmanned Automatic Vertical Warehouse (MAV), which improves customer service by optimizing logistical processes. When the storage and handling of goods are entirely automated, the result is shorter processing times and minimized operator error—the standard quality aforementioned by Marco. “It is critical to have finished products for delivery and spare parts for what is needed in assembly,” said Marco.
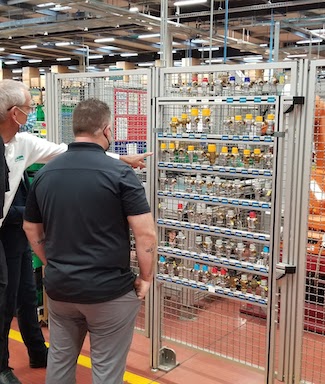
Checking out the “wall” of mixing valves.
“Everyone said it was so clean and modern, but it’s not until you’re on the floor and walking around that you realize you don’t see piles of materials and parts,” observed Aune. “Everything is very organized to the point where in the assembly stations, they move only the materials they need for a certain amount of time and a certain amount of product and then move them out quickly to be replaced with the next product. Everything was very orderly. It seemed that everything had a place. You could tell that that’s how they operate every day, not just because we were touring.”
If You Build It, They Will Come
In the 1980s, Caleffi was ready to expand into Europe and opened its first subsidiary in Germany. By the 90’s, another followed in England. “When we decided to expand, the initial branch was targeted for Germany because it’s a country that is associated with the ‘mechanic’s reference for innovative, precisely manufactured technology.’ There are a lot of German car makers, valve producers and boiler companies. We experienced nice success in Germany and then expanded into England. Now, 25 years later, we continued making our way into the U.S. and Canadian markets,” said Marco.
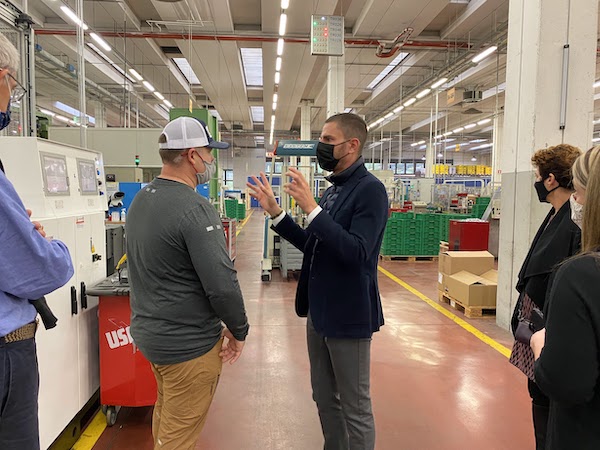
Fabio conducting the tour.
That introduction into North America came in 2001 when Roger Michaud and Rex Gillespie joined with Caleffi S.p.A. to begin pioneering the market. Mike Schreiner, now Chief Technology Officer, signed on in 2003 to develop a new zone valve line which ultimately became a key factor in Caleffi’s early growth.
From Caleffi S.p.A., Sergio Casarino was appointed Area Export Manager responsible for North America. He became an expatriate and for two years lived in Milwaukee to help get the fledgling business off the ground. Giovanni Monti, now General Manager, strategically positioned the growing world-wide company, providing a balanced configuration of management expertise and direction.
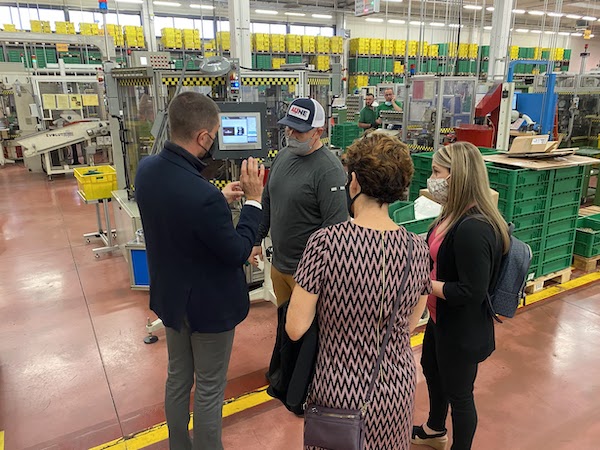
To further accelerate growth and organize North America for expansion, veteran Mark Olson was hired as CEO in 2005 where he continues to serve. Caleffi then began bringing on seasoned hydronic and plumbing experts such as Bob “Hot Rod” Rohr to head training and Roger Corrente to head sales.
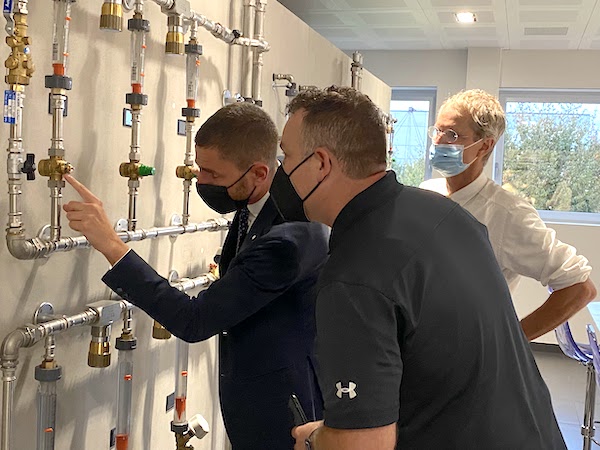
Working piping systems are on display in the CUBOROSSO training center
Marco explains, “Once the decision to expand into North America was made, we were committed to deeply understanding the unique design elements in their hydronic and plumbing systems. We rejected the idea that we had to introduce this Italian valve or that Italian valve. If you understand the system needs, you can then devise better products for that market. With the balance of the right product configurations and management expertise, we are finding success in the North American market. It’s not easy when an Italian company goes elsewhere—such as to the U.S.—to find success.”
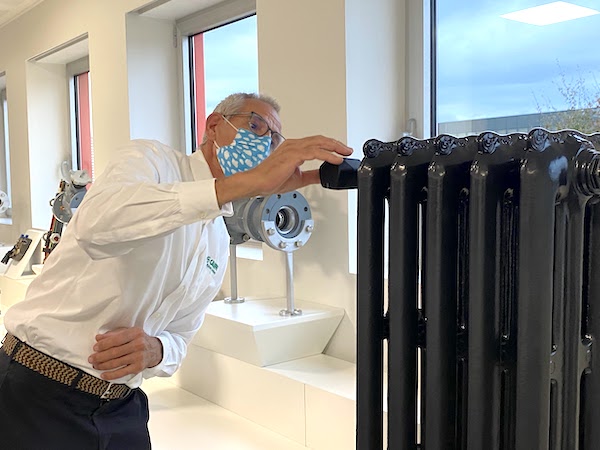
Hot Rod closely inspecting a radiator.
Bob Rohr further explains, “We’ve seen companies come into the U.S. and say ‘you’re going to do it the way we do it in our home country’ and most often it doesn’t work. Mark was smart to emphasize listening and observing: what do the American products need to be? A big part of our success is listening to the market instead of taking our way of doing business in some other place of the world and trying to force it into the market.”
To that point, training plays an integral role. Commented Marco, “We must learn and teach the system needs of our markets. In North America, applying the experience and reputation of experts like Hot Rod makes it much easier to extend our success. I think Bob and other veterans we hired have been key factors to our success.”
“Before Mark Olson came on board, our focus didn’t extend much beyond simply selling. Mark brought a technical and market-based mindset. With his influence, we became more organized and stable. Today we have a premium market reputation with a deep technical staff and strong after sales support. With around 50 employees in the States, it’s almost like another company,” said Marco.
A COVID Epicenter
Early in 2020, Italy was one of the first countries ravaged by COVID-19. Caleffi was proactive even before the government shutdown. “Two days before the Italian government shut down all production, I personally decided to halt production because it was too difficult. The hospitals were full of patients. There were people working in the office and in production without knowing what could happen. It was a tough time, to be honest,” said Marco.
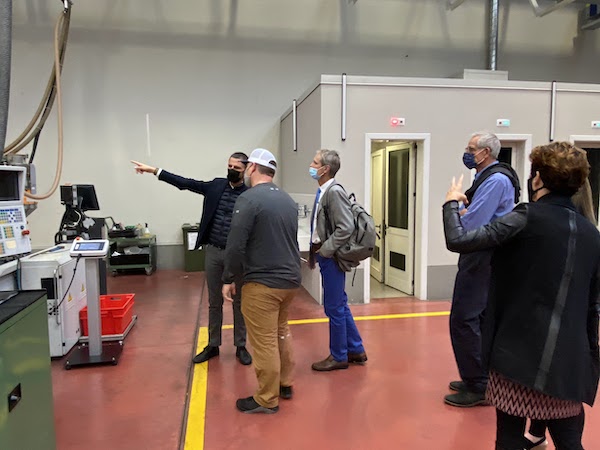
But then something powerful happened. “After staying home for two or three weeks, people wanted to come back to the company, which I never expected. Plenty of people were dedicated to the company, and it’s these employees that make up the soul and the environment of the company,” said Marco. Subsequently, Caleffi increased production in May, June and July of that year, running two shifts per day throughout the rest of the year.
“Especially now,” Marco said, “I feel proud of the choices we’ve made in the last decades in terms of business organization. Giovanni Monti is no doubt our key leader as he steadily positions and implements improvements year after year with his business resolution and experience as Managing Director for Caleffi. Giovanni is able to keep every process under control while mindfully planning actions with accuracy. It is an essential approach as we move beyond COVID.”
“The rumor I picked up during my visit,” said Aune, “was that people hired at Caleffi feel that they’ve been ‘welcomed to the last company they will ever want to work for’. Now that’s impressive.”
Rohr adds, “My wife, Ellen, accompanied us on the tour. She observed that when Marco walked into the factory, everyone stood a bit taller,” said Rohr. “The employees are proud of the company and they are proud of the work they do. I am proud of the company I work for and it’s nice to see the people here are too.”
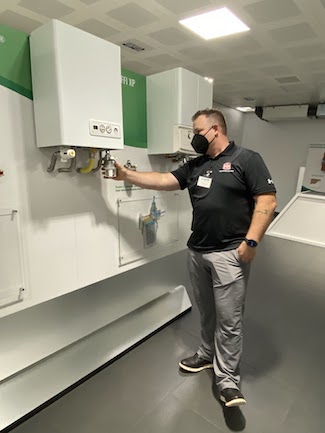
Eric admiring some components not yet available in North America used to filter incoming water on a Combi-boiler
Marco believes that success lies well beyond the company, “I think if you are involved in a company, you don’t only need to make money, you also need to create value in the company by making things better for the people and community. That was what my father believed in,” said Marco.
Currently, Caleffi has subsidiary locations in England, North America, Germany, France, Poland, Turkey, Netherlands, Portugal, Slovenia, Brazil and Australia. With these hubs, Caleffi S.p.A. sells its products in more than 90 countries. Caleffi is planning for more international growth and geographical expansion.
Says Marco, “We are currently planning an 80,000-square-meter warehouse expansion. My vision for the future is to see Caleffi in more countries with a much larger group of products to broaden the range of products we currently offer. Right now, our export business is expanding nicely and our branches are well staffed and managed. I see Caleffi continuing to extend its reach.”
I’m sure Francesco Caleffi would have been proud of the direction and leadership of his son, especially over these difficult past two years. Throughout the journey, the future looks bright for Caleffi.
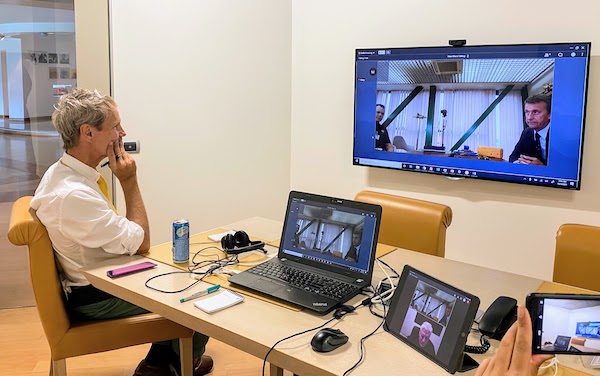
Behind the scenes, Mark Olson sits in on the “virtual” interview with Marco Caleffi by John Mesenbrink.
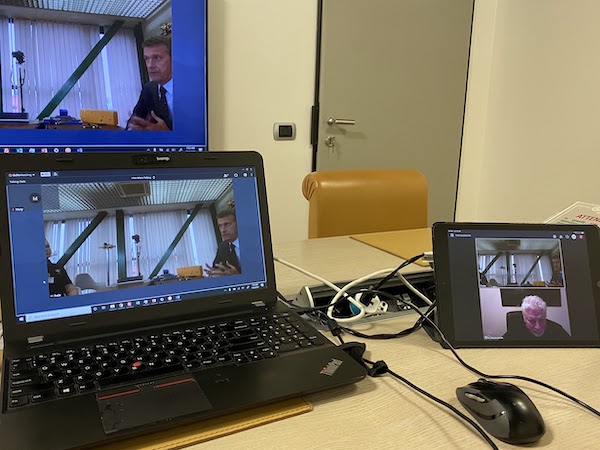
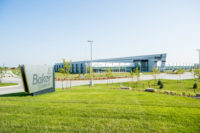
Conversations about the skilled labor shortage have become commonplace. And though high profile champions, like Mike Rowe, have given new visibility and importance to the looming challenge that threatens all trade professions nationwide, articles typically bemoan the lack of young people entering the trades while offering few solutions. The need for qualified technicians isn’t the Read more
Conversations about the skilled labor shortage have become commonplace. And though high profile champions, like Mike Rowe, have given new visibility and importance to the looming challenge that threatens all trade professions nationwide, articles typically bemoan the lack of young people entering the trades while offering few solutions.
The need for qualified technicians isn’t the only concern facing the trades, though. Others issues – such as quality of work and the time in which it’s completed – are as much a symptom of the first problem as they are challenges in their own right.
Many proactive, growing companies have squared off with the workforce shortage out of necessity, dealing it blows where they can. This often comes in the form of a bolstered recruiting game, or a train-your-own technician approach.
Local advocacy in high schools helps, too, though positive results come gradually as part of a longer-term effort. And, some companies implement systems and QC measures that help, to a degree at least.
If Baker Group, in Des Moines, IA, wasn’t already a mechanical force to be reckoned with over the past half century, this changed dramatically in early 2017.
Managers within the 650-person design-build firm, already intimately familiar with the advantages of prefabricating plumbing and mechanical systems offsite, made a bold move to expand their manufacturing space by nearly 150 percent. This, they say, has helped to solve several high-level concerns.

Baker Group is a 650-person, design-build mechanical firm in Des Moines, IA.
Manpower, quality, timeline
The decision to expand was made in order to produce higher quality products, in less time, without creating an unrealistic need for additional skilled manpower.
The firm’s new, 144,000 square-foot facility contains offices as well as manufacturing space, and is called Baker Group Advanced Manufacturing. As many as 75 craftsman can work during a single shift.
“We’ve done prefabrication work since the 1960s,” said Rob Cross, operations manager at Baker Group. “We added a large shop in 1998, and since then, we’ve steadily gained momentum. Our growth necessitated this new expansion last year.”
“The dynamic of the entire construction industry today is built on quality and speed,” says Tom Wengert, VP of Baker Group’s sheet metal business unit. “With this facility, we can prefab systems in a controlled environment, which improves quality while reducing labor costs.
“Additional benefits include increased safety, less congestion on construction sites, less jobsite trash and better scrap material recycling,” added Wengert.
While speed and quality are two major advantages to having a large manufacturing space at your disposal, the efficiency of off-site manufacturing means that fewer employees are needed to accomplish the same task.
Much of the in-shop sequencing implemented by Baker Group at the new facility was adapted from the automotive industry. For example, the flow of materials comes in west side of the shop and leave on the east side.
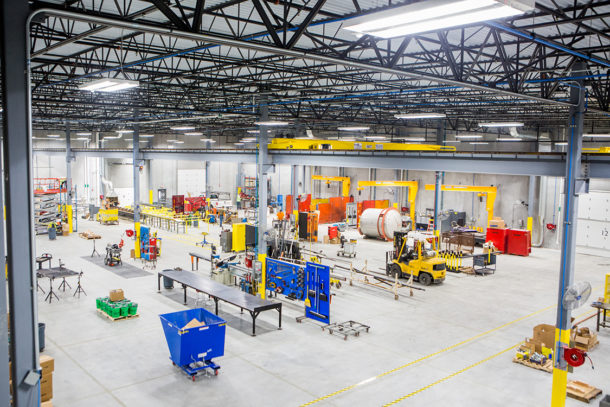
In 2017, Baker Group expanded their manufacturing space by 150 percent, or 144,000 square feet.
More than sheet metal
Completed in March of 2017, Baker Group Advanced Manufacturing includes 80,000 square-feet of fabrication space with almost 9,000 of that dedicated to multi-trade prefabrication alone.
The multi-trade space is located centrally among the sheet metal, piping and electrical shops. Here, trades work collaboratively in a weather-controlled environment to build to specifications and then ship to the job site.
The space features a 10-ton crane, allowing workers to construct large assemblies. By reducing on-jobsite time, this moves the entire construction timeline forward. The approach increases value to clients, and more than doubles Baker Group’s production capacity.
It’s in this centrally-located, multi-trade space that the various trades come together to assemble systems, sometimes even full mechanical penthouses. Welders work on framing and dunnage while pipefitters connect boilers, chillers, pumps and other equipment. Electricians wire the components and control technicians prepare everything to plug into a BAS.
“A good example of how we build to exact specifications in the shop can be seen in fabrication of gang restroom assemblies,” said Cross. “We can complete an eight-stall bathroom assembly in a little over a day, where it would take nearly a week onsite.”
Welders create an angle-iron framework, perfectly centering all the Watts closet carriers. Once assembled, the system is piped and hydro-tested. Waste water is also tested before the assembly is broken into several pieces for deliver to the job.

A Baker Group mechanic prefabricates large gang restroom assemblies at the new Advanced Manufacturing facility.
Baker Group has used the Watts back-to-back wall mounted, floor mounted and single closet carrier configurations for a wide variety of projects.
“We’ve standardized on the Watts carriers because the fab crews prefer them and they can be rapidly assembled,” said Cross. The Watts “industry standard closet carriers” come out of the box pre-assembled. The carriers feature a patented compression sealed nipple, which provides fast installation without the need for additional sealants. Adjustment is much easier than when threaded nipples are used.
“We never have any trouble with the closet carriers once they’re in the field, and the support we get from Jeff Howe, at Mack McClain & Associates – our manufacturer’s rep agency – is fantastic,” he continued
Cross has been with Baker Group for 23 years, and the relationship with rep firm Mack McClain goes back as long as he can remember. The firm supplies most of Baker Group’s plumbing components, including toilets, eyewash stations, backflow assemblies, drains and water heaters.
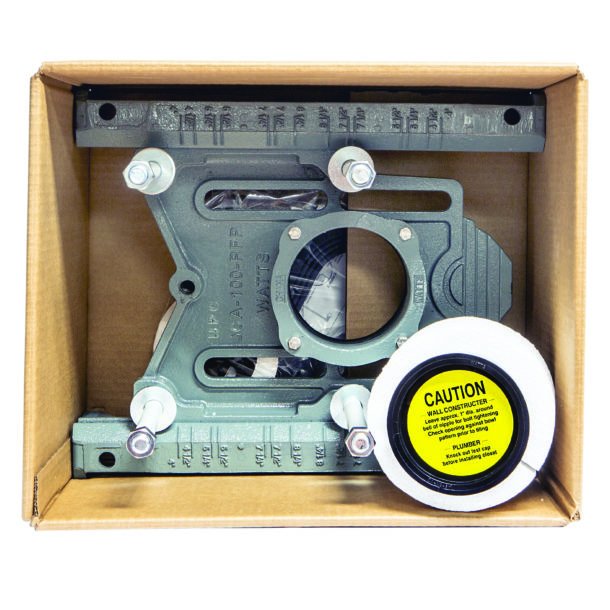
Baker Group has standardized on Watts closet carriers because the fab crews prefer them and they come out of the box pre-assembled.
Still adding capabilities
Toilet carriers aren’t the only plumbing systems that Baker Group prefabricates though. Like their ability to assemble boiler and chiller systems offsite, mechanics also build water service entrances, backflow assemblies, pump skids, pressure reducing stations and water purification systems. Once assembled, these items are broken down only as far as needed to be palletized, and the kits shipped to the jobsite.
“Every year we add something new to what we fabricate here on site,” Cross says, adding that Baker Group’s mechanical capabilities now include fabrication of ASME-rated vessels and components. “We’re equipped with the skills, knowledge, equipment and space to do this intricate and very strict code welding work.”
“Give us your biggest problem; the answer lies within the body of knowledge our people possess. We’ll find the solution,” he continued.

A premanufactured restroom assembly installed onsite.
Filling the new shop
While Baker Group Advanced Manufacturing allows the company to provide more capacity with reduced manpower, the need for new hires to fill the shop still requires ongoing effort.
“We’re a big local advocate for the trades,” said Cross. “We visit high schools and technical schools, invite people to take tours or do job shadowing programs. But we still can’t hire fast enough to fill the need.”
Baker Group is one of the largest, most capable design-build contractors in the Midwest, and they take that title seriously.
The content available on their website and YouTube channel speaks not only to potential clients, but also potential employees.
If the company’s dedication to recruiting parallels their insistence on delivering the best solution on time and on budget, staffing the new shop won’t be an unsurmountable task.
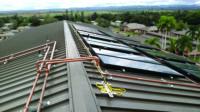
Viega fittings and solar thermal heating – it’s a combination that for AET Solar has proven to be a perfect match. AET Solar, one of the oldest solar manufacturers in the United States, worked on the largest solar thermal project in the country at the time in 2018. Viega played an integral part. The project Read more
Viega fittings and solar thermal heating – it’s a combination that for AET Solar has proven to be a perfect match.
AET Solar, one of the oldest solar manufacturers in the United States, worked on the largest solar thermal project in the country at the time in 2018. Viega played an integral part. The project was in Hawaii at the U.S. Army’s Schofield Barracks. AET installed solar water heaters to provide hot water for a portion of the barracks.
There are eight buildings with a total of 560 solar collectors and seven mechanical rooms with custom skid-mounted pumping stations. The installations were done exclusively with Viega ProPress, copper and stainless, and AET was pleased with its choice of Viega.
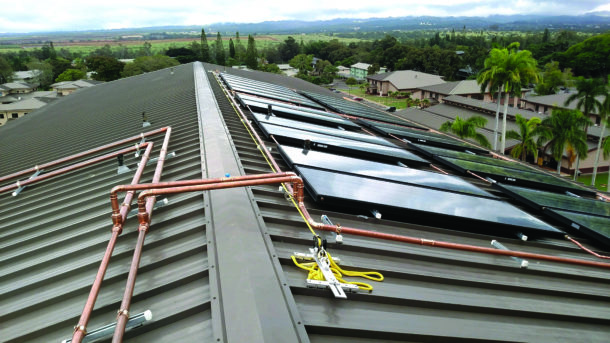
“For us, it has been phenomenal to use the Viega components,” said Carlos Fernandez-Aballi, Ph.D. and Engineer with AET. “It’s a natural fit between a press fitting and the huge challenge of collecting the energy that the sun provides. Using Viega reduced our installation time and cost significantly.”
AET’s Executive Vice President, Andrew East, was aware of Viega prior to the Schofield Barracks job, and the company was looking for a more secure and labor-savings connection for its collectors.
“There are two attractive things about Viega for us,” Dr. Fernandez-Aballi said. “Once you set it up, there’s a huge savings in labor – thousands and thousands of dollars in savings in labor on a project of this scale. For a big solar collection system like this, you need large flow rates, which means using large-diameter tubing. When you’re talking about sweating large-diameter tubes on the roof in the sun and the wind and everything else, it’s very cumbersome, so a press solution is the ideal way to go.”
Using solar energy for the barracks will provide the Army enormous financial savings. Dr. Fernandez-Aballi explained that solar thermal solutions can provide 70- to 100-percent of water heating, creating huge energy savings over a traditional system. Solar collectors are seven times more efficient than photovoltaic panels and are the most economical alternative to water heating. In a location the size of a military base, the savings are phenomenal.
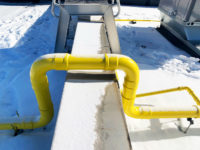
Who wouldn’t want to save nearly 500 man-hours on a project? That’s what CSM Mechanical did on a job for the City of Dearborn in Michigan – thanks to Viega’s MegaPressG fittings. By reworking plans to make the natural gas piping distribution system 4” or smaller on the police and courts buildings, and by choosing Read more
Who wouldn’t want to save nearly 500 man-hours on a project?
That’s what CSM Mechanical did on a job for the City of Dearborn in Michigan – thanks to Viega’s MegaPressG fittings. By reworking plans to make the natural gas piping distribution system 4” or smaller on the police and courts buildings, and by choosing to press instead of weld, the CSM Mechanical crew calculated a savings of 491 man-hours.
“The job just went in absolutely phenomenally,” said Craig Mortz, owner of CSM Mechanical. “We saved so much. We took an estimated 30-day project and finished it in 12 days!”
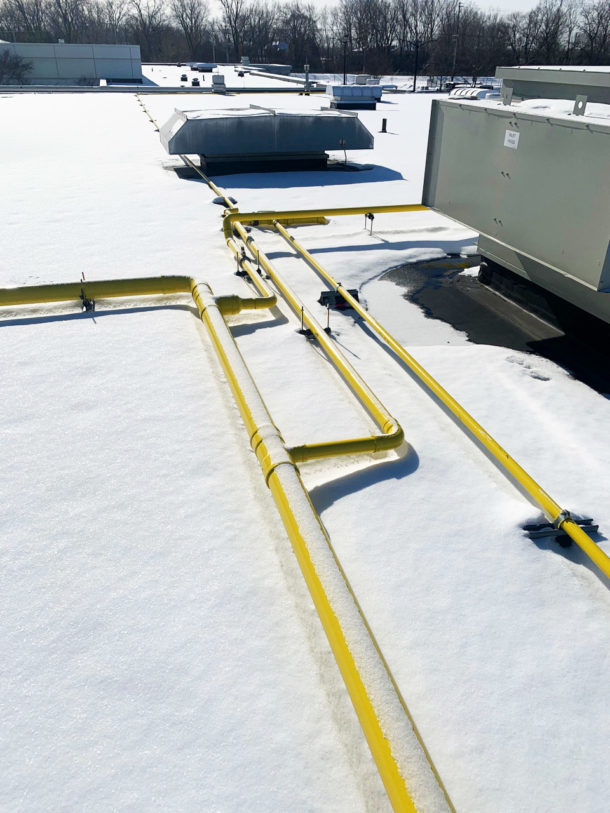
CSM Mechanical has been working for the past four years on an upgrade and update of the mechanical systems campus-wide for the City of Dearborn’s five municipal buildings. Originally constructed in the 1950s, the buildings all had one central powerhouse with heated and chilled water. The renovation plans included disconnecting the heating plant from the central source, upgrading the central chiller plant and giving each building its own individual boiler plant for improved efficiency and energy savings.
None of the buildings were plumbed for gas, and original plans for the police department building included a 6” gas main that was to be welded. Mortz and his team took a look at the project and knew they could improve on the design.
“In working with the owners and with Viega, we got concessions from the natural gas provider to increase the supply pressure so that we were able to get the system down to a 4” line,” he said. “We told the customer we could then also press it instead of welding, which would be faster, safer and save money.”
CSM Mechanical put in almost 1,000 feet of 4” gas pipe, using MegaPressG fittings. CSM Mechanical’s team was the first in Michigan to have the jaws and tool for the larger-diameter MegaPressG fittings, and they were excited to put them to work.
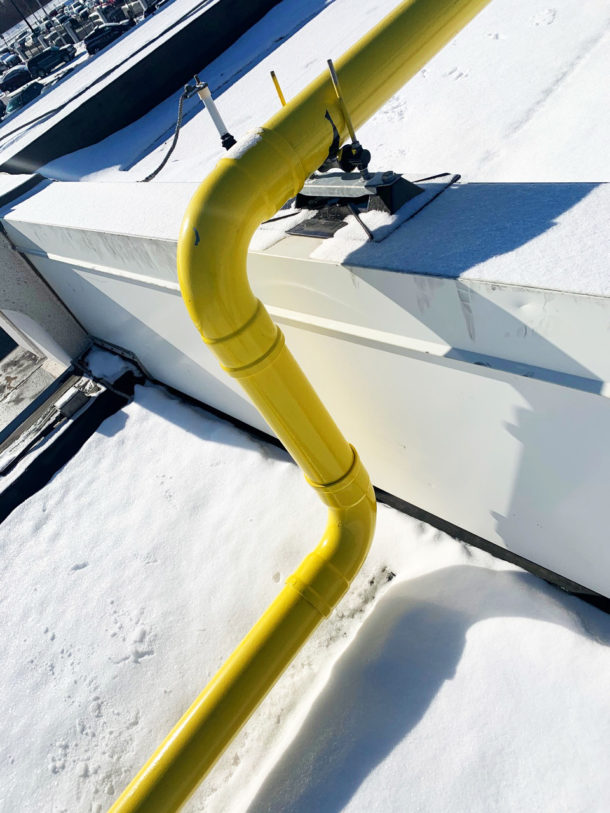
A four-man crew (instead of the six that would have been needed for welding), led by Field Operations Manager Tyler Pryzwara, completed the job. The workers put eight air handlers and four gas-fired boilers in the police and courts buildings, connecting everything with MegaPressG.
Specifications and assistance from Viega were vital in getting MegaPress – and the smaller-diameter pipe – approved for the project, Mortz said.
We showed the owners all the pressure test ratings and standards that MegaPressG is capable of,” Mortz explained. “When we increased the supply pressure and decreased the plumbing size to 4, we were well within any operational and conditional limits for this installation.
“Just the logistics of welding 6” carbon steel pipe and manually distributing it across the various building roofs is where our biggest time savings came from,” Mortz said. “As opposed to 4” pipe that is lighter and can be cut and prefabricated – that saved a lot of time.”
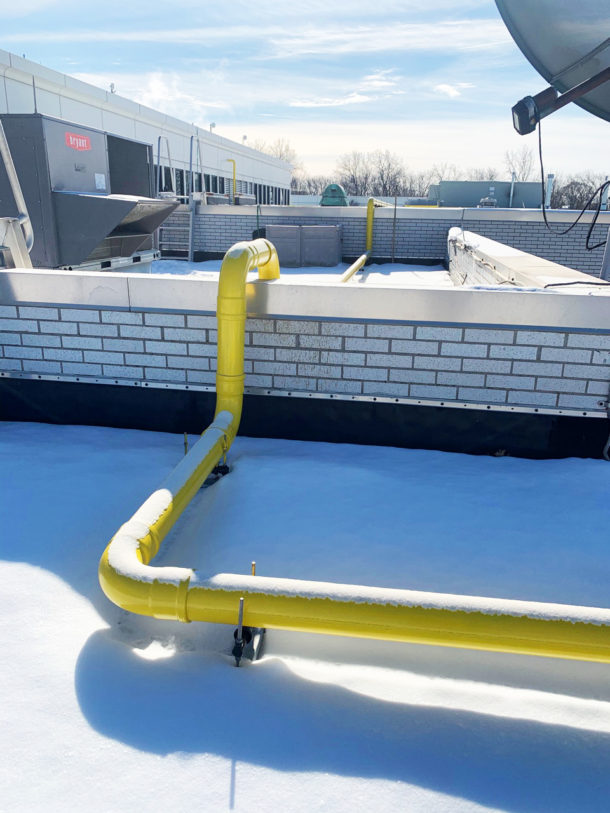
The safety aspect on this project was also a huge benefit. Because the police building is occupied and active 24 hours a day, welding posed significant safety and fire hazards since there were no “off hours” to do the work in. Plus, the buildings have a tar/pitch roofing system.
“We didn’t have to weld on the roof, so we didn’t have sparks and flames and fire blankets and all of the associated PPE,” Mortz said. “Safety was a huge win for us on that building and on the project overall.”
Once installed, CSM Mechanical pneumatically pressure tested the system, which included 1,811 mechanical joints, to 150 psi with no issues or leaks. As winter temperatures set in, the buildings were heated via the new boilers and natural gas line without a problem, providing the City of Dearborn with substantial energy savings and improved efficiencies.
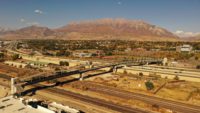
Spanning 305 feet across the I-15 freeway, the 17-foot-wide Utah Valley University Bridge soars up to 35 feet above ground and provides access to and from campus for up to 6,000 students a day. The structure includes a pedestrian path, bicycle lanes, and elevators to make it ADA-compliant, in addition to a radiant-heated deck to Read more
Spanning 305 feet across the I-15 freeway, the 17-foot-wide Utah Valley University Bridge soars up to 35 feet above ground and provides access to and from campus for up to 6,000 students a day. The structure includes a pedestrian path, bicycle lanes, and elevators to make it ADA-compliant, in addition to a radiant-heated deck to keep snow and ice off the walkway during the winter months.
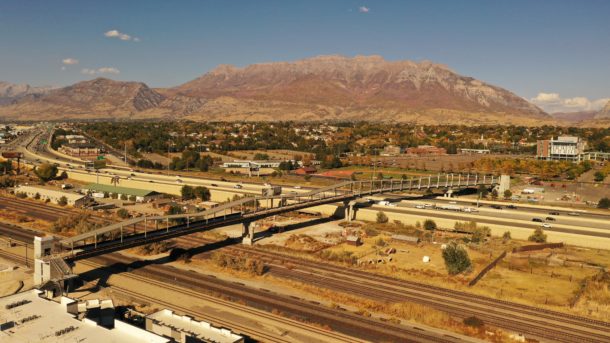
When the project first began, the university and the Utah Department of Transportation (UDOT) felt that a snow-melt system was imperative to ensure the safety of those crossing the bridge as well as those commuting underneath.
Aron Frailey of Thermal Engineering LLC recalls the day he first heard about the project. “My salesperson walked into my office and said, ‘How do you feel about quoting a snow-melt job for a thousand-foot bridge?’ Wow, I thought: A bridge? Can that even be done?”
Thermal Engineering began communicating with engineering firms, WSP and Kraemer, submitting load calculations based on the engineer’s initial design concepts. However, it took some time for the project to gain traction.
“Looking at the project in its initial stages on paper, it was difficult to see how we would do it,” says Frailey. “Even with 3D models, we struggled to understand how we would thread roughly 2,000 feet of pipe through all the girders of this bridge structure. There is a whole steel truss we had to work around and through, and I feared it could be a disaster from the standpoint of safety.”
Changing the spec
Part of the challenge was the structure’s height. Then there was the original specification, which called for 4″ steel pipe for the hydronic distribution piping. Because a standard length in that diameter weighs more than a ton, it would require numerous installers and a lot of welding.
So, Thermal Engineering began investigating — and eventually recommended — PP-RCT as a worthy alternative. A non-corrosive polymer would be better able to withstand the salt and magnesium chloride Utah uses for snow and ice melting on its highways. Even with the bridge more than 30 feet in the air, this was a major concern, because the hydronic piping would be installed in the structure’s underside, facing fast-moving traffic below.
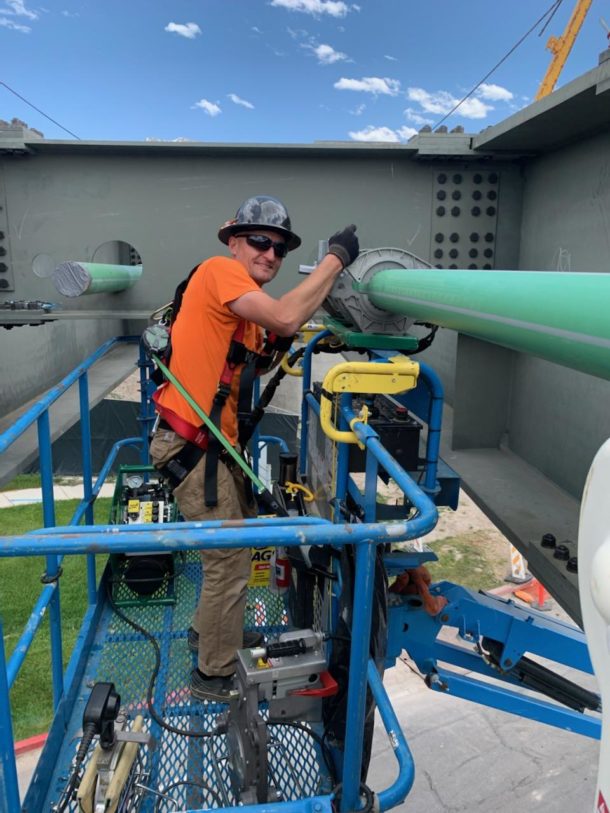
UVU Bridge in Orem, UT, Uponor PP-RCT install, Installed by Scott Layland with Thermal Engineering out of SLC, UT, photo by Stu Lorton
Moreover, PP-RCT would be far easier to handle and therefore less labor-intensive than steel. Shipped in 19-foot lengths, a stick of 4″ PP-RCT weighs a mere 63 pounds — a fraction of its steel counterpart. Plus, PP-RCT uses heat fusion for connections as opposed to welding with an open flame.
PP-RCT also offered one other critical advantage over steel: the ability to move in unison with the bridge. “The structure is intended to move as much as 18″ in every direction all the time — left to right, backwards and forwards, up and down,” says Frailey. “I was concerned about the joint integrity of a steel piping system with all that movement, and I really liked the flexibility of PP-RCT to handle it.”
For all these reasons, Thermal Engineering formally asked the engineer to change the specification to PP-RCT. After due consideration, the change was made.
“The engineer understandably had lots of questions,” says Frailey, who came to appreciate the “high level of trust” that flourished among his firm and Kraemer North America, WSP, and the rest of the build team.
“We sent samples and demonstrated how to make a heat-fusion connection,” he says. “We also cut some joints apart, so the engineer could confirm how completely the materials bonded. When we began reviewing the flow and weight characteristics, as well as the integrity of the joints and the ability to flex with the bridge, PP-RCT won the day.”
PP-RCT and PEX
The UVU project is the largest use of PP-RCT with 1,900 feet of 2½” to 4″ PP-RCT for supply-and-return piping, and it is also the first full-scale use of PP-RCT from Uponor North America. In addition to PP-RCT, the project also included 36,000 feet of ⅝” Wirsbo hePEX™, also from Uponor.
Frailey’s crew threaded the majority of the PP-RCT through the bridgeworks while it sat on the ground in the pre-fab steelyard, located roughly a mile and a half from the job site. Using a lift truck fitted with a winch for moving the pipe laterally, the team created a workstation for the McElroy Acrobat™ heat-fusion machine to connect the 19-foot lengths of PP-RCT.
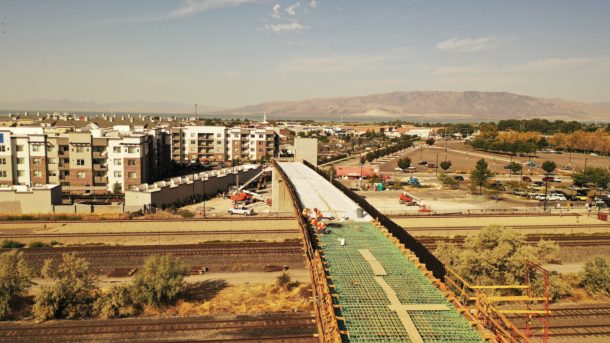
Although the heat-fusion process normally requires only two fitters, according to Frailey, “we needed a three-man team for this job” to reach the underside of the bridge. The first pipefitter’s task was to maneuver the 19-foot piece of PP-RCT off the ground and up into the bridge’s girder diaphragms.
Project superintendent Scot Layland was in an airborne workstation, hooking each length of pipe to the fusion machine and butt-fusing it to another length ahead of it in the line. Meanwhile, a third person operated the boom truck and the winch, pulling the pipe assembly through the bridge.
“Our men ran a rope through the girders and attached it to the pipe, pulling it through the girders while working on opposite ends of the bridge, rather than right over the highway,” says Frailey. Because of the PP-RCT’s weight, “the crane pulled the pipe easily — no big deal,” he says.
After the challenges of the hydronic piping, the PEX portion of the snow-melt job was smooth and easy. “For us, PEX for snow-melt systems is a known entity and installed without any problems,” he says.
Once the project was complete, Frailey was pleased with the results. “PP-RCT is an awesome product — the flow characteristics of the pipe, its light weight and flexibility, the ease of lifting and maneuvering it — all these benefits are huge compared with steel. In fact, we’re already using it on other projects.”
To learn more about Uponor PP-RCT, visit www.uponor-usa.com/pprct.