The two new products are part of ADEY’s Best Practice® approach to prolonging the life and efficiency of hydronic heating systems. ADEY, a U.K- based company whose pioneering MagnaClean CMX® range was recently rolled out in the United States and Canada, is introducing a line of innovative, concentrated system treatment formulas, designed to clean and protect Read more
ADEY
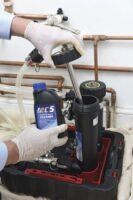
The two new products are part of ADEY’s Best Practice® approach to prolonging the life and efficiency of hydronic heating systems.
ADEY, a U.K- based company whose pioneering MagnaClean CMX® range was recently rolled out in the United States and Canada, is introducing a line of innovative, concentrated system treatment formulas, designed to clean and protect older hydronic heating systems and retrofit installs. MC5™ Cleaner and MC40+™ De-scaler serve different purposes, but both were created to combat a frequently overlooked enemy of untreated hydronic heating systems – black sludge.
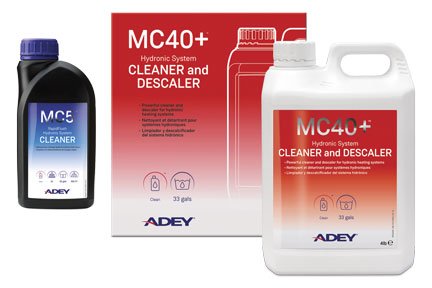
The MC40+ Hydronic Heating System Cleaner & De-scaler is a high-strength powdered chemical, specially designed to restore existing boiler systems by removing lime-scale deposits, calcium and magnetite. Rapid-performing MC40+ delivers an advanced clean, with a highly concentrated formula, in as little as one hour. It even comes with neutralizer packets to provide extra peace of mind if there is concern over residues being left in the system.
The second, MC5 Hydronic RAPIDFLUSH System Cleaner, is a high-performance, advanced-strength product, designed to work with ADEY’s award-winning MagnaCleanse® flushing unit. Together, they effectively remove sludge, debris, and scale while delivering exceptional cleaning results quickly.
Key features summary
MC40+:
- Specifically designed to remove heavy lime-scale and calcium deposits from older systems with known water-quality issues or plugged components, such as heat exchangers.
- Preferred option to clean and drain the system quickly.
- Faster-acting, with a working time range of one to four hours.
- Residential only – treats 33 gallons.
MC5:
- Designed for flushing; works best with ADEY’s MagnaCleanse flushing unit.
- Faster-acting than the MC3+® but provides more time than the MC40+. Whether old or new, if the system is to be flushed on the same day that it is cleaned, this is the preferred cleaner option.
- Working time range: from a minimum of 1 hour to a maximum of 7 days.
- Residential size only, treating 26 gallons.
For more information on the ADEY Treatment Formulas, please visit: https://www.adey.com/us.
For more information on the full line of ADEY filters and other Best Practice System Process solutions, visit adey.com/us. You can also phone +1 412 406 8292 or e-mail info@adeyusa.com.
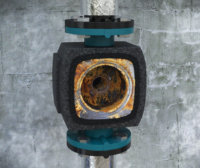
Demineralizing water will prevent corrosion from occurring in a hydronic system, right? Wrong By demineralizing, we mean removing the ions from the water until it is purified and has zero conductivity. In theory, this sounds ideal for the system however, where there’s oxygen; there’s corrosion! Regardless of how purified the water is, oxidation of the Read more
Demineralizing water will prevent corrosion from occurring in a hydronic system, right?
Wrong
By demineralizing, we mean removing the ions from the water until it is purified and has zero conductivity. In theory, this sounds ideal for the system however, where there’s oxygen; there’s corrosion!
Regardless of how purified the water is, oxidation of the water will start the process of corrosion. Keeping water purified requires 0.1 PPM or less of oxygen in it, which is A. pretty much impossible, even in a closed loop system, and B. is hard to measure.
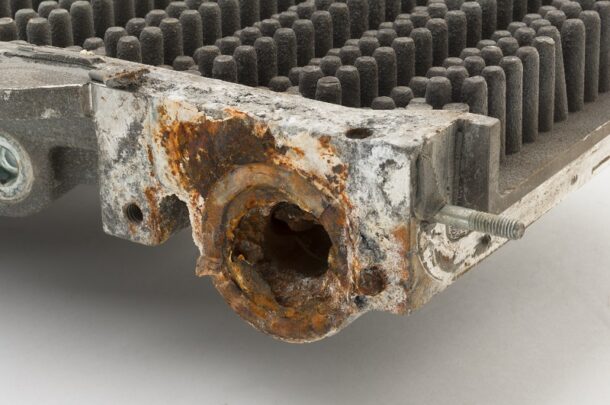
How does oxygen enter a closed loop hydronic system?
Oxygen can enter a system, old or new, in multitude of ways. Membranes, rubbers, joints, and faulty AAV’s can suck oxygen into the water. Not forgetting that most boilers now have auto-fill valves, and as soon as new water is introduced to a new system, so is oxygen.
All new components are exposed to oxygen and other contaminants during the manufacturing, transportation, and storage process. Fluxes can build up on the inside of components such as pipework during installation, and air pockets are very common when filling a new system. All of these factors lead to an introduction of oxygen in the system, and that’s when the process of corrosion begins. Remember – corrosion is a natural process that cannot be completely stopped, but it can be prevented in new systems and significantly slowed down in existing systems.
How does oxygen in a system cause corrosion, and what affect can it have on the system?
As oxygen enters a system and mixes with the dissimilar metals and the water, it oxidizes which leads to an increase in iron levels. Oxygen can also bring ions into the water, therefore increasing conductivity, causing further corrosion.
This process can also lead to magnetite build up, which is insoluble iron and is the number one cause of hydronic heating system issues such as faulty thermostats and controls, fouled EMCs, worn pump seals, heat exchanger failures, pipework pin-holes, and system blockages.
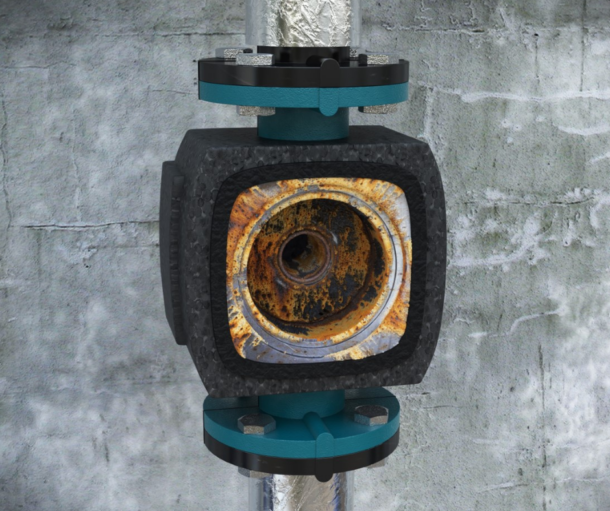
So, if purifying the water isn’t the solution, what is?
The ideal solution is to test, clean, protect and maintain the system. This controls pH, the oxygen, and the alkalinity of the water, preventing reactions and corrosion to occur.
Test
The first step to diagnosing the root cause of systems issues or preventing any damage/failures from occurring in new systems is to test the quality of the water. ADEY’s corrosion, pH, and inhibitor will identify whether corrosion has built up, or is building in the system, and provides recommendations on how to restore/treat the system water.
Will a TDS test not identify this?
Testing for TDS (total dissolved solids) tests for everything dissolved in the water which includes iron, copper, chlorides, nitrates, and sulfates. Even cleaner residues, flux residues, and the addition of inhibitor can increase TDS and conductivity, so the answer is no, testing for TDS should not be used to test for corrosion in a system. Testing for TDS should also not be used to identify water hardness. Calcium and magnesium salts cause hardness, but TDS is for all dissolved solids rather than just calcium and magnesium salts specifically, so this is not a true indication of hardness levels in a system. A specific hardness test should be used to test for hard or soft water.
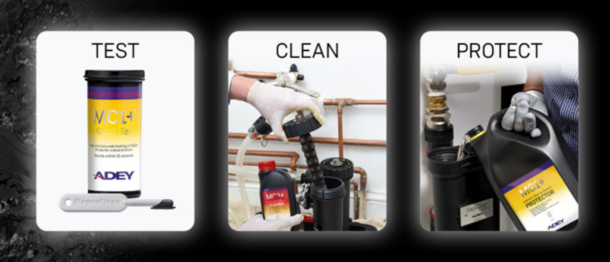
Clean
On any system, it is key to have an air eliminator. An air and dirt separator should be installed on the supply side of the system to aid air removal. On an existing system, first try bleeding any radiators, upgrade failing parts, fix any leaks, and fully cleanse the system a cleaner such as ADEY’s MC3+® cleaner. The cleaner will lift and hold any existing magnetite, scale, and sediment in suspension, ready for it to be flushed out of the system. Similar to cleaning dishes with washing up liquid, adding heat will also aid the clean, so circulating the cleaner around the system while the system is on will increase the effectiveness of the clean.
Protect
For protection, a combination of a magnetic filter such as the MagnaClean® should be installed, and inhibitor such as ADEY’s MC1+® protector should be dosed into the system. Magnetic filters should be installed on the return just before the heat exchanger or boiler to prevent any magnetite from entering this most expensive component. It is also key to choose a filter with a larger magnet directly in the flow of water to aid capture, and of course, one that is easy-to-service.
This 3-step solution is the only way to truly prevent the buildup of magnetite and the costly problems it can cause.
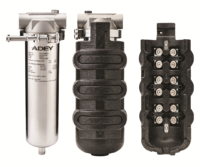
Adey’s new MagnaClean CMX range of filters provides adaptive magnetic and non-magnetic side-stream filtration for closed-loop heating and chiller applications As plumbing, HVAC and mechanical contractors become all too familiar with the extended costs of maintaining commercial hydronic heating components or system life, the need for a solution has been growing. Adey® answered that need Read more
Adey’s new MagnaClean CMX range of filters provides adaptive magnetic and non-magnetic side-stream filtration for closed-loop heating and chiller applications
As plumbing, HVAC and mechanical contractors become all too familiar with the extended costs of maintaining commercial hydronic heating components or system life, the need for a solution has been growing. Adey® answered that need with the introduction of the MagnaClean CMX™ range to the North American market in May 2022.
This easy-to-service range of filters not only protects system equipment — heat pumps, boilers, pipework, and sensors/controls — but also reduces maintenance costs and hours, improves heat transfer, heat output and efficiency, saves energy, lower clients’ utility bills, and reduces carbon emissions.
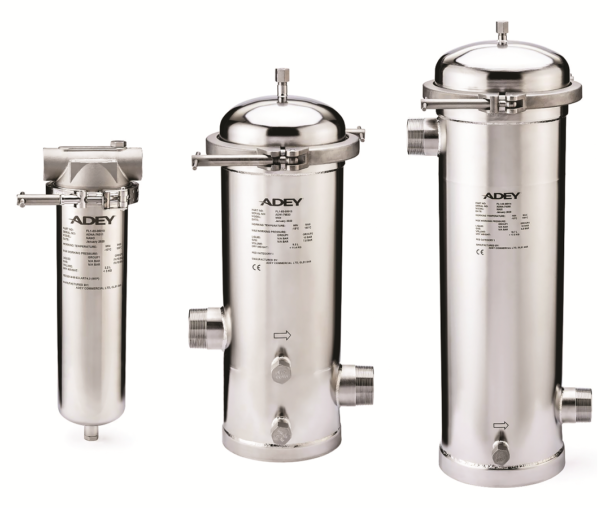
Why wait for system issues to arise?
The MagnaClean CMX range is the latest innovative extension of Adey’s market-leading MagnaClean® range of filters, offering a new and unique way of capturing both magnetic and non-magnetic debris by combining powerful neodymium magnets with a range of high quality, 5-50 micron spun-bonded filter cartridges, and needle-felt bag filters.
These cartridge-and-bag filters also act as passive deaerators, encouraging the release of dissolved air and gases from the system water, which can then be vented via the automatic air vent that is included with each of the three side-stream filters within the range: the MagnaClean CMX Nano™, Midi and Maxi.
Side-stream installation helps reduce installation time, complexity, and costs, with no need to partially or fully drain a system or cut into and weld pipework and flanges. Pipework connections can also be downsized, offering further cost-effective installation options. Existing side-stream pipework connections can also be used, meaning an existing pot feeder can be easily replaced by a CMX filter.
The MagnaClean CMX range can also be serviced with minimal system downtime or flushing, meaning minimal water and heat loss during system maintenance. This makes the range ideal for a wide range of commercial and industrial applications such as manufacturing plants, sports facilities, hospitals, schools, etc. The Midi and Maxi sizes also act as pot feeders, making chemical dosing /water treatment management effortless.
Quality construction, easy installation
Adey has honored its roots by working to maximize the quality with this new filter range, constructed from 316L stainless steel with EPDM seals. Compact and lightweight, with self-supporting and floor-standing options, tool-free servicing, and removable magnet assemblies, the MagnaClean CMX range is easy to install and service.
The innovative CMX Nano External Magnetic Jacket and CMX Nano filter combine to help accelerate the removal of highly damaging magnetite debris from heated-water and chilled-water systems, creating what is possibly the most compact, yet powerful commercial system-filter combination available today.
The innovative MagnaClean CMX range is a highly efficient and flexible product solution that delivers formidable dual-filtration performance, direct chemical dosing capability, and improved system efficiencies and protection, helping to reduce maintenance costs, energy usage, and carbon emissions.
- For more information on the Adey MagnaClean CMX Filter, please visit: https://www.adey.com/us/cmx
- For more information on the full line of Adey filters and other Best Practice System Process solutions, visit www.adey.com/us/. You can also telephone us at +1 412 406 8292 or e-mail us at info@adeyusa.com.
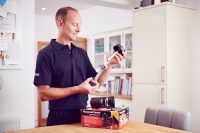
What is corrosion? We’ve all seen it and talked about it at some point, right? So, how well do we really understand it? It is important to understand that corrosion is a natural process, and it will occur in every system where any type of metal is present. From pipes and fittings to major components Read more
What is corrosion?
We’ve all seen it and talked about it at some point, right? So, how well do we really understand it?
It is important to understand that corrosion is a natural process, and it will occur in every system where any type of metal is present. From pipes and fittings to major components, corrosion is part of a natural process for any metal that has been refined and then formed into a manufactured component.
Once formed, the clock begins! These metal parts and pieces are actively working on returning to their natural form, into a more stable state such as an oxide. This is how we end up with black iron oxide, or magnetite as one result of this natural process.
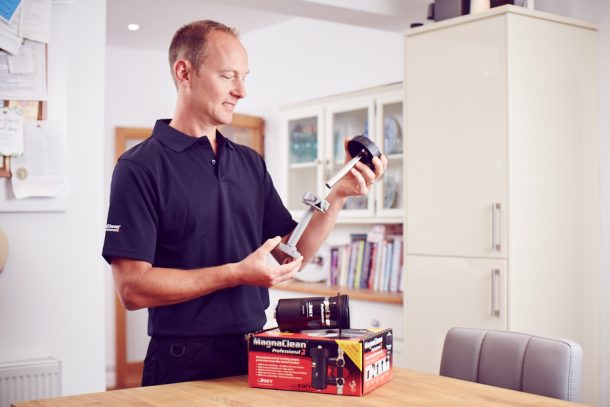
How does this apply to hydronic systems?
While there are many causes and contributing factors to corrosion, the biggest concern for any hydronic system is the risk of blockage. Blockages can not only dramatically reduce the efficiency of your system, they can prematurely shorten the functional life of your major components.
Knowledge is power, and a little extra effort now can yield years of higher efficiency and longer life for your systems’ components. Another important concept to realize, particularly in hydronic heating systems, is that heat accelerates the process of corrosion. That’s right, a hydronic heating system by its very nature is a catalyst for corrosion!
Black iron oxide or magnetite is often recognized as black water, black sludge, mud, dirt, or metal flakes in the water.
Counteract Corrosion
We can prevent corrosion from occurring in a new system, and we can even slow down the process in an existing system via three simple steps: Test, Clean, Protect.
Test
Testing is a vital step in understanding the quality of the water in the system. A test identifies whether corrosion is occurring, and also advises on what needs to be done to recover the system water and components. Read more about our water testing tools here.
Clean
Any system with corrosion occurring will need a clean. Our MC3+ cleaner is a neutral based cleaner, designed to lift and dislodge scale and iron oxide that has built up on system components and pipework. This cleaner also contains a small amount of inhibitor that will protect the components as it’s cleaning. For more information on our MC3+ cleaner, click here.
Flushing the system is also required after cleaning, and this can be done using our MagnaCleanse flushing machine. The unit works as a by-pass, allowing the system to be cleaned with no system shutdown; this also means that the system water remains hot, providing a better clean. Find out more about this money-making machine here.
Protect
Unfortunately the process of corrosion never stops, which is why any hydronic system will need the long-lasting, continuous protection of a magnetic filer. Our MagnaClean filters collect the iron oxide that has been loosened by the cleaner, and will continuously collect any future iron oxide to provide on-going protection for the system and its components. MagnaClean filters are available in a wide range of residential and commercial sizes for any type of hydronic system, whether it be a boiler, chilled water, or steam system.
Inhibitors are also vital in ensuring the on-going protection of the system. Our MC1+ protector provides a protective coating on all system components to prevent future corrosion from building up, and also contain pH buffering agents to neutralize pH levels which will prevent future acidic or alkaline corrosion. More information about our MC1+ protector can be found here.
Counteract corrosion: TEST. CLEAN. PROTECT.
Warning: Chemicals should not be used in steam systems due to higher temperatures. Magnetic filters can be used for steam system protection. For more information, please visit https://www.adey.com/us/corrosion
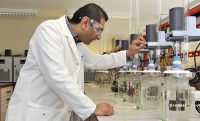
Does propylene glycol protect a system? Firstly, before adding any propylene glycol to a system, you should understand the design life of it. Often, the less expensive propylene glycol holds a shorter design life of 3–5 years, whereas the premium propylene glycol holds a design life of roughly up to 15 years. As propylene glycol Read more
Does propylene glycol protect a system?
Firstly, before adding any propylene glycol to a system, you should understand the design life of it. Often, the less expensive propylene glycol holds a shorter design life of 3–5 years, whereas the premium propylene glycol holds a design life of roughly up to 15 years.
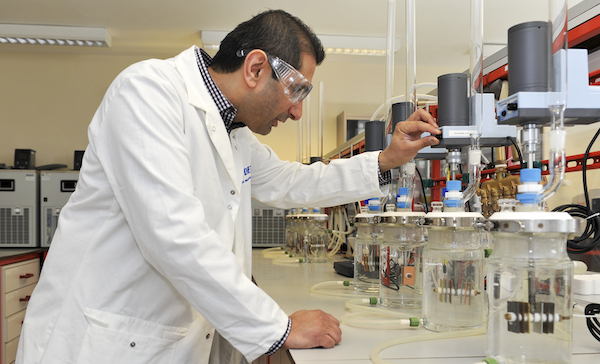
As propylene glycol begins to degrade, it becomes acidic, which as you can imagine has a major impact on key components within the system—attacking metal surfaces such as iron pipework, pumps and heat exchangers, which is why the design life of glycol needs to be seriously considered. A premium glycol contains a higher quality inhibitor which acts as a buffer to keep the system’s water pH idyllic, but the system should be checked on a regular basis anyway—the ideal level is 8 – 8.5. Once system pH goes below 6.5, inhibitor with buffering agents will need to be added to elevate the pH levels.
How much glycol should I add to the system?
Boiler manufacturers often advise that glycol should make up no more than 50% of the system’s volume, with some HE boiler applications being reduced to 35%.
Can system efficiency be affected if too much glycol is added?
Yes, glycol has a higher viscosity than water—too much of it can reduce the effectiveness of water flowing through pipework, and too much glycol can also reduce heat transfer capabilities. Both of these aspects together can have a serious impact on heating components such as pumps and heat exchangers, causing them to work harder to maintain system temperature and flow, so much so that it can lead to over-heating and eventually, failure. This is why many boiler manufacturers have warning limitations on the amount of glycol used, because too much can damage components and even result in boiler breakdowns.
Do I need a cleaner and dirt filter if the system has already got pre-mix glycol?
Yes. Pre-mix glycol is not designed to lift and capture magnetite—it’s designed to prevent system water from freezing during cold winter months, and the inhibitors in glycol are used as a buffer to prevent acidity levels from rising.
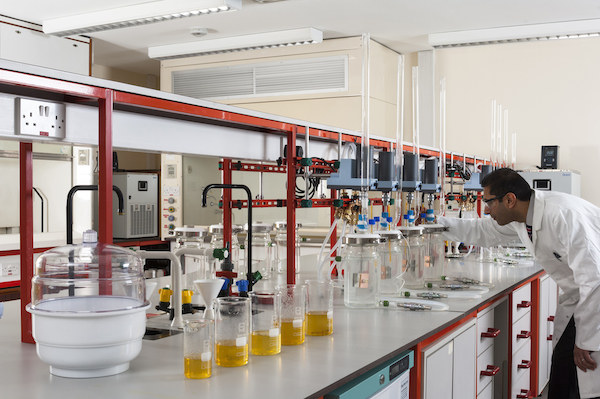
Magnetite, also known as black iron oxide sludge is formed as a result of air oxidizing inside an untreated system. Unfortunately, a pre-mix glycol does not mean that a system has been sufficiently treated, and here’s why:
A cleaner contains surfactants and dispersants that surround the magnetic particles, bonding them until they become dislodged from surfaces such as metal pipework. Of course, the longer a cleaner is left in the system, the more time it has to bond and dislodge debris, but you should always check the label for time-frames because cleaners can also become acidic when left in a system for too long
- A system flush allows the dislodged particles and cleaner to be removed from the system, but this is not where treatment should stop
- A magnetic dirt filter provides long-term protection. Just because the system has been cleaned and flushed once, doesn’t mean that magnetite isn’t going to return. The filter continuously collects magnetic dirt particles, preventing them from circulating through vital narrow waterways and blocking valuable system components such as pumps and heat exchangers
- An inhibitor forms a protective layer on surfaces such as pipework, but this is not the only benefit of an inhibitor. Some inhibitors are specifically designed to counteract residue cleaner left in the system, even after flushing, ensuring that the system water remains pH neutral
- Finally, testing and maintenance ensures that elements such as chloride, copper, iron, water hardness and pH are not affecting the longevity and efficiency of the heating system. These checks should be carried out on an annual basis for residential systems, and more frequently for commercial/industrial systems.
Andrew Lapinsky, Senior Sales Manager and Water Treatment Specialist, ADEY.