Viega plans to invest over $70 million in the next two years as part of its long-term strategy to expand U.S. manufacturing and support the needs of its North American customers. Broomfield, Colo. — Viega announced plans to expand its production capacity in McPherson, Kansas. The first wave of these investments is approximately $14 million Read more
PVF
Viega plans to invest over $70 million in the next two years as part of its long-term strategy to expand U.S. manufacturing and support the needs of its North American customers.
Broomfield, Colo. — Viega announced plans to expand its production capacity in McPherson, Kansas. The first wave of these investments is approximately $14 million and will increase the U.S. production of its industry-leading ProPress® products.
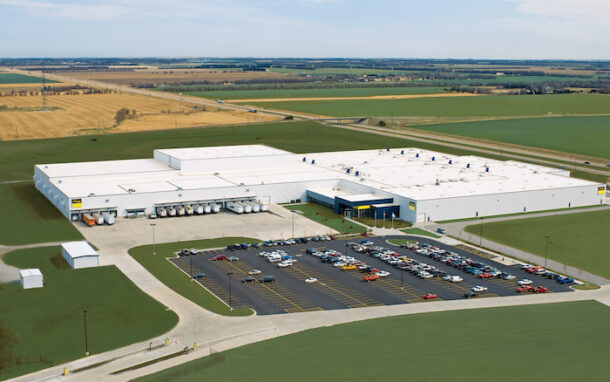
“As we continue to grow the business, we are bringing more production to the United States,” said Markus Brettschneider, CEO and President of Viega LLC. “These investments in our U.S. footprint will further support demand and leverage the talented U.S. manufacturing workforce, starting with the expansion of production capacity in Kansas.”
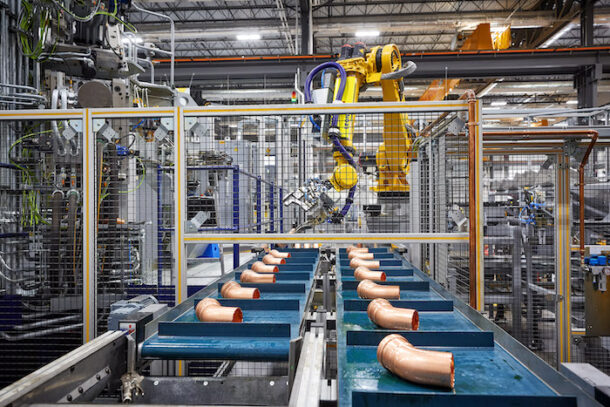
The McPherson manufacturing and distribution center is currently around 1 million sq. ft, with the facility more than doubling its footprint and workforce since opening in 2008. The new ProPress equipment is expected to be in production by the end of Q3 2023, with additional investments to come.
“We are proud to produce our fittings right here in Kansas. As we increase our U.S.-made products, we remain committed to creating highly skilled jobs in America, building out more sustainable manufacturing processes, and developing tomorrow’s workforce,” said Marki Huston, Head of Manufacturing for Viega LLC.
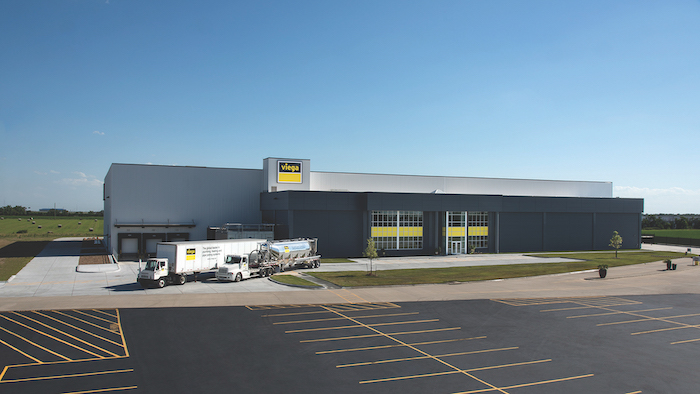
In addition to its McPherson, Kansas facility, Viega supports its customers and partners through distribution centers in Reno, Nev. and Carlisle, Penn., with further North American expansion planned for 2024 and 2025.
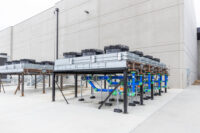
Businesses that entrust their data storage to the state-of-the art Novva data center outside of Salt Lake City will benefit from a location chosen for its many data center-friendly attributes. The area offers outstanding connectivity, low power costs, and a central-western site with easy access to a major international airport. In addition, the site’s climate Read more
Businesses that entrust their data storage to the state-of-the art Novva data center outside of Salt Lake City will benefit from a location chosen for its many data center-friendly attributes. The area offers outstanding connectivity, low power costs, and a central-western site with easy access to a major international airport. In addition, the site’s climate and 5,000-ft. altitude allow for many hours of free cooling annually.
Just as important to Novva’s clients, the new data center has a low disaster risk. The area is not prone to earthquakes, floods, or adverse weather events such as hurricanes.

And finally, for the additional peace-of-mind that makes this data center truly start-of-the-art, the cooling system for the computer servers boasts Aquatherm PP-RCT piping that will provide virtually leak-free service for decades to come. The Aquatherm piping will never scale or corrode, and the cooling water flow will remain unchanged throughout the anticipated 50-year lifespan of the pipe. All of this data adds up to a win for Novva and its clients.
The “hyperscale” data center in Salt Lake City will be Novva’s flagship data center. The 100-acre Utah campus is planned to ultimately include more than 1.5 million square feet of data center space and will accommodate 250kW to 30 MW clients. The construction is taking place in four phases. The first phase, which includes a 300,000-sq.-ft. data center, a 120MW substation and an 80,000-sq.-ft. headquarters office building for Novva, was completed in December 2021.
Beating the Heat
Reliable cooling systems are an essential component of modern data centers. Computer servers are notorious for generating heat—and heat is notorious for being an enemy of computer servers.
The decision to install Aquatherm pipe as part of the new data center’s cooling system was driven by Steven Boyce, vice-president of infrastructure and design at Novva Data Centers. Boyce has been involved in the IT and data center space for more than 20 years, and has worked on multiple successful startups during that time.
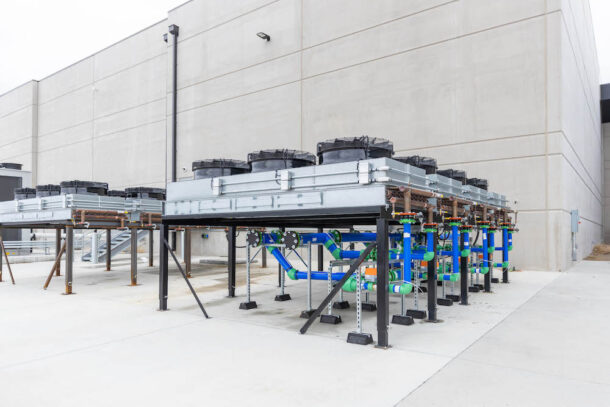
When I first learned about Aquatherm, it was a no-brainer,” Boyce said. “I had been using steel pipes in my builds, which would corrode and rust, and in turn, fill my equipment with sediment and pieces of rust. Efficiencies would be diminished, and the pipes would eventually have to be replaced. Aquatherm’s total installed costs are lower, and their warranty is something that no steel vendor could match.”
Once the decision was made to trust the cooling system’s performance to Aquatherm pipe, Novva turned to the Salt Lake City branch of Harris Mechanical for the installation.
Harris had experience installing Aquatherm pipe, although the Novva data center represented the company’s largest data center Aquatherm installation to date. To handle the first phase of the Novva system, Harris installed a BASX custom chiller package (which included the pumps and controls), the Aquatherm pipe for computer system cooling, and the comfort system piping and plumbing. The piping work for phase 1 began in mid-May 2021 and was completed in October 2021. The system was commissioned and turned over to the owner in December 2021.
Fast and Furious
Jeff Reading, operations manager, construction, Harris Mechanical, explained that the Novva data center started out as a core and shell project, with the office built first and the data hall scheduled to be built out later. However, as anyone in construction work knows, it’s always best to expect the unexpected.
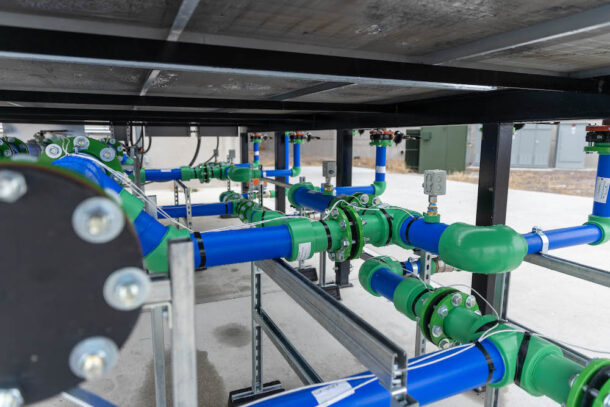
“We finished the core and shell construction in May 2021, and the data hall was right on its heels as a change order to the original project. So it came at us fast and furious,” Reading said. “The original plan was to complete the entire chilled water loop, which runs underneath the floor on both sides of the building. However, it was decided to install the piping in stages as the facility is built out. So far we have installed about half of the piping that will ultimately go in there.”
The installation to date has included 4,418 ft of Aquatherm Blue Pipe SDR 17.6. The main system piping is 10-in., and the takeoffs are 4-in.
Training Professionals
To handle such a large project. Harris Mechanical sent several installers to Aquatherm’s U.S. headquarters in nearby Lindon, UT, for training.
Having Aquatherm-trained technicians opens up new opportunities for HVAC and plumbing companies. The company gains differentiation in the market, and enjoys the time- and labor-savings associated with installing polypropylene pipe.
Aquatherm training is the most intensive, comprehensive training in the polypropylene piping industry. Attendees receive both classroom training and hands-on training with multiple fusion machines, and must pass a rigorous test using all the fusion tools correctly.
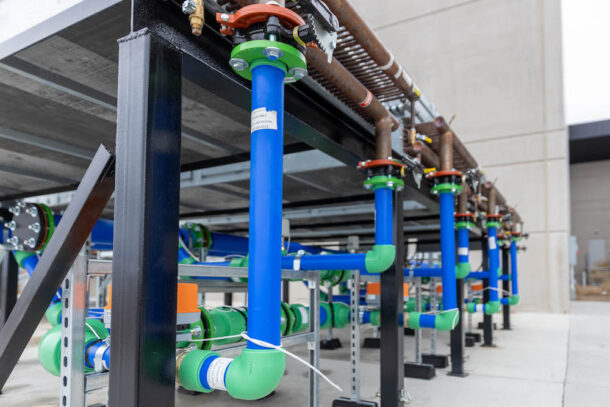
After the training, Harris completed the installation using McElroy fusion tools and a combination of socket fusion for the 4-in. pipe and butt fusion for the 10-in. pipe. The system runs at a low pressure (35 to 45 psi); the cooling system supply water runs at 55°F and returns to the chiller at about 60°F.
According to Reading, Harris Mechanical had a good experience with Aquatherm piping at the Novva data center, and the ease of installation compared to steel pipe helped Harris stay ahead of the project’s tight schedule.
“It was a smooth process,” he said. “We definitely gained experience and confidence with the pipe throughout the project, and our installers became accustomed to ‘leapfrogging’ and working with more than one [fusion] machine at a time.”
A Smooth Path
The underfloor piping system presented one of the major installation challenges at this project. The floor is raised 5-ft., and all of the facility’s piping, wiring, HVAC ducting, and utilities run through the raised space.
Aquatherm’s building information modeling (BIM) capabilities and Scan-to-Fab service helped ensure that the installation went smoothly by preventing underfloor conflicts and collisions.
“Using 3D BIM and Revit really helped with coordinating this installation,” said Autumn Turner, a fabrication drafter at Aquatherm. “Not only was all the HVAC and plumbing under the floor, there were floor stands every square foot. It took a lot of coordination to avoid all those potential obstacles.”
Turner noted that careful coordination enhanced the already-fast heat-fusion installation of Aquatherm pipe, and that less time and money spent on welders is a major benefit of choosing Aquatherm.
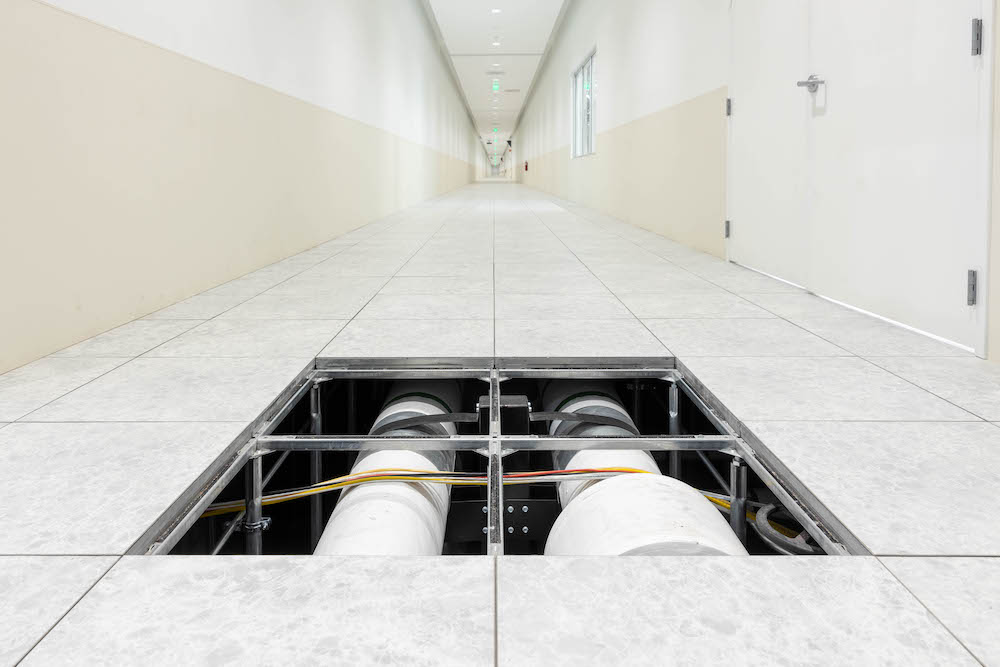
“Aquatherm is just easier work with than steel pipe,” she said. “It takes a lot less time to weld, and when you add in the BIM support and drafting it was easier for the installers to get situated into the floor and navigate the space.”
Turner added that Aquatherm’s BIM and Revit capabilities will ensure the future installation phases of the massive project also go smoothly.
Rhett Coles, Aquatherm’s fabrication drafting/scan-to-fab manager, said that Aquatherm’s Scan-to-Fab service and in-house fabrication makes any piping installation easier and smoother. Spools can be custom made in any size or configuration and shipped to the jobsite ready to install. In addition, any pieces fabricated by Aquatherm are covered by a comprehensive 10-year warranty.
“In the case of the Novva data center, we were in constant communication with Steven Boyce and the owner’s group,” Coles said. “We were not providing a cookie cutter system to them. They would tell us whatever they wanted or needed and we would work directly with them to help them fully accomplish their goals.”
A reliable, leak-free piping system with a long life span, and a smooth installation in any space, including challenging underfloor designs? The data are in: Aquatherm is the right choice for data centers.
Broomfield, Colo. — Viega is celebrating a milestone with the tenth anniversary of the introduction of MegaPress. Press technology has been in the U.S. since 1999, and Viega has continued to release new fittings and valves to make Viega press technology an industry standard in commercial, residential and industrial applications. Viega MegaPress systems have hundreds Read more
Broomfield, Colo. — Viega is celebrating a milestone with the tenth anniversary of the introduction of MegaPress. Press technology has been in the U.S. since 1999, and Viega has continued to release new fittings and valves to make Viega press technology an industry standard in commercial, residential and industrial applications. Viega MegaPress systems have hundreds of configurations, thousands of approvals, and more than 22 million fittings sold. Over the past ten years, Viega MegaPress systems have saved contractors millions of dollars in installation costs.
Viega MegaPress and MegaPressG were the first press systems in the U.S. market engineered explicitly for gas and hydronic applications. Since the launch, MegaPress systems have expanded to include more than 200 configurations from 1⁄2” to 4” and are approved for more applications than any other carbon steel fitting system.
The value of a MegaPress system is in its unique engineering. The Grip Ring uses bi-directional teeth to provide mechanical strength and securely lock the fitting to the pipe. The sealing element provides elastomeric insurance behind the metal-to-metal contact to compensate for small irregularities of the pipe surface; this ring stays outside the flow path. The Viega MegaPress system has a long lifespan and is tested to withstand a broad range of pressures, temperatures and applications. All Viega fittings come equipped with Smart ConnectTM technology that identifies unpressed connections during pressure testing, allowing for easy identification to ensure the fittings are installed right the first time.
“In the past 10 years, labor costs have been rising while labor availability has been dwindling. It’s a perfect storm. Our MegaPress systems solve both of those challenges and help contractors across the country get more done with less. It’s a proven and trusted technology that isn’t just faster, but it’s reliable, mitigates jobsite risk because of the flameless installation, and eliminates the need for fire watch,” said Will Schneider, Product Portfolio Manager of Viega LLC.
Following the initial success of MegaPress, Viega launched MegaPressG with an HNBR sealing element approved for use in gas and fuel oil applications. Initially available 1⁄2” – 2”, MegaPressG also became the first fitting approved for connecting gas pipe up to 4”.
MegaPress FKM was added to the lineup for higher-temperature applications. With more than 180 configurations 1⁄2” to 4”, MegaPress FKM is now a staple in residential and low-pressure steam, compressed air, fire protection and fuel/oil applications.
With the rapid rise of press fitting adoption, Viega engineered a system for connecting large diameter 304 and 316 IPS stainless steel pipe. MegaPress Stainless comes with a choice of EPDM or FKM sealing elements and makes secure connections in less than 16 seconds.
In recent years, MegaPress systems expanded to meet contractor demand for a complementary valve offering. This included Viega MegaPressG Valves which come with HNBR sealing elements and are available in sizes 1⁄2” to 2”. And Viega MegaPress 3-piece ball valves are available 1⁄2” to 4” and work on potable water, hydronic water and a wide range of other system applications.
“I’ve had the opportunity to train thousands of plumbers and contractors on MegaPress systems and it’s been exciting to see the industry truly embrace this revolutionary technology,” said Troy Locke, Manager, Customer Engagement, Viega LLC. “We’re about pushing the industry forward. We’re going to continue to add more sizes, more applications and secure more approvals. In a decade, I believe we’ve only started to scratch the surface of what is possible with these types of pipe fittings and valves.”
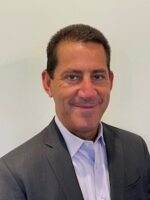
Milwaukee Valve has announced the retirement of President and CEO Rick Giannini, effective January 20, 2023. John Labellarte, the company’s current COO, will succeed Giannini in leading the commercial, industrial and marine valve manufacturer. Giannini joined Milwaukee Valve in 1998 and successfully guided the business through challenging market conditions. His leadership transformed Milwaukee Valve into Read more
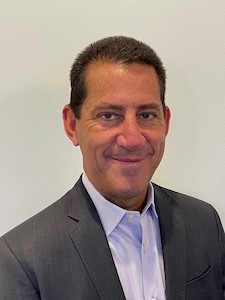
John Lebellarte
Milwaukee Valve has announced the retirement of President and CEO Rick Giannini, effective January 20, 2023. John Labellarte, the company’s current COO, will succeed Giannini in leading the commercial, industrial and marine valve manufacturer.
Giannini joined Milwaukee Valve in 1998 and successfully guided the business through challenging market conditions. His leadership transformed Milwaukee Valve into a service leader and global manufacturer. He guided the transformation of the sales organization, reinvested in manufacturing processes and equipment, and assembled the company’s overseas manufacturing operations. Giannini greatly expanded the development and growth of Milwaukee Valve’s product offering and presence in the Navy Marine market.
Giannini also developed and maintained the management team which will continue to lead the company. He dedicated time and energy to industry-leading organizations, serving as Chairman of the Aircraft Carrier Industrial Base Coalition (ACIBC) since its inception in 2004. He also sat on The American Supply Association’s (ASA) Industrial Piping Division Steering Committee and served on ASA’s Board of Directors.
New president and COO John Labellarte started with Milwaukee Valve in 1999 as General Manager. He was promoted to Vice President and COO in 2006. During his tenure, Labellarte has been instrumental in driving the company’s global manufacturing initiatives, strategic planning, product development and operational performance. His focus on continual improvement and the utilization and development of new technologies will continue to build brand value and value proposition for the company. Prior to joining Milwaukee Valve, Labellarte worked for 12 years with the Marpac & McCANNA Valve companies, serving in operations and management roles. He is extremely qualified to lead Milwaukee Valve, with 35 years of executive and operations management experience in the valve industry.
In its 121st year of business, Milwaukee Valve Company is internationally recognized for state-of-the-art manufacturing facilities and innovative new products covering a wide range of commercial and industrial applications.
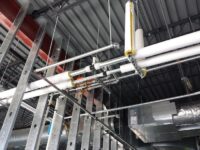
By Aaron Stotko When a century-old Dallas railroad company headquarters required major renovations to transform into a Homewood Suites by Hilton, initial cost estimates for the hydronic heating system came in too high. That’s when City Wide Mechanical of Dallas looked to alternative piping systems for a solution. They found PEX-a pipe with F1960 expansion Read more
By Aaron Stotko
When a century-old Dallas railroad company headquarters required major renovations to transform into a Homewood Suites by Hilton, initial cost estimates for the hydronic heating system came in too high.
That’s when City Wide Mechanical of Dallas looked to alternative piping systems for a solution. They found PEX-a pipe with F1960 expansion connections to be the ideal system, due to its durability and ease of installation in addition to the job-site productivity, safety and, best of all, profitability potential it provided.
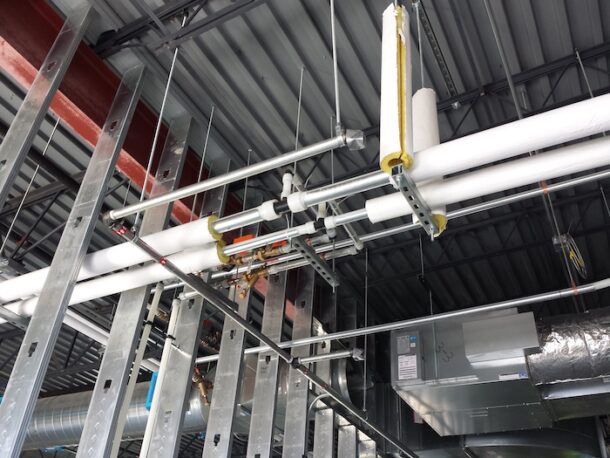
And City Wide Mechanical isn’t alone in their findings. Many mechanical contractors are discovering the benefits of PEX-a pipe and F1960 connections as the preferred alternative to copper, iron, and steel, which have dominated the mechanical piping industry for decades.
Benefits of PEX-a
PEX is an acronym for crosslinked polyethylene. It has been used in North America since the mid-1980s, starting with radiant floor heating systems, then moving into plumbing and, eventually, to hydronic hot-water heating and chilled-water applications.
PEX can be manufactured via three different processes, which create products with varying crosslinking percentages that allow for different characteristics. PEX-a is the most durable, flexible, and resilient with crosslinking around 85%. PEX-b is a stiffer piping product with crosslinking around 65% to 70%, and PEX-c features crosslinking around 70% to 75%.
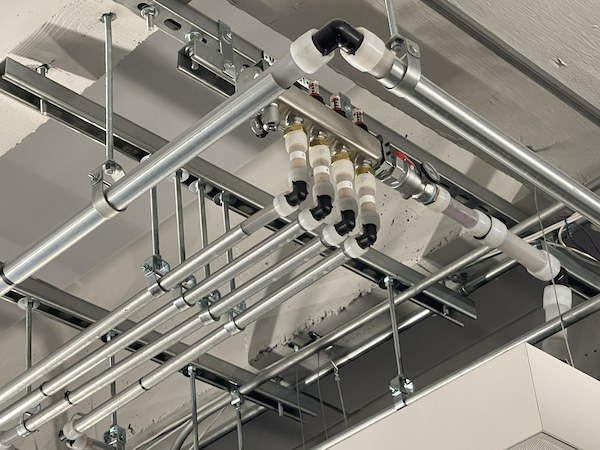
ASHRAE Headquarters Grand Opening Fall 2021, photos by Devin Abellon
One major benefit of the higher crosslinking in PEX-a is its extreme flexibility along with its thermal and shape memory. The flexibility of PEX-a eliminates most connections in smaller-diameter piping, saving time and money with up to half the connections required in rigid metal piping systems. To make a change in direction, the installer simply bends the pipe instead of having to stop and make a fitting. There are also bend supports available that help hold a bend securely in place.
The thermal memory of PEX-a provides kink repairability with a simple shot of heat from a heat gun. This eliminates the need to add in a coupling if a kink ever occurs in the pipe. (It is important to note that kink repairability is not possible with PEX-b or PEX-c pipe.)
The shape memory of PEX-a allows the pipe to expand and contract back down to its original shape. This makes it extremely resilient in freezing conditions and also provides for the fastest, easiest, most reliable PEX-a fitting system — F1960 expansions.
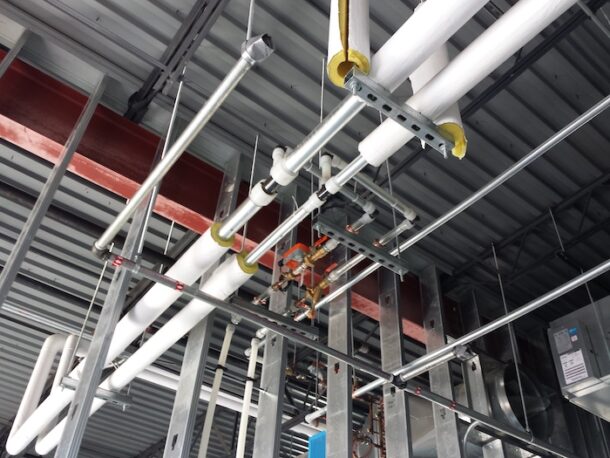
Expansion fittings require one simple tool to expand the pipe and an expansion ring before inserting a fitting. As the pipe and expansion ring naturally shrink back to their original shape, it creates a strong, durable connection that holds tight and can never be dry-fit. (Note: It is not recommended to expand PEX-b or PEX-c pipe due to microcracking that can occur.)
The innovative expansion fitting method eliminates torches, glues, and solder from a job site for greater worker safety. Plus, the system is extremely easy for installers to learn, helping get new crews up to speed quickly.
Speaking of job-site safety, PEX is also much lighter in weight compared with metal systems. For example, a 300-foot coil of 1/2-inch PEX weighs about 18 pounds, whereas the same amount of copper pipe weighs around 85 pounds. The lighter weight of PEX makes it safer and easier for installers to move around a job site and also eliminates the need for heavy-lifting equipment.
PEX-a also has a long-term advantage over copper when it comes to performance longevity. It is a static system, meaning its internal surfaces — which are three times smoother than copper — will not pit, scale, or corrode. That means its performance will remain the same from day one through decades of use.
Finally, because it is not a traded commodity, PEX-a holds a relatively stable material cost. This makes bidding a project much more consistent and reliable.
Application Details and Installation Tips
PEX-a is regulated by the ASTM F876 standard, which denotes temperature and pressure ratings of 200°F at 80 psi (pounds per square inch), 180°F at 100 psi, and 73.4°F at 160 psi. These values are well within the range of operation for most hydronic systems, including chilled beams, fan coil units, baseboards, radiators, hydronic VAV (variable-air volume) reheat coils, and radiant manifolds.
Because PEX is oxygen-permeable, it is important to use a pipe with an oxygen barrier that limits oxygen diffusion to levels below DIN 4726. This will protect the metallic components in the mechanical piping system, such as valves, strainers, and pump volutes, from corrosion.
The pipe is manufactured in sizes from 5/16 inch up to 4 inches and features a copper tube size (CTS) outside diameter. This means all the off-the-shelf components used in a copper hydronic piping system — hangers, supports, and insulation — can be the same.
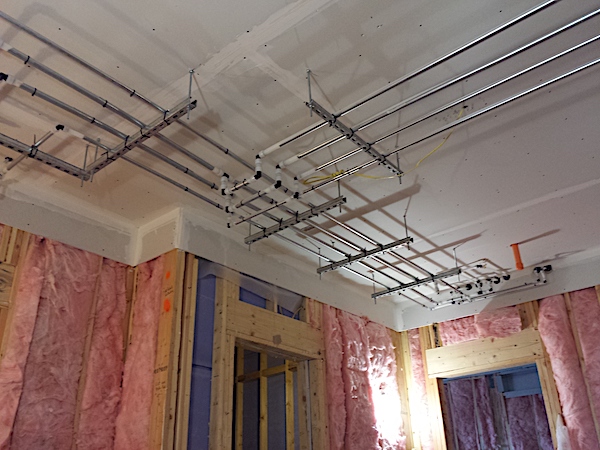
For horizontal piping, the industry offers PEX-a Pipe Support — a galvanized-steel channel that is 9 feet in length and available in PEX pipe sizes from ½ inch to 3½ inches. This solution enables hanger spacing similar to copper pipe and helps control the natural expansion and contraction of the pipe as it heats and cools.
Because PEX-a expands at 1.1 inches per 100 feet per 10°F Delta T (which is 10 times that of copper), installing anchors every 65 feet and using PEX-a Pipe Supports allows PEX-a to function much like a copper system. In fact, different installation methods have a different effect on the overall net expansion rate.
With a strut-and-clamp system, using PEX-a Pipe Supports and anchoring with fixed points reduces the expansion rate of PEX-a to 0.08 inches per 100 feet per 10°F Delta T (a rate less than copper). And a loop-and-clevis system can reduce the rate to 0.12 inches per 100 feet per 10°F Delta T.
If you’d like to learn more about PEX-a piping systems, visit the Plastics Pipe Institute at plasticpipe.org or the Plastic Pipe and Fittings Association at ppfahome.org.
Aaron Stotko is the director of Segment Marketing at Uponor. He can be reached at aaron.stotko@uponor.com.